AGC Research Report 71(2021)
サンドペーパー落下試験におけるカバーガラス破壊現象の解析
Analysis of fracture mechanism in sand paper drop event for cover glass
金原一樹*・今北健二**・小林裕介***・小池章夫*
Kazuki Kanehara, Kenji Imakita, Yusuke Kobayashi and Akio Koike
*AGC株式会社 技術本部 材料融合研究所
**AGC株式会社 電子カンパニー
***AGC株式会社 技術本部 先端基盤研究所
スマートフォンやタブレット端末には広くカバーガラスが用いられている。カバーガラスに求められる最も重要な性能は高い落下強度を持つことである。しかし、落下破壊現象は動的な現象のため解析が難しく、加えてガラス強度自体のばらつきも相まって、これまで落下破壊現象に関して定量性のある議論はほとんどなされていなかった。そこで本研究では、サンドペーパー落下試験における破壊メカニズムの解明を行い、落下強度の定量化を行った。まず、高速度カメラを用いてスマートフォン落下試験時の様子を観察した。その結果、スマートフォンが落下し、サンドペーパーに接触して割れる現象では①サンドペーパー接触時にクラックが発生②筐体がたわむことによる曲げ応力の発生に伴い、クラック先端に応力が集中してガラスが破壊することが分かった。次に、様々なサンプルで落下試験を行い、破壊後のガラスの破断面を観察することで、発生したと考えられるクラック深さを測長した。その結果、ガラスがサンドペーパーに当たった際に発生するクラック深さが明らかになり、傷の進展を止めるために重要な化学強化応力プロファイルを見いだした。最後に得られた知見に基づきガラスの物性と応力プロファイルから落下高さを定量的に計算する手法を確立した。これにより、実際の落下試験を行うことなく、落下強度が定量的にわかるようになった。また、本研究成果を用いることで、スマートフォン用に用いられているカバーガラスの強度を高めるために必要なスマートフォン筐体の構成やガラス物性が明らかになった。
Fracture mechanism of cover glasses in a drop event was investigated through high speed camera observation and conventional fracture surface analysis. Drop tests were performed for various chemically strengthened glasses with different mechanical properties and stress profiles. These were dropped on 180 grit sandpapers. Based on the observations, it was found that the fracture of cover glasses in the drop tests is caused by two consecutive steps. The first one is nucleation of a crack due to the contact between the protrusions of the sandpaper and the glass, which causes a strong tensile stress localized around the protrusions. The second one is the propagation of the crack due to a tension caused by bending of the smart phone during the rebound process after the first contact with the sandpaper on the ground. According to these investigations, we established a prediction formula for the “fracture drop height” for the sandpaper drop tests. It enables us to understand key parameters to improve the fracture drop height. Key factors to improve the fracture drop height should be not only the mechanical properties of the cover glass and the body of the smartphone but the stress of cover glass induced by chemical strengthening.
1. 緒言
現在、スマートフォンをはじめとしたモバイル機器は世界中で幅広く使用されており、こうしたモバイル機器のディスプレイを保護するためにカバーガラスが用いられる。ディスプレイをしっかり守れる強いカバーガラスを作るために、カバーガラスの登場以降様々な製品が開発されているものの、依然としてカバーガラスの破損に伴うモバイル機器の返品が起きていることから、カバーガラスにはさらに高い強度を持つことが求められている。割れないカバーガラスへの強い要求に応えるため、これまでカバーガラスの割れ方について様々な研究が行われてきた[1,2]。既往の研究によって4点曲げ試験やビッカース圧子を使った試験などの準静的な破壊現象に対する理解は進んできている。例えば、4点曲げ試験やディスプレイ接触面からガラスが割れる現象に対して強度を向上させるためには、ガラスの表層部に強い圧縮応力を入れることが重要であることが分かっており、そのために現在用いられている多くのカバーガラスには化学強化処理がなされている。化学強化処理とは元々ガラス中に含まれるアルカリイオンよりも大きなイオン半径を持つアルカリイオンを導入する処理を指す[3]。例えばナトリウムイオンを持ったガラスを、カリウムイオンを含む溶融塩に浸漬させることでガラスと溶融塩中のアルカリイオンを交換することができ、それぞれのイオン半径の違いを利用してガラスに強い圧縮応力を導入することができる。この処理を行うことで、ディスプレイ接触面から割れる現象には強くなる。一方従来の研究では、人の指と接触する面側からの破壊現象に関しては十分な理解ができていなかった。人の指と接触する面側からの破壊は、カバーガラスの割れとして市場で最も見られる現象であり、実験系としてはサンドペーパー等の粗い面に対してスマートフォンを落下することで、市場で発生する割れの主要な割れモードを再現できることが分かっている[2]。
そこで本研究では、人の指が接触する面側からカバーガラスが破壊する現象の理解を目的とした。サンドペーパーに対してスマートフォンを落下試験した場合におけるカバーガラスの破壊メカニズムを、高速度カメラによる観察とガラスの破面解析を行うことにより調査した。
2. スマートフォン落下破壊試験の観察
本研究では、カバーガラスが人の指と接触する面側から割れる際、どのようにして破壊するのかを理解するために、高速度カメラを使用してスマートフォンの落下試験の様子を観察できる実験系を用意した。
スマートフォン筐体を自由落下させたときの様子をFig. 1に示す。Fig. 1(a)はスマートフォンが初めてサンドペーパーに接触する瞬間の映像である。落下試験を行うとまず、サンドペーパーに当たることでガラスに傷がつくものと考えられる。次にFig. 1(b)にFig. 1(a)の状態から約0.5秒後の様子を示す。スマートフォンがサンドペーパーに当たった後でリバウンドし、その間にスマートフォンの筐体全体が曲がっていることが確認できる。これらの写真から、サンドペーパー落下試験におけるカバーガラスの破壊プロセスは、Fig. 2に示すように、①カバーガラスがサンドペーパーに接触しクラックが入り、②落下後のリバウンド時にスマートフォンの筐体が曲がることで傷先端に応力が集中してガラス全体が割れるという2つの連続したステップで構成されていることが推定される。
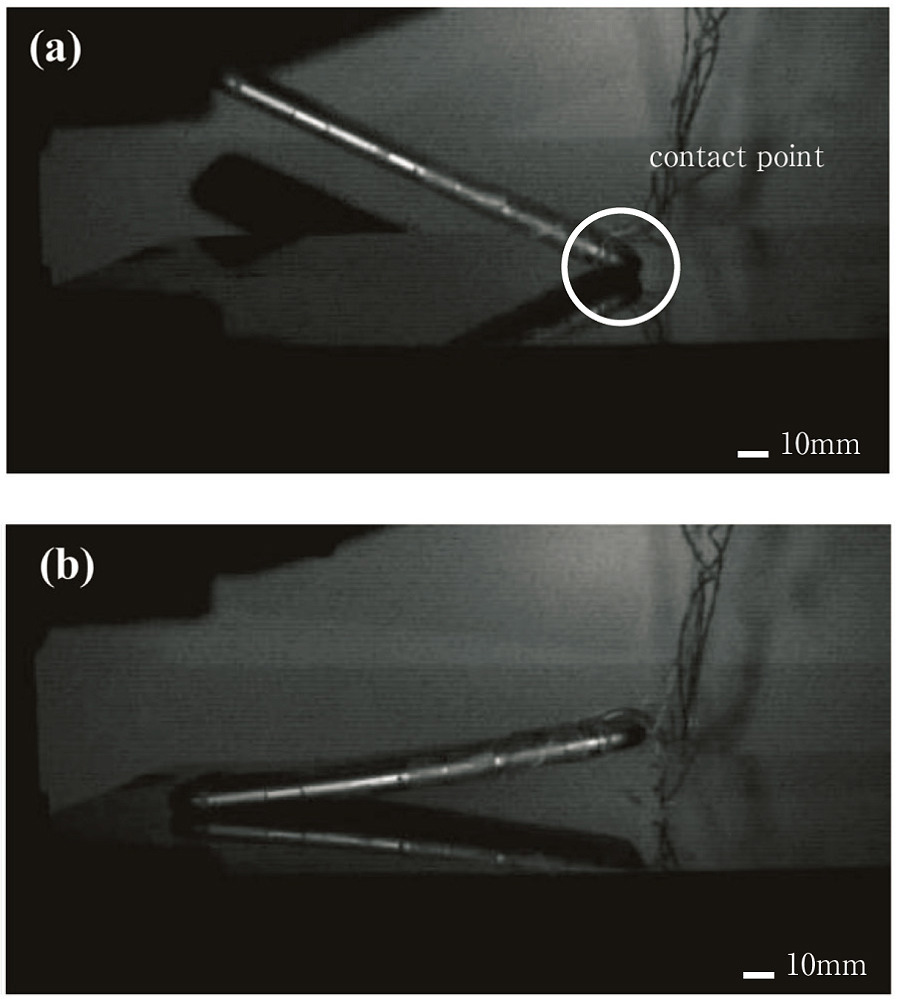
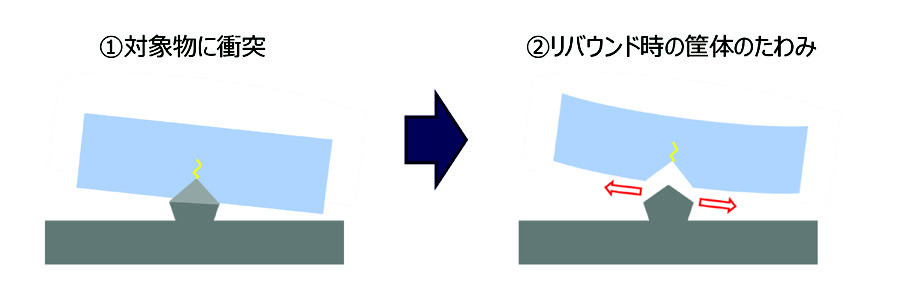
3. 落下後試験サンプルの観察
前章でサンドペーパー落下試験時には①サンドペーパーにカバーガラスが接触することで、カバーガラスにクラックが入り②筐体がたわむことでクラック先端に応力が集中し、カバーガラスの破壊が起こっていると推定した。そこで①のクラックが入る部分を理解するために落下試験後のガラスの破断面観察を行い、サンドペーパーとの接触時に発生するクラックの長さを調査した。落下試験に用いたのはFig. 3に示すような50×50×0.7 mmのガラスサンプルをポリカーボネート製の筐体に貼り、さらにスチール製の板を取り付けた模擬筐体である。なお、総重量は典型的なスマートフォンと同じ148 gにした。また、試験時は垂直自由落下となるよう、姿勢を制御して落下試験を行い、ガラスが当たる対象には市場で発生する割れの一部を再現できる番手180番のSiC製サンドペーパーを選択した。なお、このサンドペーパーは粒径63~75 µmの粒子で全体の90%以上が構成されている。落下させたガラスはソーダライムガラスとアルミノシリケートガラスであり、落下高さは50,100,150 cmの3水準を行った。なお、試験はバラツキを考慮して各条件で30回ずつ行った。
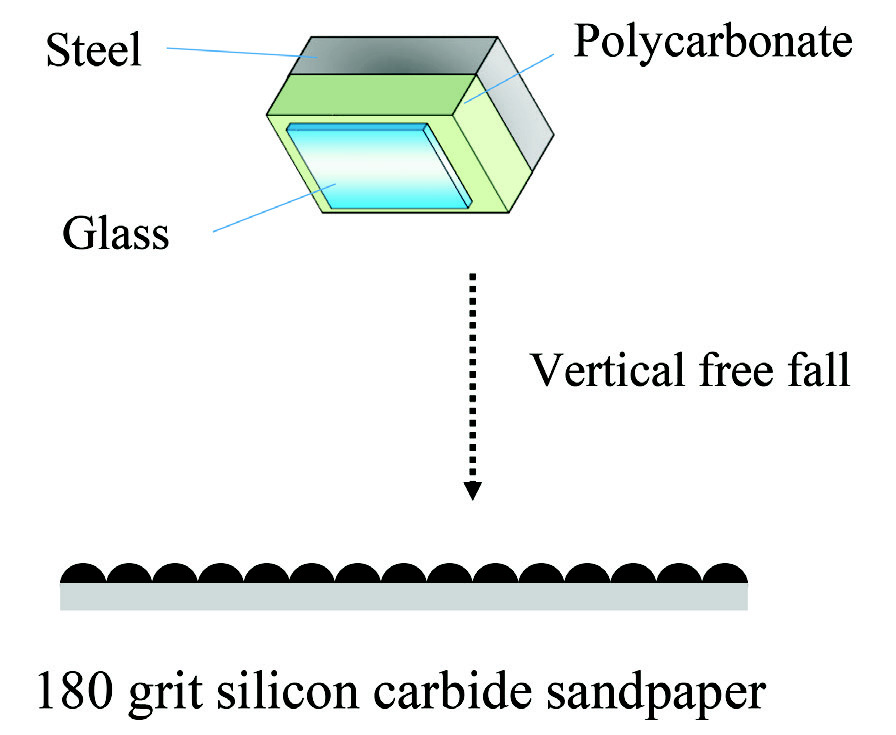
Fig. 4に落下試験後サンプルの破断面を観察した代表的な写真を示す。このうちガラス表層から見てガラスがえぐれてなくなっている部分までの深さをDamage深さと定義する。また、表層から半円状に広がっている模様がガラス表面から垂直方向に発生したクラックの痕跡である。このうち、最初の半円状の跡までの深さをクラック深さと定義する。クラック深さと落下高さの相関をFig. 5に示す。赤いプロットがソーダライムガラスの平均クラック深さであり、青いプロットがアルミノシリケートガラスの平均クラック深さである。なお、エラーバーとして記した値は全データから四分位数を算出し、Q3とQ1に当たる値を記載した。Fig. 5から分かるように、180番のSiC製サンドペーパーにガラスが接触した場合、ガラスの種類や落下する高さに関係なく、おおよそ50~60 µmのクラックが発生することが確認できた。
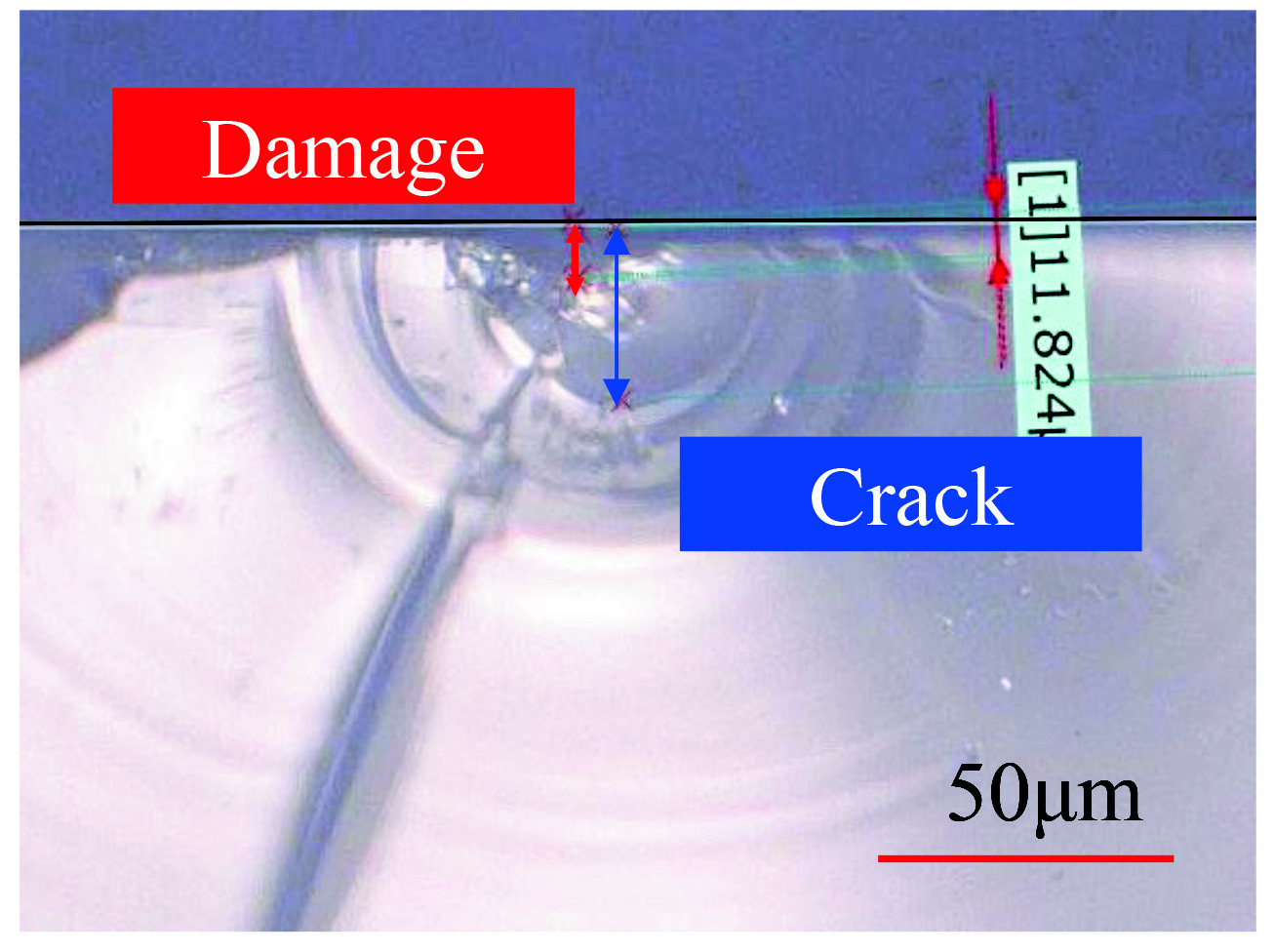
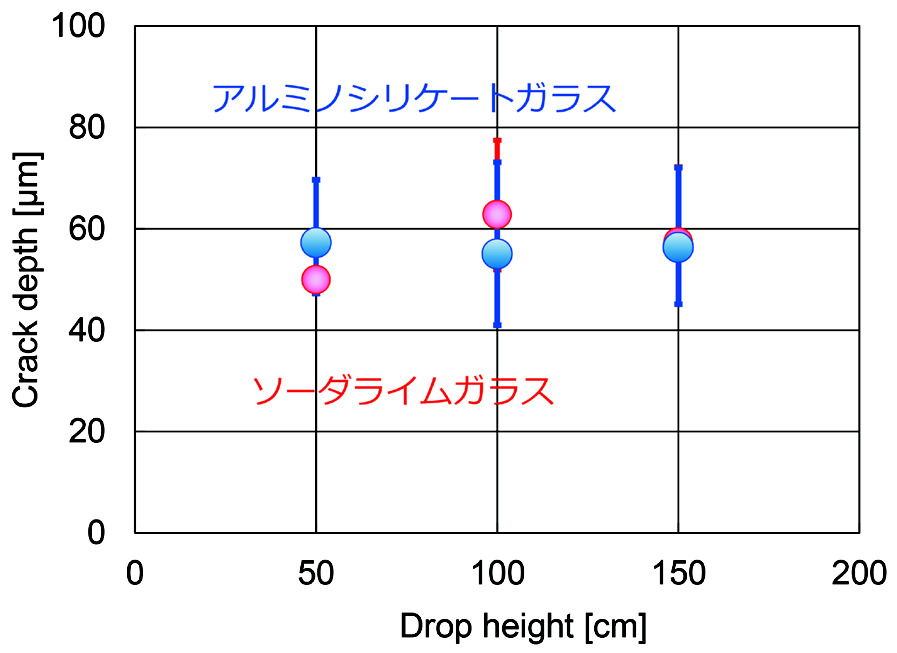
4. 落下破壊高さ予測式の構築
この章ではガラスにクラックが発生した後、筐体がたわむことでクラック先端に応力が集中する過程を考える。ガラスが破壊するという現象は、亀裂の開口に絞って考察すると、ガラスに存在する傷先端にかかるいくつかの力のうち圧縮応力よりも引張応力が大きくなり、かつその応力の大きさがガラスの耐えられる応力を超えてしまった場合に生じる現象と考えられる。上記を考慮し、落下試験時に発生する応力を考えると、引張応力として「ガラス表面に発生する曲げ応力」、圧縮応力として「クラック領域深さにおける化学強化応力」、ガラスの耐えられる応力として「ガラスの破壊靭性由来の耐久力 」の3つの力を考慮すれば良いことが分かる。上記をまとめるとFig. 6のような力の関係になる。
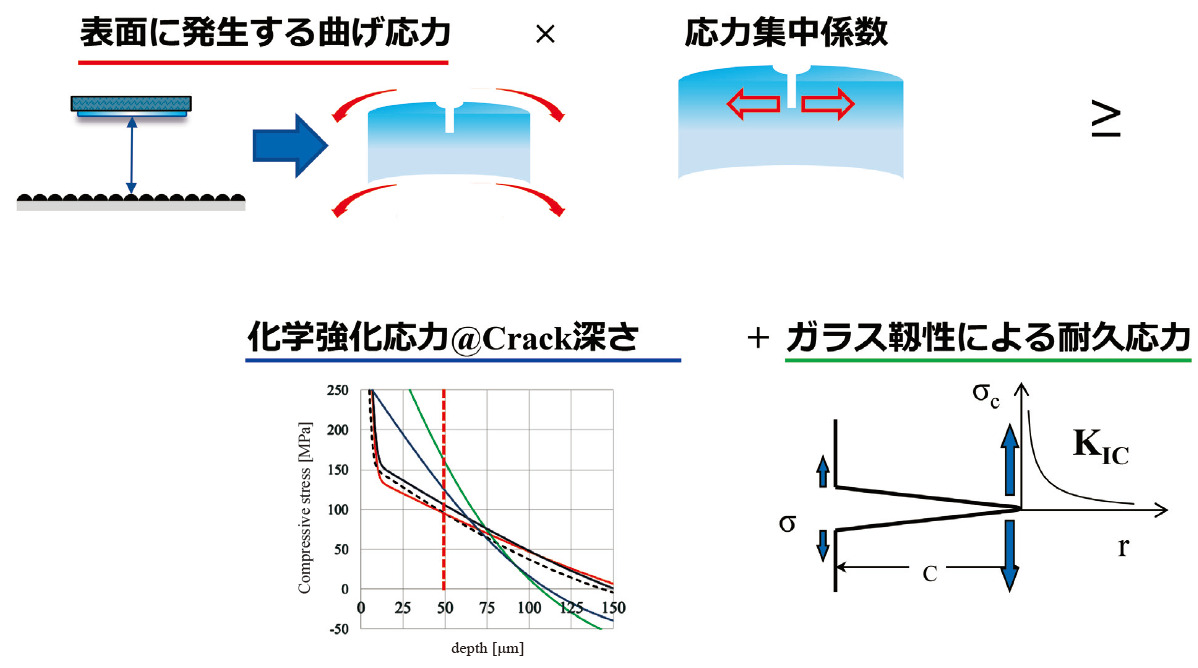
それぞれの力について考えていく。まず、「ガラス表面に発生する曲げ応力」についてエネルギー論を元に考える。スマートフォンの落下する前の位置エネルギーUと落下後のスマートフォン全体の曲げのエネルギーUを等しいとした場合、ガラスの表面に発生する応力σglassは次の式(1)の関係を利用して、式(2)のように表すことができる。
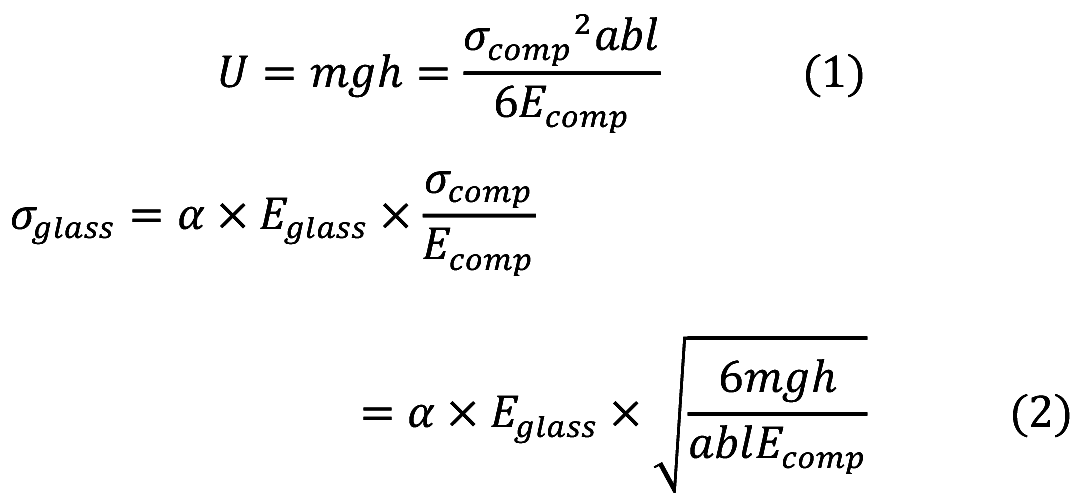
なお、mはスマートフォン全体の重さ、gは重力加速度、hは落下高さ、σcompはスマートフォン自体に発生する応力、σglassはガラス表面に発生する応力、a,b,lはそれぞれスマートフォンの長辺、短辺、厚みを示す。また、Eglassはガラスのヤング率を示し、Ecompはスマートフォン全体のヤング率を示し、αは落下したスマートフォンが曲げ以外にエネルギーを使用することを考慮した補正係数であり、スマートフォンが落下した際に音などにエネルギーを散逸し、落下前の位置エネルギーの全てが曲げのエネルギーに変換されないことを想定している。なお、本研究においてαはガラスの種類に寄らず一定の値としたが、特別にエネルギーを散逸しやすいなどの特徴がある場合は、ガラスの種類に応じて変える必要がある。この式から導いた落下高さと表面に発生する応力の関係をFig. 7に示す。cal.の値は(2)式から導いた計算値であり、exp.の値はスマートフォンのモック表面に歪ゲージを取り付け、落下試験を行った際に計測した歪値から求めた応力値を示す。計算値と実測値は大まかには一致していることが確認できる。
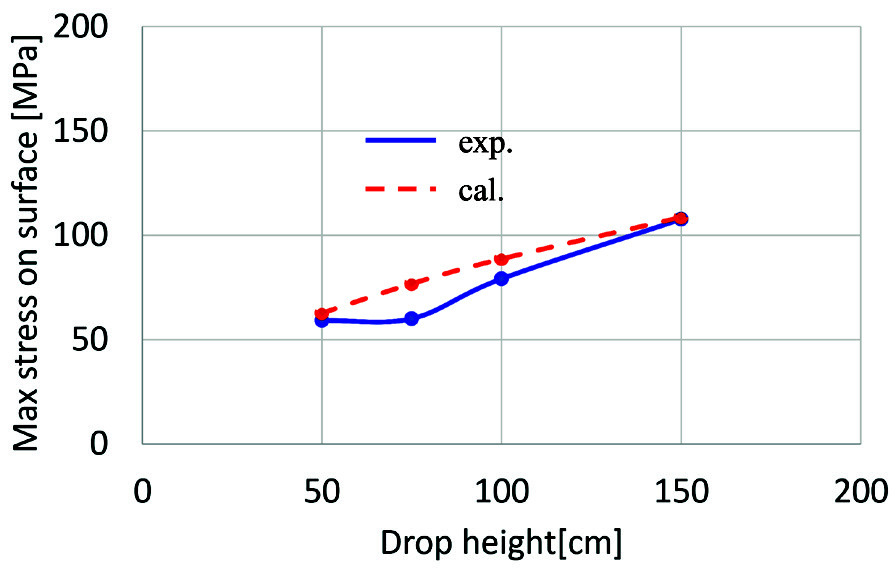
次に、「クラック領域深さにおける化学強化応力」について考える。この値は3章で示した通り、180番のSiC製サンドペーパーにガラスが接触した場合、ガラスの種類や落下する高さに関係なく、おおよそ50~60µmのクラックが発生することから、化学強化後のガラスにおける表層から50µm深さの位置の圧縮応力の値を考えれば良い。
最後に、「ガラスの破壊靭性由来の耐久力」について考える。ガラスの破壊靭性由来の耐久力として、式(3)に示すGriffithのモデル[4]が適用できると仮定した。
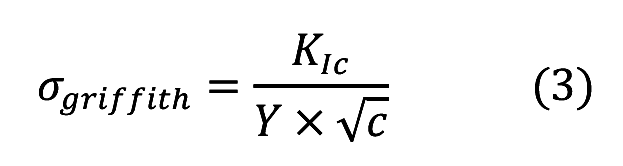
なお、σGriffithはガラスの耐久力、KIcはガラスの破壊靭性値、Yは形状因子であり今回は表面の補正係数と呼ばれる1.12を使用し、cはクラック長さを示す。
なお、griffithの式は本来静的な現象に対してのみ適用できるが、今回はスマートフォンの曲げがガラスのクラック進展速度よりも優位に遅いものと考え、スマートフォンの落下時の曲げという動的現象にも適用できると仮定して使用している。
落下破壊の状況での応力のバランスを考えるとガラスの割れる瞬間の力のつり合いは次の式(4)のようになるはずである。

なお、σtempはクラック先端の化学強化応力を指す。Fig. 6に示した力のつり合いとこれまでの式(1)~(4)までを利用すると、落下破壊高さhは次の式(5)のように表すことができる。
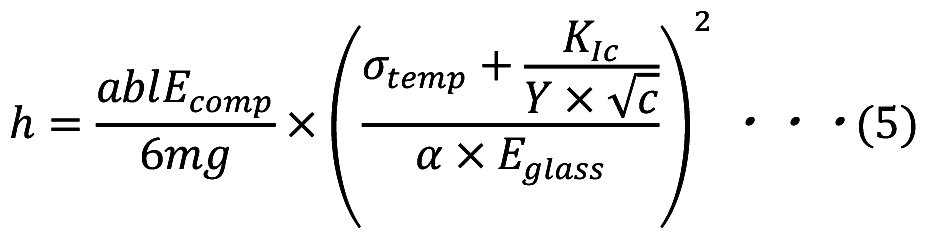
なお、落下破壊高さhとはカバーガラスを10cmの高さからスタートして、割れなかった場合は5cmずつ落下高さを上げ、最終的にカバーガラスが割れた落下高さの平均値のこととする。
Fig. 8に(5)式を用いて算出した落下破壊高さと様々なガラスを用いて落下試験を行い実験的に得た落下破壊高さの相関を示す。
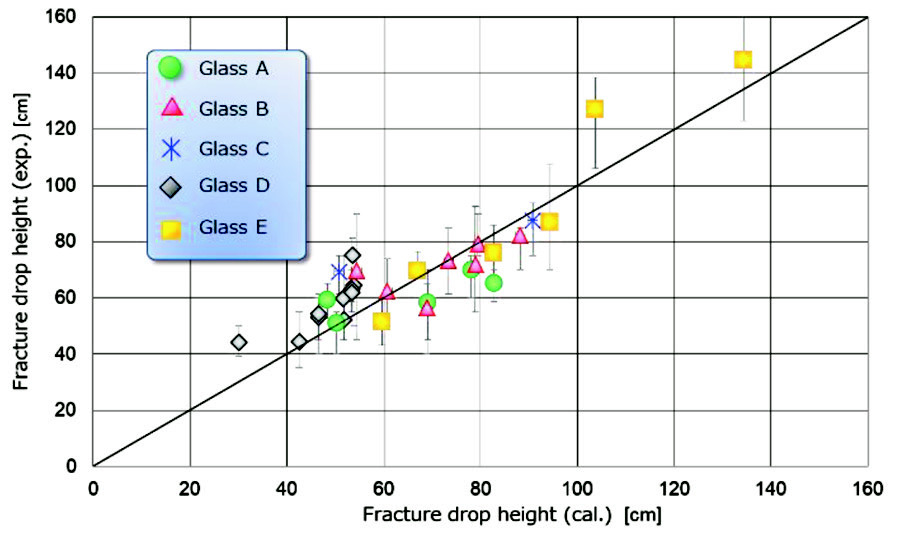
落下させるスマートフォン筐体には、138.4×67.3×0.7 mmのガラスサンプルにアルミニウム製の金属板ブロックを接合させたものを使用した。また、上記2つを接合したスマートフォン筐体は、総重量が一般的なスマートフォンと同じ148 gになるように調整されている。また落下に用いたA~Eのガラスは化学強化によって付与した圧縮応力がそれぞれ異なるリチウム含有アルミノシリケートガラスやリチウム非含有のアルミノシリケートガラスである。
式(5)によって得られた値は実験値を予測可能なことを示しており、落下破壊高さを定量的に示すことができるようになった。また、この式によって落下破壊高さを上げるうえでポイントとなるパラメーターを理解することができる。例えば落下高さを上げるためには、スマートフォンの質量mを下げ、スマートフォンのサイズであるa,b,lの大きさを上げ、スマートフォンの筐体のヤング率を高めることがスマートフォン側の設計として有効なことが明らかになった。なお、クラック深さや発生応力はモックによって変化する可能性があり、筐体の複数のパラメーターが変化した場合、定量的な比較をするのは注意が必要である。また、式の適用範囲として理論的には幅広いガラス系に適用可能だが、あらゆるガラス種やサイズに対して実証を行っていないので、この点も注意が必要である。ただし、定性的には正しい現象を表していると考えており、落下強度を向上させるためにガラス側にできることとして、化学強化の圧縮応力の大きさを上げること、またガラスの破壊靭性値であるKIcを高めることが有効なことを示した。
5. 総括
スマートフォンに用いられるカバーガラスの落下破壊メカニズムを調査し、落下破壊強度を定量化した。カバーガラスの落下破壊現象を高速度カメラを用いて観察し、落下破壊現象が①サンドペーパー接触時にクラックが発生②筐体がたわむことによる曲げ応力の発生に伴い、クラック先端に応力が集中してガラスが破壊するという2つのステップによっておこる現象であることが分かった。さらに実際の落下試験で得られるサンプルの破断面観察を通して、180番のSiC製サンドペーパーに落下させた際にはガラスの種類や落下高さによらず、50~60 µmのクラックができることをが明らかになった。また、カバーガラスが割れる際に発生している応力を推定し、数式にすることで落下破壊強度を定量化することができた。今後は本知見を用いてより高強度なガラスを作製していくと共に、サンドぺーパー以外の様々な物質に接触した際の落下破壊メカニズムも解明していきたい。
参考文献
- K. Hayashi, S. Akiba, T. Sakagami, S. Sawamura, T. Nakashima and H. Ohkawa, SID’12 digest 43, No. 1, 1584–1587 (2012).
- H. Ohkawa, Y. Kobayashi, S. Akiba, K. Hayashi, T. Nakashima, A. Nakagawa, H. Saiki, N. Ishimaru "Product design for strong cover glass," SID’15 digest 23, No. 3, 119-128 (2015).
- R.F. Barthoromew and H.M. Garfinkel, "Glass: science and technology," Academic Press:New York (1980), p. 217.
- A. A. Griffith, "The phenomena of rupture and flow in solids," Phil. Trans. Royal Soc. London, Series A 221, 163–198 (1921).