エレクトロニクス
ダイナミックに変化するエレクトロニクス市場。その目まぐるしい動きにあわせて、技術革新も加速しています。そんな世界で、半導体分野、オプトエレクトロニクス、スマートフォン・タブレット向けに、次代を担う高機能部材・部品を次々と求められています。
次世代高速通信が社会を大きく変えようとしている現在、次の変化を実現するために必要な素材・ソリューションは何か、マーケティング力と技術力を結集し開発を加速しています。
開発ストーリー紹介:EUV露光用マスクブランクス
EUVマスクブランクスの技術を垂直統合し、実用化への道を切り開く
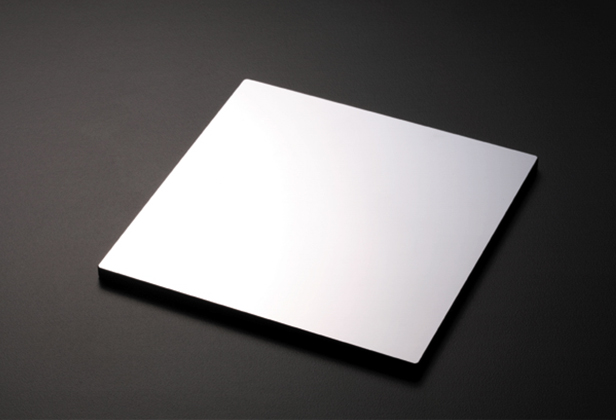
次世代半導体製造プロセスの部材開発に着手
ビッグデータ、AI、高速データ通信、VR…今、産業界に「100年に一度」と言われる技術革新の波が起きようとしています。この大変革の隠れた主役ともいうべきものが、LSIや超LSIなどの半導体チップです。計算処理の高速化、データの大容量化、高集積化によって電子機器はより高機能に、より小型になり、その流れは強まりこそすれ弱まることはありません。
こうした半導体チップの進化とは、半導体回路パターンの微細化にほかなりません。一般に、半導体回路パターンの形成には光リソグラフィ技術が用いられます。これは、フォトマスクと呼ばれるガラス基板に描画された回路パターンを、露光装置を介してシリコンウエハー上に転写する技術です。その線幅は20nm(ナノメートル、1nm=10億分の1m)が理論的な限界値とされ、より微細な回路パターンを形成するためには、次世代半導体製造プロセスが必要となります。それがEUV(極端紫外線)露光技術です。
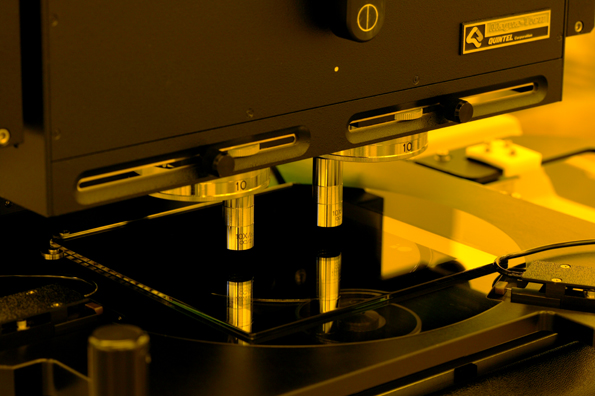
光リソグラフィ技術では、光源として波長が193nm以上のKrF(フッ化クリプトン)やArF(フッ化アルゴン)が用いられます。これに対してEUVは波長が13.5nmで、10nm以下の線幅が可能となります。 20nmの線幅の回路パターンを形成するためには、光リソグラフィを複数回適用する必要があり、複雑かつ高コストなプロセスでした。一方、EUVは、10nm以下の線幅の回路パターンを1回で形成できるため、光リソグラフィのような複雑なプロセス技術が不要というメリットもあります。
AGCがEUV露光技術に用いられるマスクブランクスの研究開発に着手したのは2003年のこと。以前から開発していた半導体向け合成石英ガラスの高い技術と品質が、グローバルな半導体技術開発コンソーシアムである米国International SEMATECH(セマテック)から認められ、マスクブランクス開発に向けたプロジェクトへの参画を要請されたことがきっかけでした。
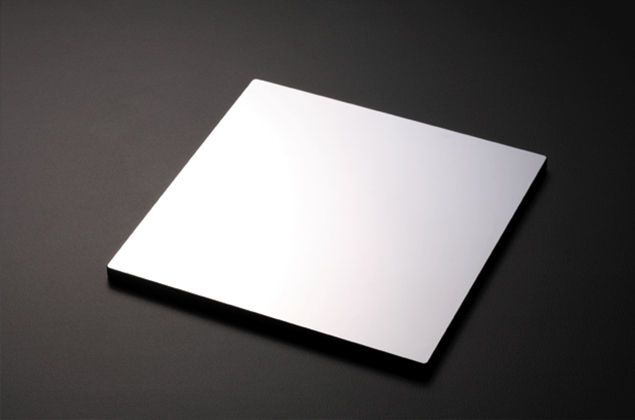
マスクブランクスとは、低膨張ガラス基板の表面に複数の組成からなる膜を積層したフォトマスクの原版で、EUV露光技術の中核をなす最も重要な部材です。AGCは、ガラス材料から研磨、成膜までの技術を垂直統合した世界で唯一のマスクブランクス・メーカーとなることを目標に設定しました。
要求精度は従来の10分の1のレベルに
さっそく、セマテック等が設立したマスクブランクス開発センターに研究員を送り込んで共同研究を行うとともに、社内でも独自プロセスの開発に向けたプロジェクトが立ち上がりました。
「まったくゼロからのスタートであり、しかも要求水準が非常に高いので、できるかどうかわかりませんでした。しかし、AGCにとって大きなチャンスであり、一技術者としても挑戦しがいのある面白いテーマでしたので、全力で取り組むことにしました」と語るのは、米国での研究を経てプロジェクトの牽引役を務めてきた研究員です。
では、求められる水準とはどれほど厳しいものなのか。ブランクスのサイズは約15cm(6インチ)。その表面の平坦度を150mの野球グランドに当てはめると、許容される表面の凹凸は13.5ミクロン以下となります。さらに、スギ花粉ほどの大きさの異物が数個以下でなければなりません。露光装置で用いられる光源の波長が193nmから13.5nmになったため、要求される平坦度も欠点も、一気に10分の1の水準になったのです。
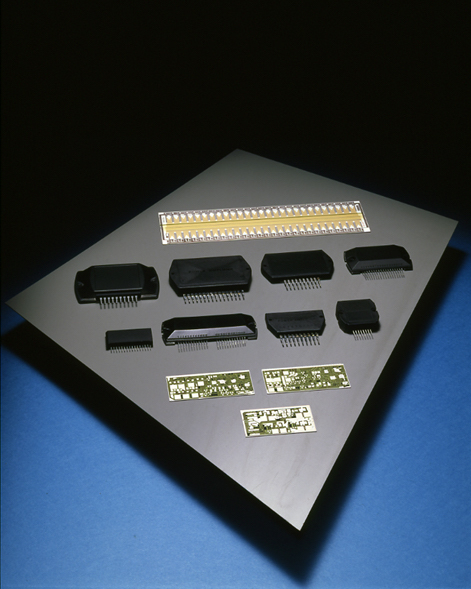
それ以外にも、お客様である半導体メーカーからは50種類以上の品質要求が出されていました。実用化のためには、それらの「関所」を一つずつ通過しなければ前に進むことはできません。これほど難易度の高い開発だけに、当初は失敗の連続で、満足できるガラス基板は1枚も採れませんでした。
しかも、当初4〜5年での実用化を計画していた開発スケジュールは、さまざまな要因によって延期に継ぐ延期を余儀なくされました。いつになったら実用化できるのか、実用化しても使ってもらえるのか、といった重苦しい雰囲気にプロジェクトメンバー全員が包まれました。そんなムードを打ち破ったのが、愚直なまでの開発姿勢と、チームワークでした。
何か画期的なブレークスルーがあったから実用化できたというわけではありません。問題を解決するために、原因の推定、対策の立案、対策の効果検証、を繰り返し行い、それを一つずつ積み上げていきました。また、要求品質を、単独の工程ではなく、ガラス材料作製・ガラス加工・成膜といった複数の工程で実現する必要があります。駅伝のように、自分の責任を果たした上で、その成果を次の走者(工程)に渡していくことによって、厳しい要求品質をクリアしていきました。
的確な投資判断で開発現場をバックアップ
そうした開発現場の苦闘と同時に、経営陣による的確な投資判断があったことも見逃せません。ある一定額以上の投資に対しては、経営会議を何度もパスしてようやく認められるのが一般的ですが、それを待っていてはタイミングを逸することがあります。とりわけマスクブランクスのような最先端でしのぎを削る技術開発においては、時間が成否を分けることも珍しくなく、的確な投資判断が必要となります。
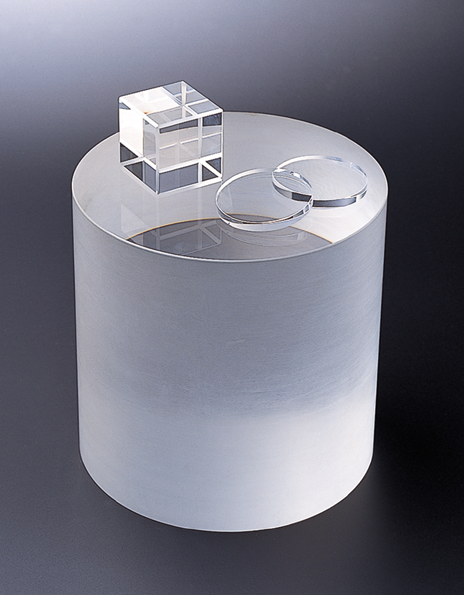
そうした姿勢の背後には、エレクトロニクス分野を事業の柱に育てようという一貫した強い意志があります。そんな経営陣の姿勢が現場のモチベーションを上げ、開発を進めるための推進力となります。マスクブランクスの開発は、その好例と言えるでしょう。
こうした関係者の懸命の取り組みによって、開発にメドがついたのは2014年前後のこと。これを受けて、2018年2月には供給体制の大幅増強が決定しました。この事業が軌道に乗れば、半導体製造の分野においてAGCは大きな存在感を発揮できるばかりでなく、産業界全体の発展にも大きく貢献できます。
EUVマスクブランクスの開発が始まってから15年。強いプレッシャーにさらされながら技術開発に打ち込んだプロジェクトメンバーの夢が、ようやく現実のものになろうとしています。