AGC Research Report 71(2021)
真球状中空シリカナノ粒子の開発
Spherical Hollow Silica Nano Particles with Dense Shell Structure
荒井雄介*・松原俊哉*・金賢枝*・山田和彦**
Yusuke Arai, Toshiya Matsubara, Hyunji Kim, and Kazuhiko Yamada
*AGC株式会社 材料融合研究所(yusuke.arai@agc.com)
** 株式会社AGC総研(kazuhiko.yamada@agc.com)
中空シリカ粒子は、材料として取り扱い易く、細孔構造や表面物性の多様性等の優れた特性を有することから、様々な用途に向けた研究・開発が行なわれてきており、近年では環境、医療・バイオ、電子デバイス分野への応用が期待されている。既存の中空シリカ粒子ではコスト、粒径、強度等の観点で課題があることから、本研究ではこれらの課題を解決する新規真球状中空シリカナノ粒子の開発に取り組んだ。ドデカンを液体核として、珪酸ソーダおよびEO-PO-EOブロックコポリマーを用いた2段階のシリカ殻形成工程により前駆体を作製し、これを400℃で煆焼、650℃~800℃で焼成することで、真球形状の中空シリカナノ粒子を得た。粒径は300 nm~700 nmの範囲で、殻厚は17 nm~32 nmの範囲で制御可能であり、この範囲において実用的な強度を実現した。さらに、700℃以上での焼成でシリカ殻が水やアルゴンガスを透過しない程度まで緻密化し、800℃焼成品は、室温下であれば水中に保持しても水が中空内へ浸透せず、光散乱性および分散性を2年程度維持可能であることを示した。比較的安価な原料とプロセスからこれらの優れた特長を有する真球状中空シリカナノ粒子を実現したことで、化粧品用樹脂粒子代替、電子デバイス用の低誘電、断熱用フィラー材料、反射防止塗膜、ドラッグデリバリー等のバイオ・医薬等分野への展開が期待される。
Spherical silica particles are gaining much popularity as they are expected to be used in environmental, biomedical, and electronics applications. However, conventional silica particles were unsuitable for these applications due to their high cost, size, and poor mechanical properties. This report describes novel spherical hollow silica nanoparticles with dense shell structures that can solve the issues listed above. A poly(ethylene oxide)-poly(propylene oxide)-poly(ethylene oxide) block copolymer-based oil-in-water emulsion combined with sodium silicate was developed as a novel synthesis process. Silica shell structure was prepared in two steps shell formation process and then subjected to filtering, calcination, and sintering processes, yielding spherical hollow silica nanoparticles. The primary particle median diameter and shell thickness can be controlled within 300–700 nm and 17–32 nm, respectively. After sintering at 800℃, the products had a dense and robust structure with sufficient mechanical strength for practical use and excellent water impermeability. The remarkable novel spherical hollow silica nanoparticles are expected to be used in various applications, including cosmetics as polymer alternatives, electronic devices as low dielectric and insulation filler material, and biomedicals as drug delivery.
1. 緒言
中空粒子は、低密度、高比表面積、低屈折率、物質内包能等種々の性質を持ち、これらの性質を活かして、軽量材、断熱材、色材等幅広い分野で利用されている。中空粒子には中空樹脂粒子や中空無機粒子があり、中空無機粒子には、チタニア、ジルコニア、酸化錫といった酸化物(1–3)に加え、シリコン、カーボン(4,5)などの様々な研究例があるが、その中でも中空シリカ粒子は、材料として取り扱い易く、細孔構造や表面物性の多様性等の優れた特性を有することから、触媒、触媒担体、化粧品用顔料、樹脂充填剤、吸着剤、乾燥剤、断熱材、塗料、ドラッグデリバリー、反射防止塗膜、超撥水コーティングなど様々な用途を念頭に研究がなされ、また実用化されている(6–11)。AGCにおいても中空シリカ粒子を用いた太陽電池用コート剤を開発し、優れた耐磨耗性と反射防止効果を実現している(12)。さらに近年では、医療・バイオ分野における需要の高まりに加え、マイクロプラスチックによる海洋汚染に対する化粧品分野での懸念の高まりを受けた中空樹脂粒子代替、高周波電子デバイス用途の低誘電率部材向けの応用でも中空シリカ粒子は非常に高い注目を集めている。
中空シリカ粒子の製法は1990年代のメソポーラスシリカ合成に関する研究(13–15)を嚆矢に様々な手法が提案されており、界面活性剤を分子鋳型としてゾルゲル法により作製する手法や、エマルション中の液滴を核とする方法、樹脂や無機粒子といった固体核の周囲にシリカ殻を形成させた後に核を除去する手法が広く用いられている。分子鋳型法による研究例としては、Ranaらによる陽イオン性界面活性剤の臭化ヘキサデシルトリメチルアンモニウム (cetyltrimethylammonium bro-mide; CTAB)とオルト珪酸テトラエチル(tetraethyl orthosilicate; TEOS)を用いて超音波キャビテーション下で粒子形成させる手法(16)、FowlerらによるTEOSとCTABを添加したアルカリ性水溶液を攪拌した水中へ滴下しつつpH調整で反応制御して形成させる手法(17)、Hubertらによる臭化ジメチルジオクタデシルアンモニム(dioctadecyl dimethyl ammonium bromide; DODAB)のベシクル上でTEOSを反応させる手法などが挙げられる(18)。エマルション中の液滴を核とする方法では、TEOSに替えて安価な珪酸ソーダを出発原料とした研究例があり、Jafelicciらは、硝酸水溶液を陰イオン系界面活性剤sodium1,2 bis (2-ethylhexyl-oxy-carbonyl)-1-ethenesulfonateを添加したヘプタン中に加えてW/O型のマイクロエマルションを形成させ、これに珪酸ソーダ水溶液を添加することでエマルションを核とした中空シリカ粒子を形成している(19)。またSunらはpoly(ethylene oxide)-poly(propylene oxide)-poly(ethylene oxide) (EO-PO-EO) ブロックコポリマーを添加した塩酸とトリメチルベンゼンによりO/W型エマルションを形成させ、これに珪酸ソーダ水溶液を添加することでマルチラメラ構造のシリカ殻を有する中空シリカ粒子を形成している(20)。これらの液体核を用いる方法に対し、固体核を用いる手法としてはポリスチレン(PS)粒子を用いる報告例が比較的多い。例えばPS粒子表面にStöber法でシリカ殻を形成させることで単分散の中空シリカナノ粒子を形成させたZhangらによる報告(21)、同様にPS粒子を核としてメソ孔の存在しない緻密な殻を有する中空シリカナノ粒子を形成したNandiyantoらによる報告(22)がある。
さらに近年では、中空シリカ粒子形成に加えて機能性を付与するための表面修飾や中空部へ機能性材料を閉じ込める検討等も行われており、例えばPS粒子を核に中空シリカナノ粒子を形成し、さらに有機物により表面修飾することで機能付与を検討したSharmaらによる報告(23)、中空シリカナノ粒子内に酵素(グルコースオキシダーゼ)を内包させたJoらによる報告(24)などが挙げられる。
このように種々の応用が期待され、多岐に渡る製造方法が研究されている中空シリカ粒子であるが、製品化されているものは高価格かつ小粒径のものと低価格かつ大粒径のものに二極化している。高価格かつ小粒径の製品としてPS粒子を固体核として用いて作製されたものがある。この手法は径の揃った真球状の中空粒子を形成できるという優れた特徴を有しているが、Stöber法による殻形成に時間がかかるため製造コストが高く、100 nm以上の粒径のものを製造しにくい。加えて固体核の除去にもコストがかかるため、価格は1kgあたり数十万円と高価であり、少量で高付加価値が得られる分野のみに利用が限られている。また、粒径が100 nm以下であることから、例えばEUの改正新規食品規則:(EU) 2015/2283や化粧品規則:(EU) No1223/200、殺生物性製品規則 (EU) No 528/2012といったナノマテリアル規制の対象となってしまうため、応用範囲がさらに限定されてしまう。一方で低価格で実用化されているものとしては、純粋なシリカではなくソーダライムボロシリケートガラス系の中空ガラス粒子(例えば3M™社のグラスバブルズ(25))があり、断熱材用途や誘電率低減用途に広く用いられている。これらは噴霧火炎中に発泡剤を含むガラスビーズを投入し、ガラスの溶融と内部からの発泡を同時に進行させることでバルーン状粒子を形成しているため、粒径が10 µm以上で粒度分布も広くなりやすく、微細な電子デバイスや化粧品、バイオ・医薬等の用途には適さない。このため、近年注目を集めつつあるこれらの応用分野に適用可能なサブミクロンサイズの中空シリカ粒子は市場に存在しておらず、実用化に向けて工業的に比較的安価に生産可能な手法の実現が望まれている。
そこで本研究では、従来の方法では実現できていなかった粒径100 nm~1µmの範囲で、粒径、殻厚、比重を制御可能な中空シリカナノ粒子の製造手法確立に取り組んだ。固体核とシリコンアルコキシドを用いる手法ではコスト面と粒径の課題が解決できないと判断し、本研究では液体核と珪酸ソーダを用いる手法を採用した。JafelicciらやSunらによる過去の検討(19,20)では中空シリカ粒子の合成は実現できているものの、粒径、殻厚の制御や実用上十分な機械的強度は実現できておらず、メソポーラスな殻構造であるために、例えば水中で保持した際に長期間中空性を維持しにくい。本論文では上記課題の解決を実現する新規な中空シリカナノ粒子形成手法を提案し、シリカ殻形成工程におけるpH制御および珪酸ソーダの比率、焼成工程における温度条件が殻構造に与える影響について考察を加える。また、水中で長期間保持した際の中空内への水侵入モデルを提案し、作製した粒子の水中で保持した際の長期信頼性について考察する。
2. 実験方法
2.1. 中空シリカナノ粒子の作製
中空シリカナノ粒子は、O/Wエマルション中の液滴を液体核として2段階のシリカ殻形成工程を経て前駆体分散液を調製し、それをろ過、乾燥、焼成することで作製した。以下各工程について詳述する:
エマルションの作製:純水965.5 gにEO-PO-EO型ブロックコポリマー(EO80-PO30-EO80, ADEKA社製プルロニックF68)をn-ドデカンの重量の0.15倍である4.5 g添加し溶解するまで攪拌した。この水溶液にn-ドデカン30 gを加えた後にシャフトジェネレータ(IKA社製 T50 digital ULTRA TURRAX)により予備乳化を行い、その後高圧乳化機(エスエムテー社製LAB2000)を使って圧力40 MPaで3回乳化作業をすることで微細エマルションを得た。エマルションは作製後12時間25 ℃で静置したものを以降の試験に供した。また、一部サンプルについてはエマルション静置時間および温度を変化させエマルション径を変化させたものを用いた。
1段目シリカ殻形成:得られた微細エマルションへ、SiO2 10wt%相当に希釈した三号珪酸ソーダ(Na2O・3.2SiO2・22.8H2O)水溶液(以降、希釈珪酸ソーダ水溶液と表記する)をpHが2となるよう2M 塩酸とともにゆっくり加え、25 ℃で保持しながら良く攪拌した。加える希釈珪酸ソーダ水溶液の量はドデカン量に対するSiO2量の重量比(以降S/Oと表記する)が0.1となるよう30 gとした。その後1M 水酸化ナトリウム水溶液をゆっくり 滴下してpHが6となるよう調製し、オイルコア-シリカシェル粒子分散液を得た。シリカ殻形成段階でのpHの影響を調査する目的で、一部サンプルについては希釈珪酸ソーダ水溶液添加中および添加後のpHを意図的に変化させたものもあわせて作製した。
2段目シリカ殻形成:1段目シェル形成で得られたオイルコア-シリカシェル粒子分散液を70 ℃に加熱し、攪拌しながら1M 水酸化ナトリウム水溶液をゆっくり添加し、pHを9とした。続けて希釈珪酸ソーダ水溶液を、pH が9前後で維持されるように0.5 M塩酸とともに徐々に添加し、その後70 ℃で2日間保持した後、ゆっくり室温まで冷却し、中空シリカ前駆体分散液を得た。添加した希釈珪酸ソーダ水溶液の量は、1段目シリカ殻形成で添加したSiO2量との合量でS/O=0.4, 0.8, 1.2, 1.6, 1.8, 2.2となるようにした。
ろ過、煆焼、焼成:中空シリカ前駆体分散液を0.45 µmの親水性ポリテトラフルオロエチレン(PTFE)製メンブレンフィルターを用いて加圧ろ過を行った(圧力0.28 MPa)。ろ過後のケーキを窒素雰囲気下60 ℃で1時間、400 ℃で4時間煆焼し(昇温速度5 ℃/min)、有機分を除去することで中空シリカ前駆体を得た。この前駆体を550~800 ℃で4時間焼成(昇温速度5 ℃/min)することで中空シリカナノ粒子を得た。
2.2. 評価
微細エマルション中のドデカン液滴径分布は動的光散乱式粒度分布計(マイクロトラック・ベル社製 Nanotrac)を用いて測定した。
1段目および2段目シリカ殻形成時点での粒子形状は透過型電子顕微鏡(TEM)(日立ハイテクノロジーズ社製 HT7700)を用いて加速電圧100 kVで観察した。観察前処理として、親水化処理したコロジオン膜上に、固形分濃度が0.1 wt%程度になるようにイオン交換水で希釈した試料を滴下・乾燥させた乾燥試料、および液中観察ツールキット(Bio Ma-tek社製K-kit)内へ試料を封入した液中試料の2種類を準備しTEM観察に供した。また、中空シリカナノ粒子の殻厚を測定するため、800 ℃焼成後の中空シリカナノ粒子についてもTEM観察を行った。焼成後の中空シリカナノ粒子は走査型電子顕微鏡(SEM)(日立ハイテクノロジーズ社製 S4800)を用いて加速電圧3 kVでの観察も行い、粒径分布、形状、二次凝集状態の評価を実施した。中空シリカナノ粒子の二次凝集径は回折散乱式粒子分布測定装置(マイクロトラック・ベル社製 MT3300)を用いて測定した。
煆焼~焼成過程における重量変化は熱重量示差熱分析(TG-DTA) (TAインスツルメンツ社製 Q600)を用いて評価した。ろ過後のケーキを60 ℃の乾燥機中で一晩乾燥させたものを試料とし、乾燥空気雰囲気下で室温~800 ℃の範囲(昇温速度5 ℃/min)で測定を行った。
得られた中空シリカナノ粒子のシリカ殻の状態は、比表面積測定、細孔径分布測定、乾式密度測定および水中での見かけ密度測定により評価した。比表面積はマウンテック社製 Macsorbを用い混合ガス(吸着ガスとして窒素30%、キャリアガスとしてヘリウム70%)を用いてBET1点法により求めた。細孔径分布はMicromeritics社製 3Flexを用い、窒素吸着法により求めた。乾式密度測定はヘリウムガス、酸素ガス、およびアルゴンガスをプローブガスとして乾式ピクノメーター(Micromeritics社製 AccuPyc II 1340)を用いて測定した。水中での見かけ密度は、ゲーリュサック型比重瓶を用いて測定した。前処理として比重瓶中に試料と水を入れ、比重瓶ごとPTFE製の密閉容器に入れて110 ℃の恒温槽中で16時間静置、その後室温まで冷却してから測定を実施した。また、中空シリカナノ粒子内への水の浸透挙動を評価するため、上記恒温槽の温度を40、70、110 ℃として1~30日間での密度の経時変化もあわせて評価した。
中空シリカナノ粒子の強度は静水圧加圧前後での中空粒子率(完全に被覆されている中空シリカナノ粒子の体積割合)を比較し、粒子が10%破損する圧力をもって指標とした。静水圧加圧は、中空シリカナノ粒子をシーラー用袋へ入れシーリング後、CIP装置(エヌピーエーシステム社製 CPA-50)を用いて1分間実施した。
3. 結果
3.1. 微細エマルション中のドデカン液滴径分布および中空シリカナノ粒子の粒径分布
Fig. 1にS/O=1.2の作製に供した微細エマルション中のドデカン液滴分布測定結果と、SEM画像より算出した800 ℃焼成後中空シリカナノ粒子 (S/O=1.2)の粒径分布をあわせて示す。ドデカン液滴および中空シリカナノ粒子のメディアン径(D50) はそれぞれ265 nm、300 nmであり、両者の分布は良く一致していることを確認した。
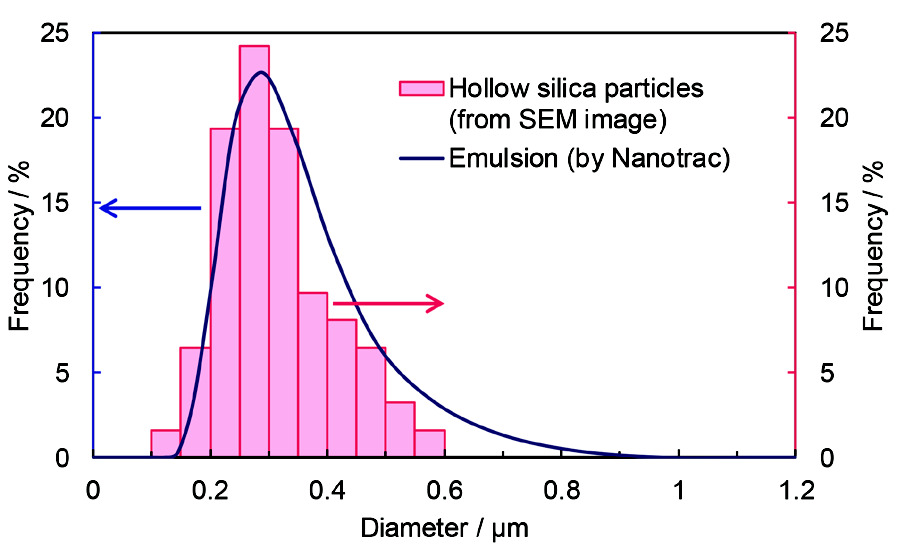
エマルション静置条件を変化させて作製した中空シリカナノ粒子(S/O=1.2)における800 ℃焼成後のメディアン径と静置時間の関係をFig. 2に示す。保持温度が25 ℃でも静置時間を長くすることで、一次粒子径が大きくなり、約200時間後には粒径600 nmとなることがわかった。また、保持時間を70 ℃にすると、15時間静置でも一次粒子径が700 nmを越える中空シリカナノ粒子を作製可能であることがわかった。
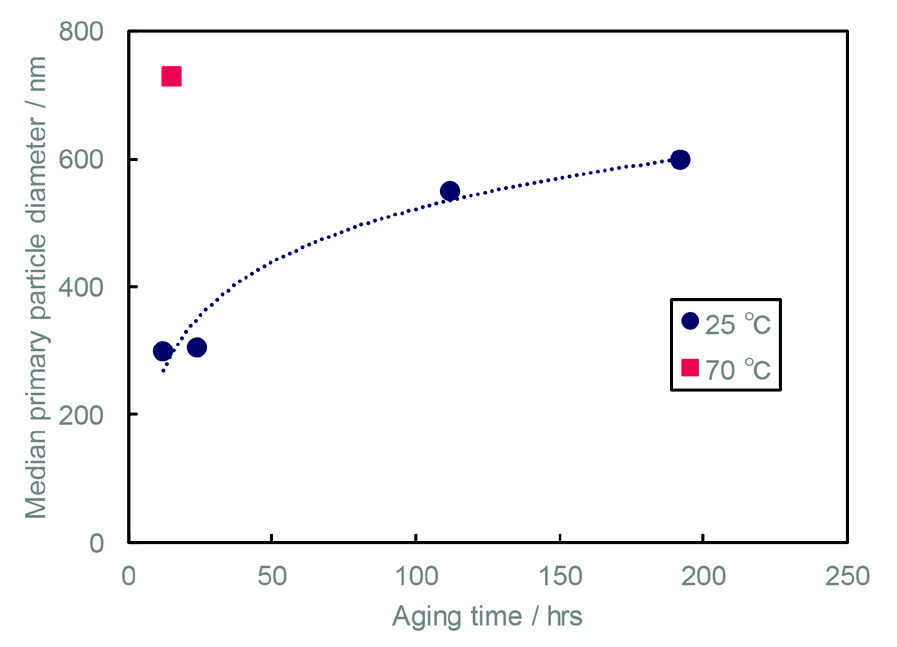
3.2. シリカ殻形成過程および煆焼前中空シリカ前駆体のTEM観察結果
1段目シリカ殻形成時点でのオイルコア-シリカシェル粒子のTEM観察結果をFig. 3に、2段目シリカ殻形成終了時点での中空シリカ前駆体(S/O=1.2)のTEM観察結果をFig. 4にそれぞれ示す。Fig. 3, 4ともに乾燥試料の観察結果である。Fig. 3から、1段目シリカ殻形成時点では球形ではなくホオズキ形の中空粒子が存在し、このホオズキ形中空粒子の殻厚が5 nm以下程度であること、また数10 nmφ程度の微粒子が多数存在していることを確認した。その後2段目シリカ殻形成工程を経ると、Fig. 4からわかるようにホオズキ形中空粒子や数10nmφの微粒子は見られなくなり、全て真球形状の中空粒子となることを確認した。また、中空粒子の一部は完全な中空ではなく開口部が存在している(以降、不完全中空粒子と表記する)ことを確認した。
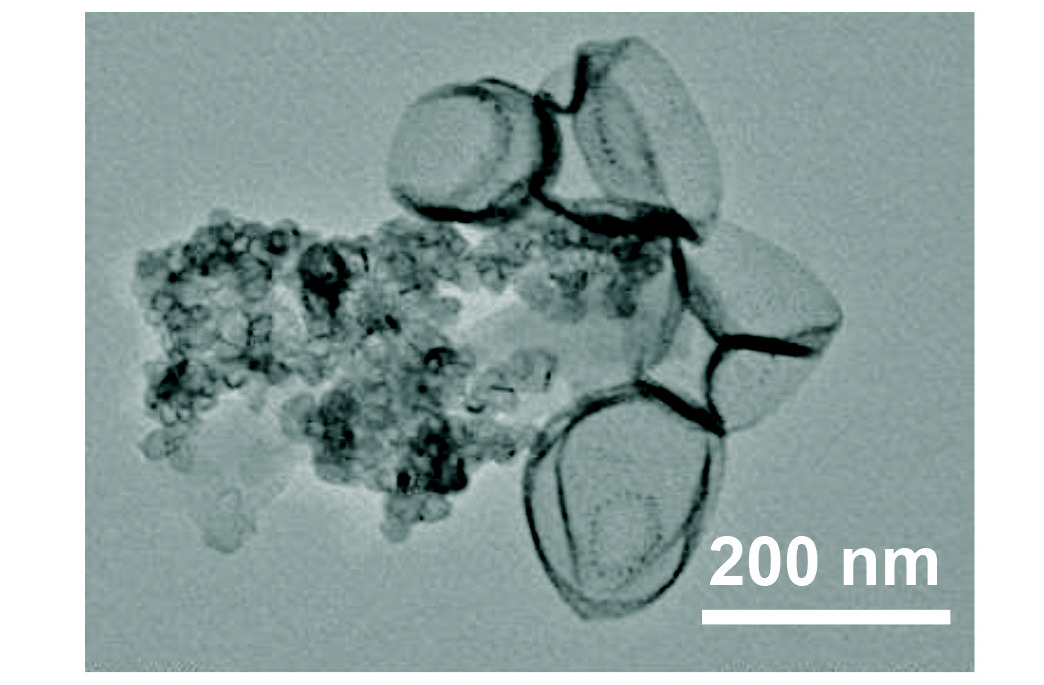
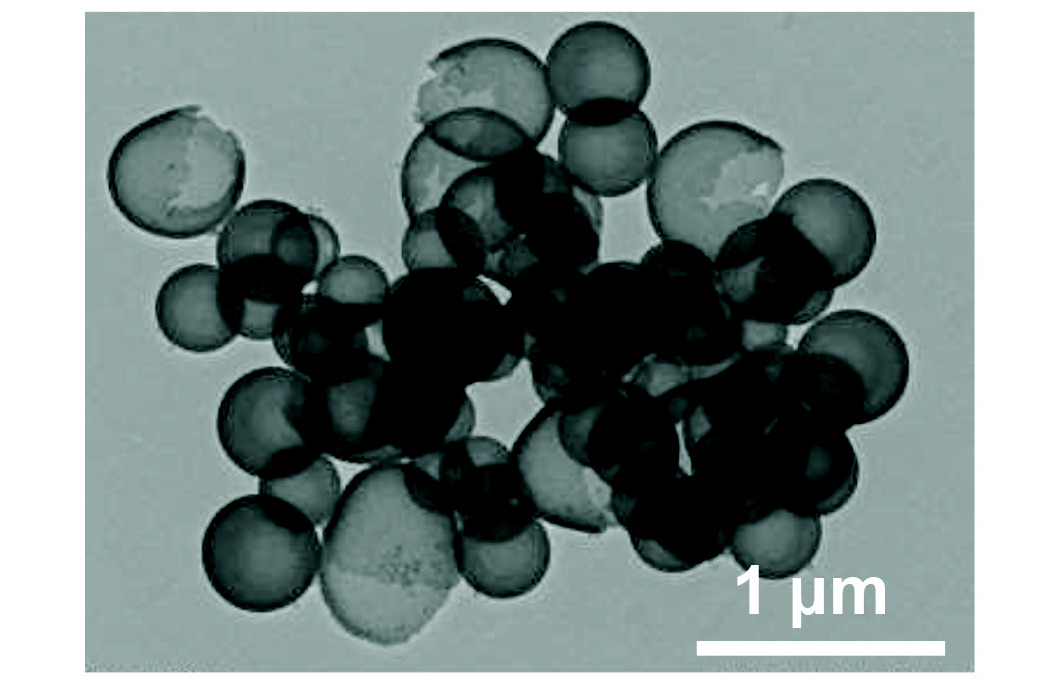
Fig. 5に液中試料のTEM観察結果を示す。Fig. 5 (a)が1段目シリカ殻形成時(Fig. 3に対応)、Fig. 5 (b)が2段目シリカ殻形成の初期段階、Fig. 5 (c)が2段目シリカ殻形成終了時点(Fig. 4に対応)である。なお、液中試料は観察キットの開口幅が500 nmであるため、500 nm以上のサイズの粒子は観察できないこと、また、真空に比べてコントラストがつきにくいため、微細な構造や数10nm程度の微粒子が見えにくい点に留意する必要がある。Fig. 5から、液中では1段目シリカ殻形成時でも(若干いびつではあるが)球形をしていること、2段目シリカ殻形成初期段階では不完全中空粒子が多く見られ、100nm未満の微粒子が見られること、2段目シリカ殻形成終了時点の液中でも不完全中空粒子が存在することを確認した。
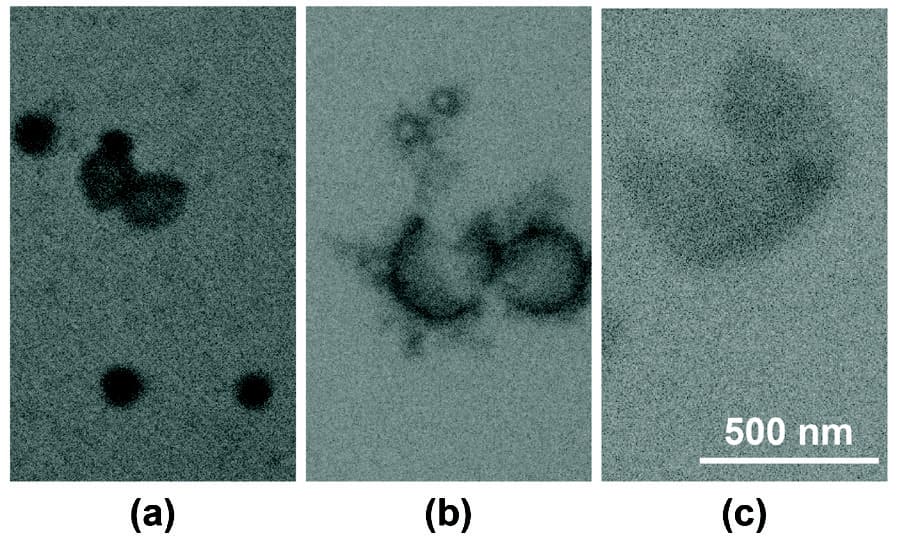
3.3. TG-DTA測定結果
Fig. 6にS/O=1.2の条件で作製した中空シリカ前駆体におけるTG-DTA測定結果を示す。200 ℃から500 ℃の間で、380 ℃付近の大きな発熱ピークを中心とした発熱ピークが複数見られ、それに伴い約40%の重量減少が生じていることがわかった。200 ℃以下における約3%弱の重量減少は60 ℃風乾後に残留していた吸着水によるものと推定され、200 ℃~500 ℃にかけての重量減少はシリカ殻からEO-PO-EOブロックコポリマー F68、中空内部からドデカンが燃焼・脱離することによるものと考えられる。500 ℃以上では重量減少が見られないことから、500 ℃の熱処理で前駆体中の有機成分は完全に除去されて、中空シリカナノ粒子を形成していると考えられる。
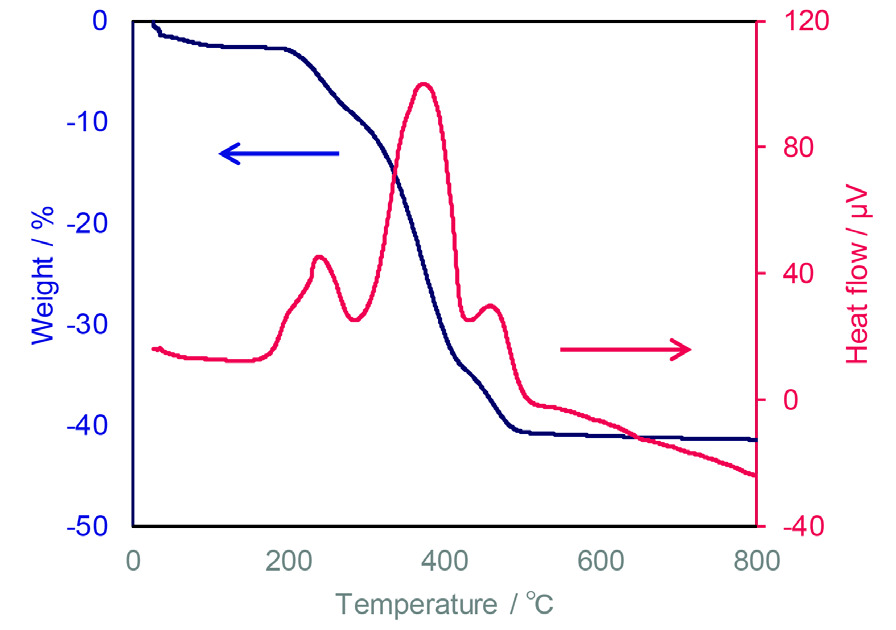
3.4. 1段目シリカ殻形成時のpHを変化させた中空シリカナノ粒子作製結果
1段目シリカ殻形成において、希釈珪酸ソーダ水溶液を添加中および添加後のpHを変化させて作製した中空シリカナノ粒子のSEM観察結果をFig. 7に示す。図中、添加中のpH(pHinit)を縦軸に、添加後のpH(pHpost)を横軸にしてSEM像を整理した。pHinit=2、pHpost=6の条件から外れると、中空粒子表面にシリカ微粒子が多数生じてしまうこと、また、不完全中空粒子の割合が多くなることを確認した。Table 1にこれらの粒子のBET比表面積、見かけ密度、中空粒子率および微粒子析出量を示す。中空粒子率はTGDTA測定結果より4.1節に示した方法で算出した。微粒子析出が多い条件ではBET比表面積も大きいこと、pHinit=2、pHpost=6以外の条件では見かけ密度が大きく、中空粒子率が低いことがわかった。
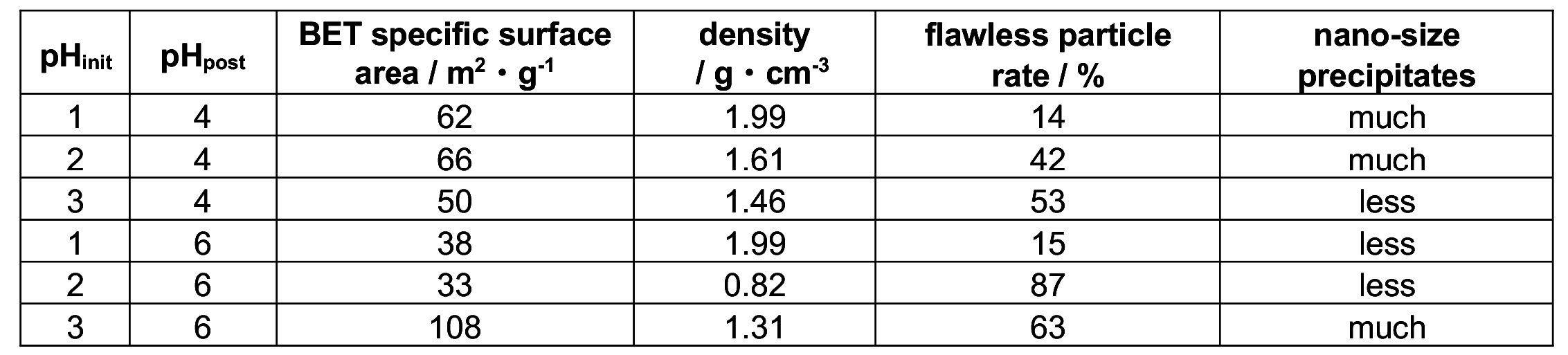
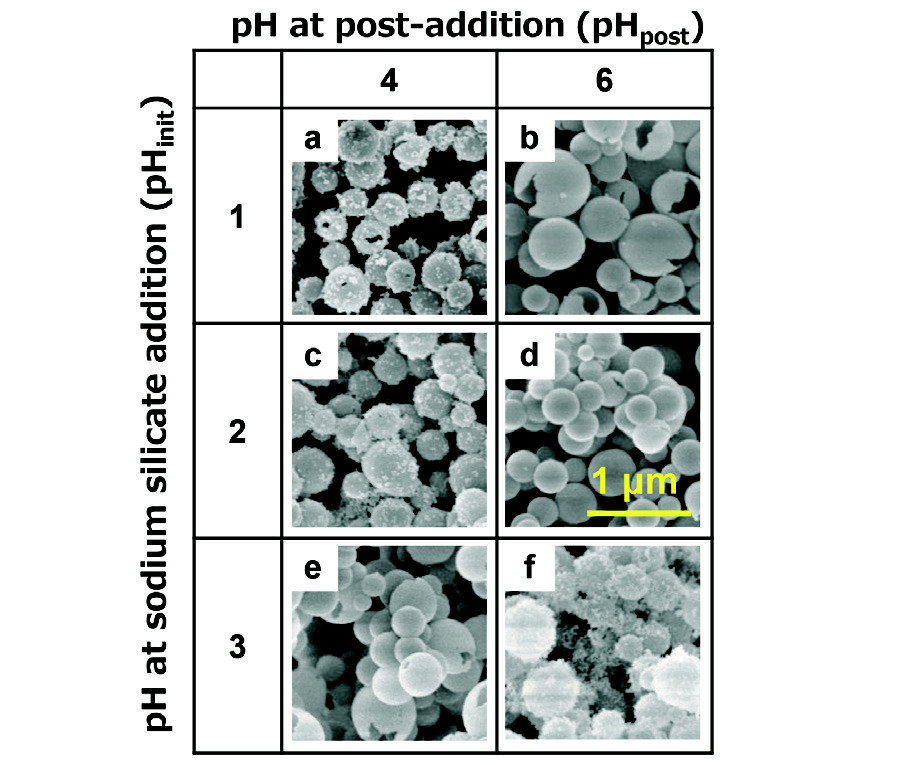
3.5. 焼成温度の異なる中空シリカナノ粒子の細孔径分布、比表面積および密度測定結果
Fig. 8にS/O=1.2の中空シリカナノ粒子における、焼成温度に対するBET比表面積および水中での見かけ密度の変化を示す。焼成温度が高くなるにつれて、比表面積は直線的に減少し、見かけ密度は、650 ℃以下ではアモルファスシリカの真密度に近い2.0~2.1程度であるのに対して650 ℃から700 ℃の間で急激に小さくなり、700 ℃以上では1.0前後となることが確認できた。
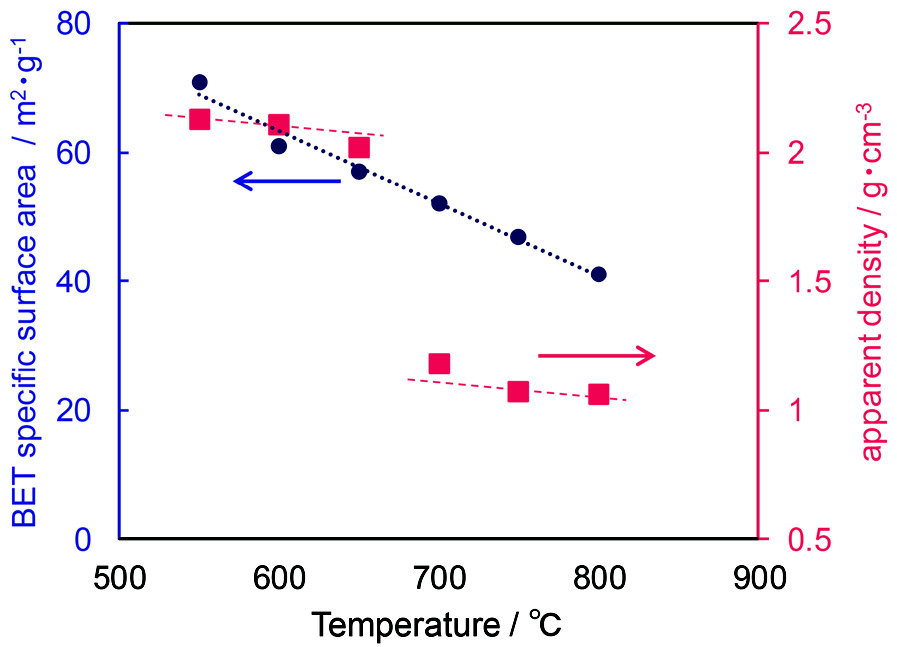
乾式密度測定結果をFig. 9に示す。ヘリウムガスをプローブとした場合の密度は焼成温度によらずアモルファスシリカの真密度とほぼ同等の2.2であるのに対し、酸素ガスでは650 ℃以下の温度では極端に高い値や測定エラーとなり有意な値が得られず、700 ℃以上ではFig. 8に示した水中での見かけ密度とほぼ一致する値となることを確認した。同様にしてアルゴンガスをプローブとして測定した結果は、650 ℃以下の温度ではヘリウムガスプローブとほぼ同等で700 ℃以上では酸素ガスプローブの場合とほぼ等しい値となることがわかった。また、これらのサンプルに対して窒素吸着法により細孔径分布測定を実施した結果、650 ℃以下では4 nm に細孔径のピークが確認できたが、700 ℃以上ではピークが確認できなかった。
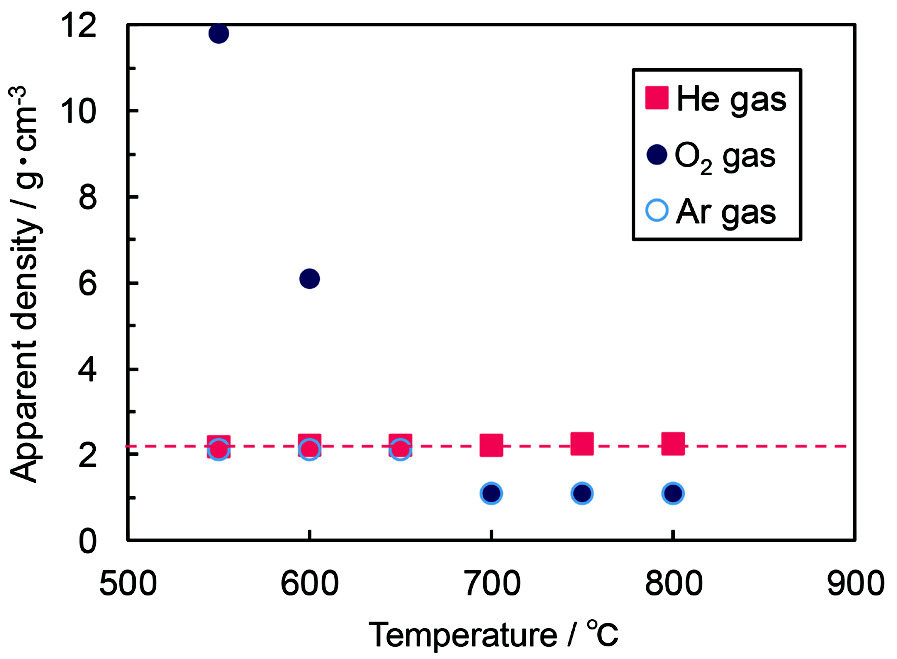
3.6. S/Oの異なる中空シリカナノ粒子の作製結果
800 ℃焼成後中空シリカナノ粒子(S/O=1.2, 2.2)のTEM観察結果をFig. 10(a),(b)に示す。シリカ殻の厚さがS/O=1.2では22 nm、S/O=2.2では37 nm前後であること、800 ℃焼成後も綺麗な球形の中空構造を維持していることを確認した。
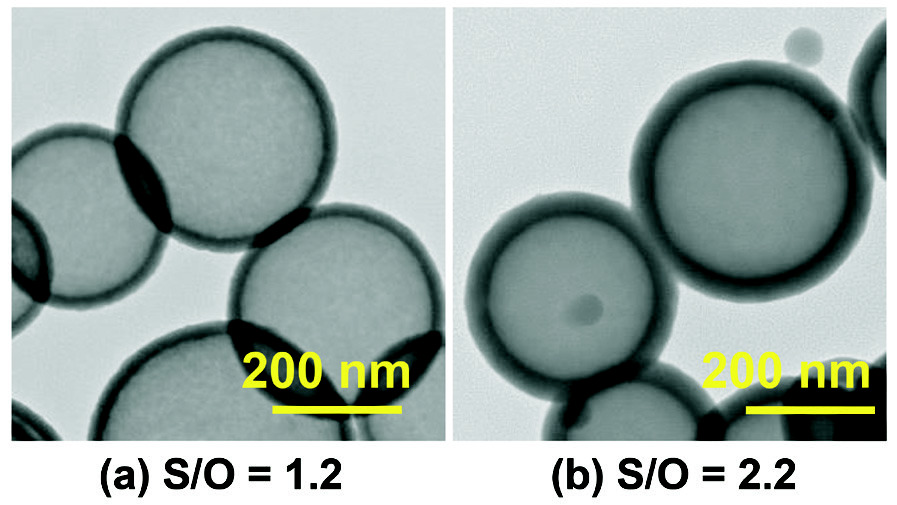
800 ℃焼成後中空シリカナノ粒子(S/O=0.4, 0.8, 1.2, 1.6, 1.8, 2.2)のSEM観察結果をFig. 11に示す。今回作製したS/Oの範囲ではいずれも球状の粒子を形成できることが確認できた。S/O=0.4では球状を維持できている粒子が少なく、球状でも不完全中空粒子が数多くみられた。S/O=1.8以上では、S/O=1.6以下の試料と比べて微粒子状の付着物が多くみられた。なおSEM観察とあわせて実施したEDX分析結果から付着物はシリカ微粒子であることを確認している。
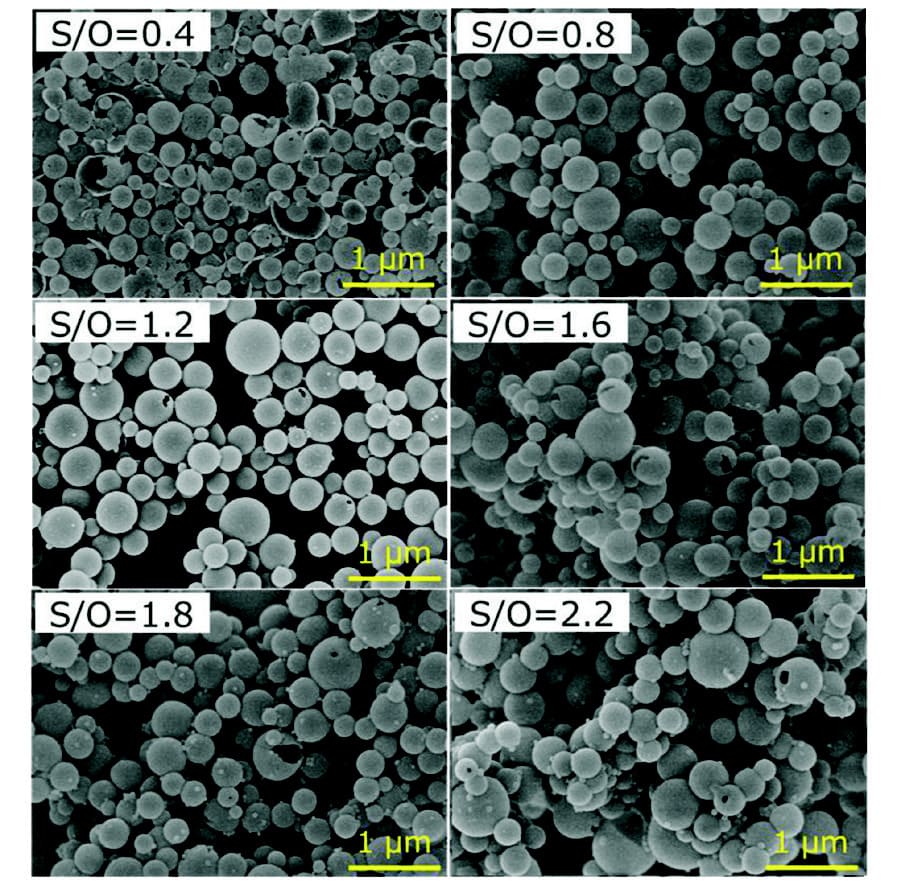
不完全中空粒子の開口部に着目し各S/Oにおけるシリカ殻の厚さを測定した結果とTEM観察から測定した結果をあわせてFig. 12に示す。両者の結果は良く一致しており、S/Oが大きくなるとシリカ殻が厚くなること、開口部の殻厚が特異的に厚かったり薄かったりするわけではないことが確認された。Table 2に800 ℃焼成後中空シリカナノ粒子(S/O=0.8, 1.2, 1.6, 1.8, 2.2)の殻厚、一次粒子径、凝集径、BET比表面積、見かけ密度および中空粒子率の測定結果を示す。中空粒子率はTG-DTA測定結果より4.1節に示す方法で算出した。S/Oによって殻厚とBET比表面積は変化するのに対し、他物性は明確な相関が見られなかった。
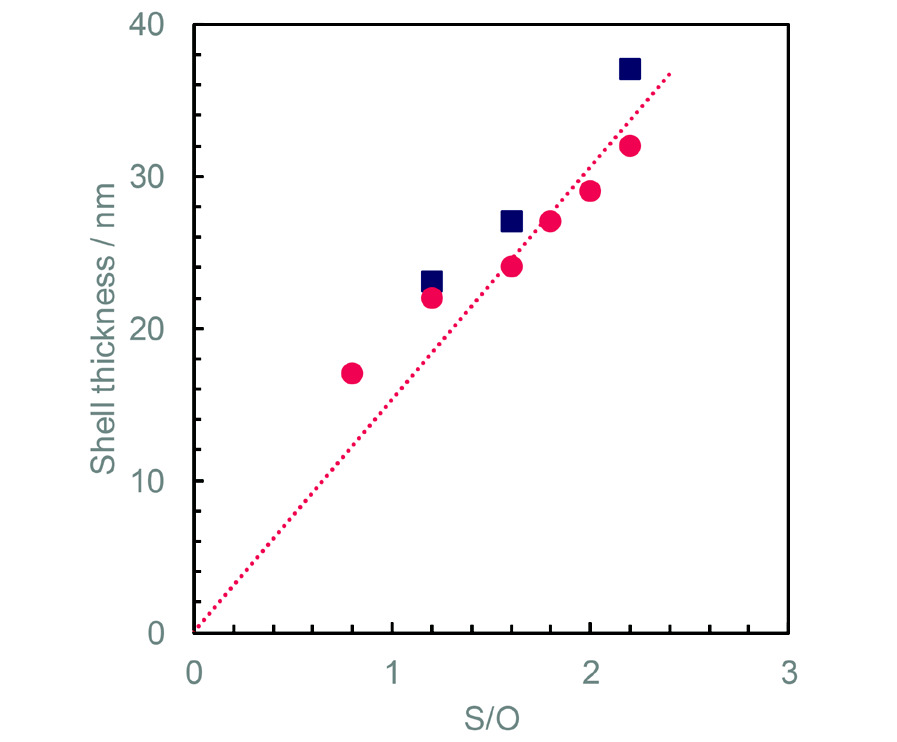
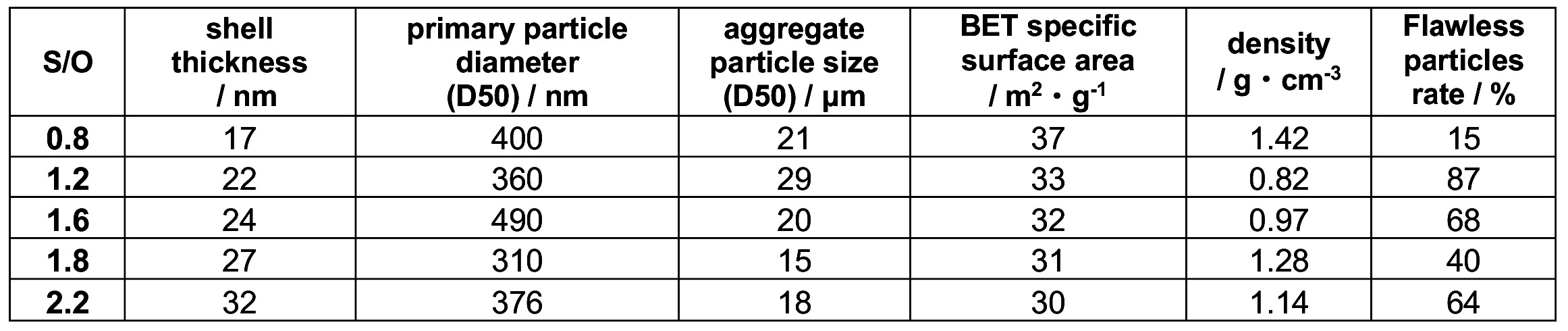
Fig. 13にS/Oに対する静水圧加圧による10%破壊応力の変化を示す。S/O=1.2において10%破壊応力が6 MPaと、樹脂等への混練工程でも破壊しない実用的な強度を持つこと、また、今回作製した範囲では、S/Oに対して直線的に増加することがわかった。800 ℃焼成後中空シリカナノ粒子 (S/O=1.2)を樹脂中へ均一になるよう混合した後の断面SEM観察結果をFig. 14に示す。樹脂との機械的混合後においても真球形状を維持していることが確認できた。
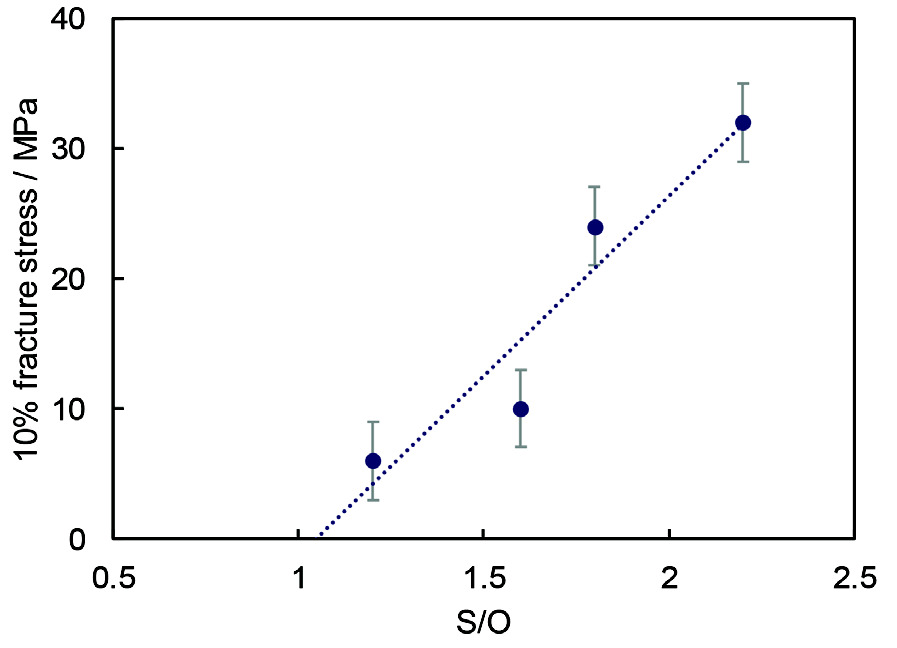
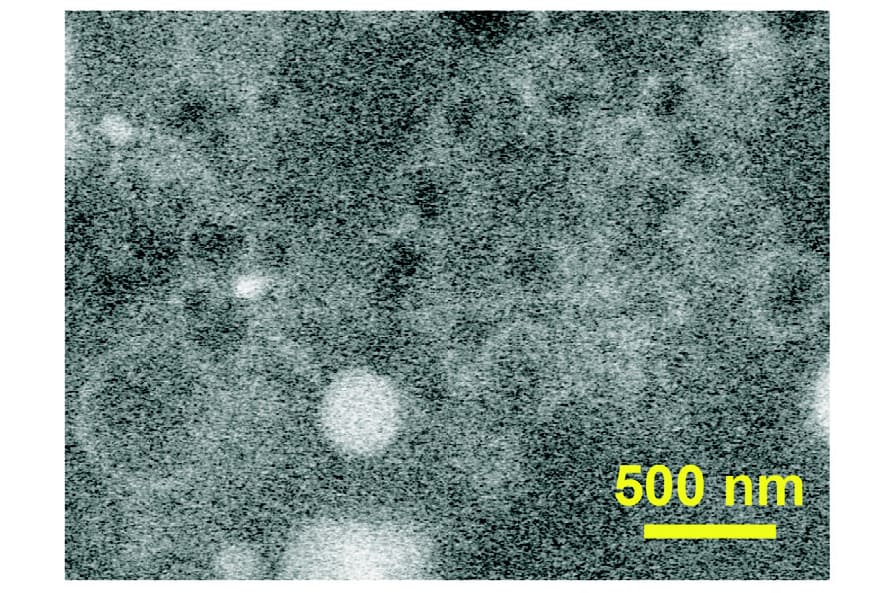
3.7. 水浸漬による中空シリカナノ粒子の見かけ密度の経時変化評価結果
700 ℃焼成後の中空シリカナノ粒子(S/O=1.2)を40、70、110 ℃の恒温槽中で水へ浸漬し、見かけ密度の経時変化を測定した結果をFig. 15に示す。水温が高くなるに従い見かけ密度の増加が早くなり、40 ℃における密度増加と比べて110 ℃では18倍程度の速度で密度が増加(≒中空部へ水が侵入)することが確認できた。
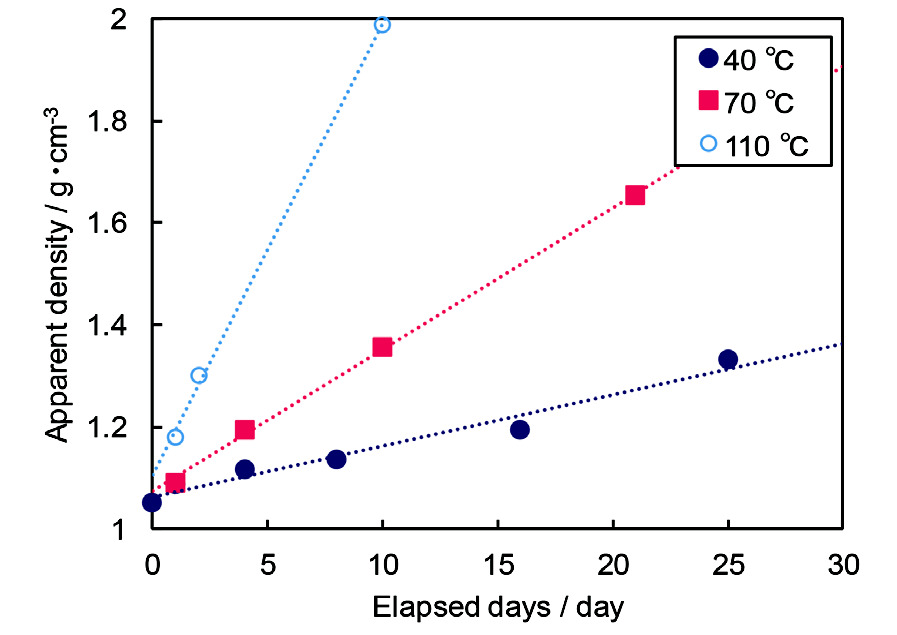
焼成温度の異なる中空シリカナノ粒子 (S/O=1.2)を110 ℃の恒温槽中で水へ浸漬し、見かけ密度の経時変化を測定した結果をFig. 16に示す。焼成温度が650 ℃のサンプルは浸漬直後から水が中空部へすぐに浸透してしまい、アモルファスシリカの真密度とほぼ同等の見かけ密度になってしまうことがわかった。焼成温度が高くなるに従い見かけ密度の増加は遅くなり、800 ℃焼成品では50日浸漬後でも700 ℃焼成品と同等程度の見かけ密度を維持できることがわかった。
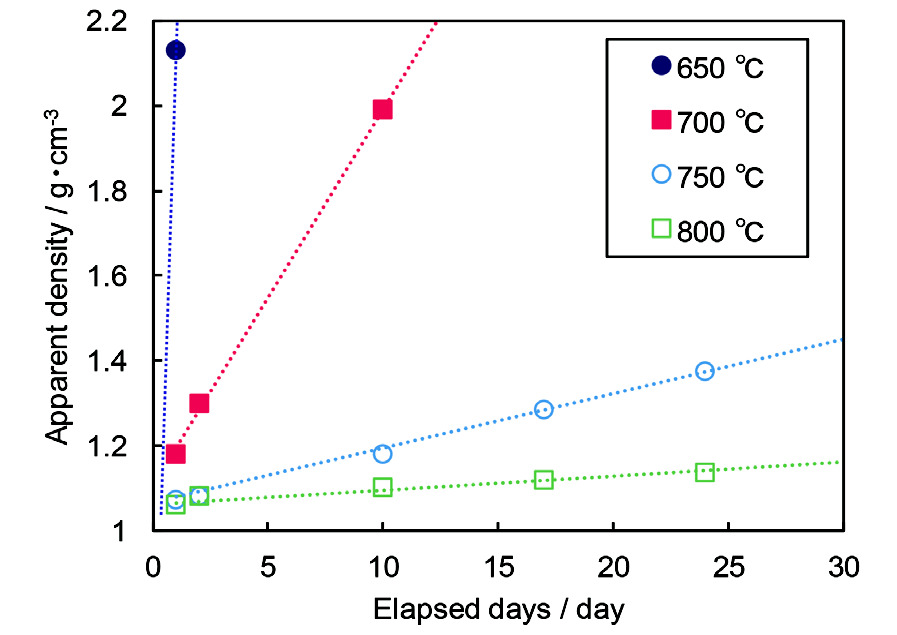
S/Oの異なる条件で作製した中空シリカナノ粒子(700 ℃焼成品) を70 ℃の恒温槽中で水へ浸漬し、見かけ密度の経時変化を測定した結果をFig. 17に示す。S/Oが大きいほど見かけ密度の増加を低下させることを確認できた。
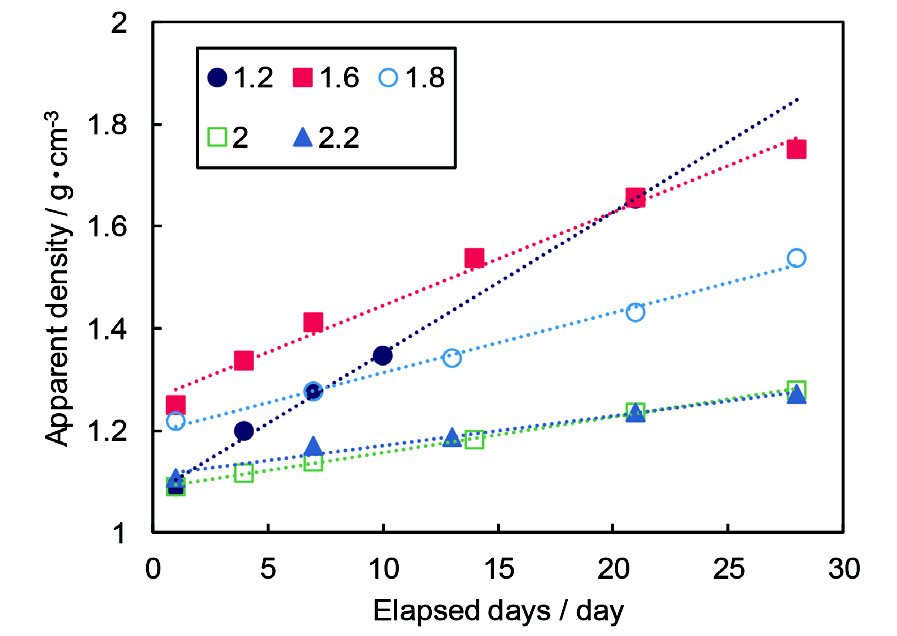
4. 考察
4.1. TG-DTAおよびアルゴンガスプローブの乾式密度測定結果による中空粒子率の推定
SEM観察結果から、作製した中空シリカナノ粒子には完全に被覆されていない不完全中空粒子が存在していることがわかった。本節では、すべての粒子が完全に被覆されているとした時の中空シリカナノ粒子の総体積のうち、実際に完全に被覆されている中空シリカナノ粒子の体積の割合を中空粒子率p[%]と定義し、TGおよびアルゴンガスをプローブとした際の乾式密度測定結果からそれぞれ算出し妥当性を検証する。なお、以下の計算は収率を100 %と仮定し、添加したドデカンの全量が液滴核に、F68の全量がシリカ殻中に存在していると仮定して行った。
TGからの算出は以下のように考えた。3.3節に示したように、200 ℃~500 ℃にかけて見られる重量減少はシリカ殻中に存在するF68と中空内部に残存しているドデカンの燃焼・脱離により生じると考えられる。ここで、不完全中空粒子に関しては洗浄~ろ過~風乾の工程でドデカンが完全に脱離していると考えられるため200 ℃~500 ℃にかけてドデカンに起因する重量減少は生じないはずである。よって、200 ℃~500 ℃の間での重量減少量ΔWはドデカン、F68の仕込み量(それぞれWoil, W68)とpから、以下のように表わせる。

ここでS/O=r とおくと、Woil, W68はシリカの仕込み量Wsilicaを用いてそれぞれWoil=Wsilica/r,W68=0.15Woil=Wsilica/rと表わすことができる。なお、この時のWsilicaはTG測定終了時点でのサンプル重量と等しい。以上の関係を式(1)に代入すると、pは以下の式(2)より求められる。
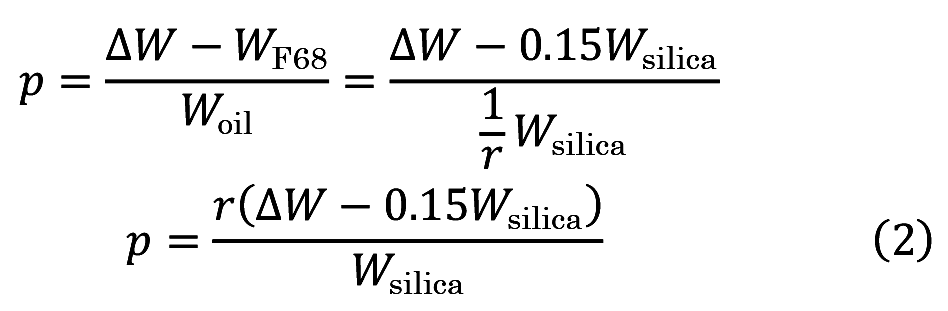
次に、アルゴンガスをプローブとした際の乾式密度測定結果からの算出は以下のように考えた。焼成後の中空シリカ粒子において、ドデカンがあった部分が焼成によって中空シリカの空気層になっていると考えられるため、シリカの体積をWsilica、ドデカンの体積をWoilとすると、中空シリカナノ粒子の体積はp(Wsilica+Woil)で表わされる。また、中空を維持できてないシリカナノ粒子の体積は、(1-p)Wsilicaと表わせる。そのため、シリカの重量をWsilicaとすると、見かけ密度dとpの間に以下の関係が成り立つ。
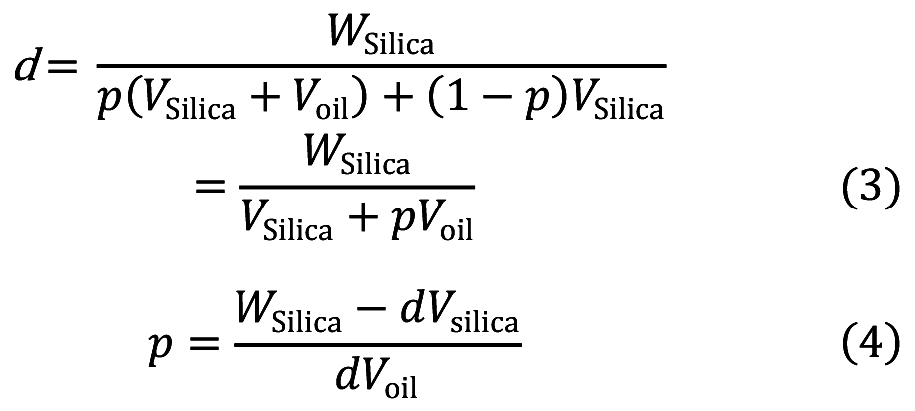
式(2)から算出された中空粒子率を横軸に、式(4)から算出された中空粒子率を縦軸にとったプロットをFig. 18に示す。■は一段目シリカ形成時のpH条件が最適なもの(pHinit=2, pHpost=6)であり、○はそれ以外の条件による結果である。pHinit=2, pHpost=6で作製した試料における中空粒子率は、それぞれの方法で算出した結果の間に良い相関が見られた。一方それ以外の条件では、TGからの算出結果にくらべて乾式密度測定結果からの算出結果が低い傾向が見られた。これは、これらの条件では明確な開口部は無いものの緻密性が悪い中空粒子が存在したことで、TGでは風乾~200 ℃以下ではドデカンが脱離しないために高めの中空粒子率となったことによるものと推定される。明確な開口部の存在の有無を判断するのであればTGによる算出結果を、殻の緻密性も考慮に入れる場合は乾式密度測定結果による算出の方が好ましいと言える。
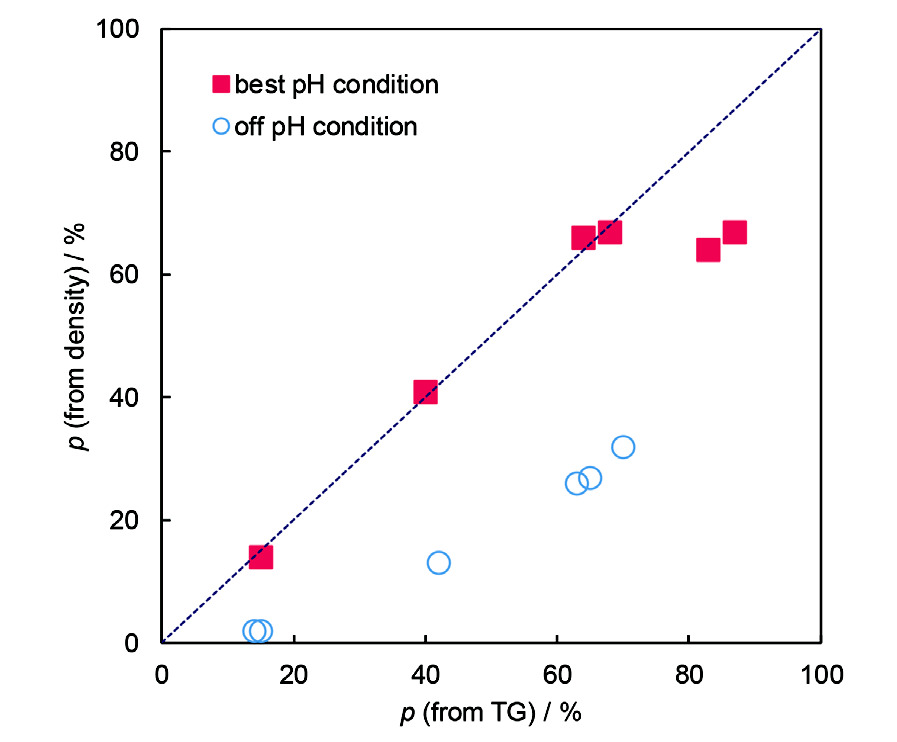
4.2. 1段目シリカ殻形成時のpHがシリカ殻形成機構に与える影響
本研究ではSunらの手法(20)をもとに、実用上十分な機械的強度を有するシリカ殻構造を実現するべく、液中でシリカ微粒子が殻を形成しやすいpH環境を形成する目的で反応を2段階に分けることとした。1段目はエマルション中の油滴界面をシリカナノ微粒子で被覆する工程であり、2段目は被覆したシリカ殻を成長させて厚くする工程である。1段目ではシリカナノ微粒子のネットワーク形成を促進させる必要がある。酸性環境下におけるシリカナノ微粒子は個々の粒子が成長するかわりに三次元的にネットワークを形成することが知られており(26)、そのため本研究では1段目シリカ形成中はpHを酸性側で制御している。3.4節では希釈珪酸ソーダ水溶液添加中および添加後のpHを変化させた際の粒子形状と物性変化について示した。本節ではこの違いが生じた原因について考察する。
Fig. 19に1段目シリカ形成の模式図を示す。SiO2が油滴の周囲に集合して被覆を形成するためには、まず始めに珪酸ソーダから生成するオリゴマー状のシリカナノ微粒子がF68と複合体を形成し、その後複合体が油滴界面上に配列することでシリカ殻を形成すると考えられる。複合体を形成せずにシリカナノ微粒子のみで凝集を開始してしまうと、100 nm以下の微粒子という望ましくない副生成物を形成する原因となる。そのため、1段目シリカ形成の初期段階ではシリカ微粒子がF68と複合体を形成しやすい条件にする必要がある。
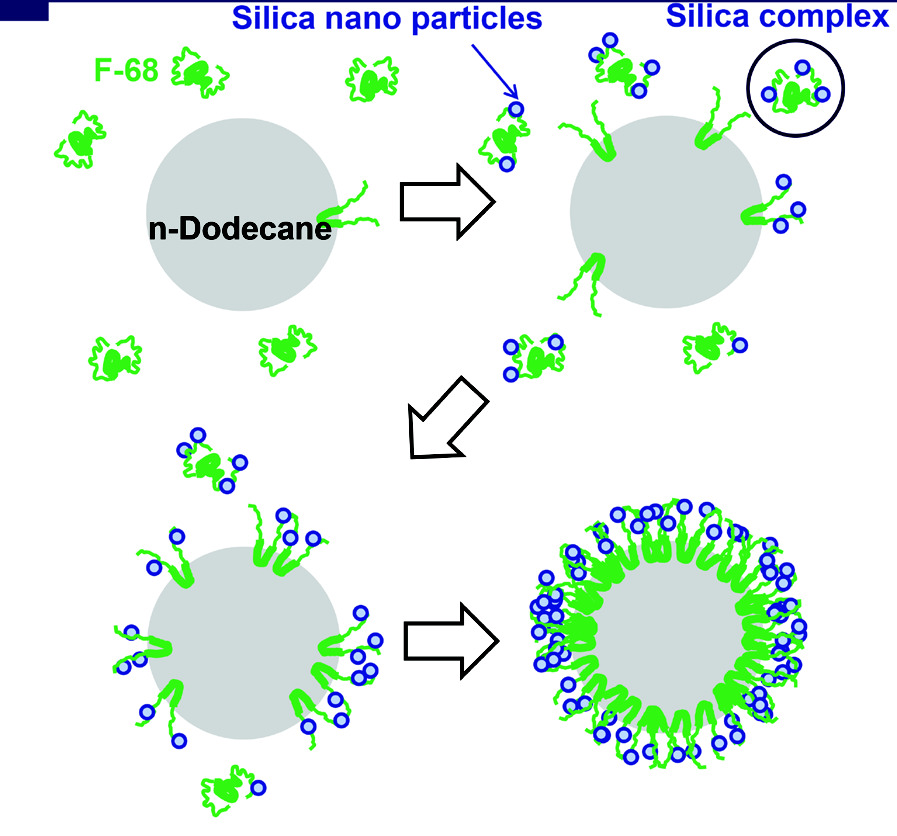
一般的にシリカナノ微粒子はpHによってゼータ電位の変化を示すことが知られており、プラスに帯電した状態のシリカナノ微粒子が、F68で部分的にマイナスに帯電したEO鎖部の酸素分子と静電相互作用で吸着することで前述の複合体を形成すると推定している(Fig. 20)。実際にFig. 3中に見られる数10 nmサイズの微粒子はこの複合体であると考えられる。シリカナノ微粒子のゼータ電位はpHが2以下でゼータ電位がプラスになる領域があり(27)、この条件で保持することでシリカナノ微粒子をF68に吸着させやすくできると考えた。
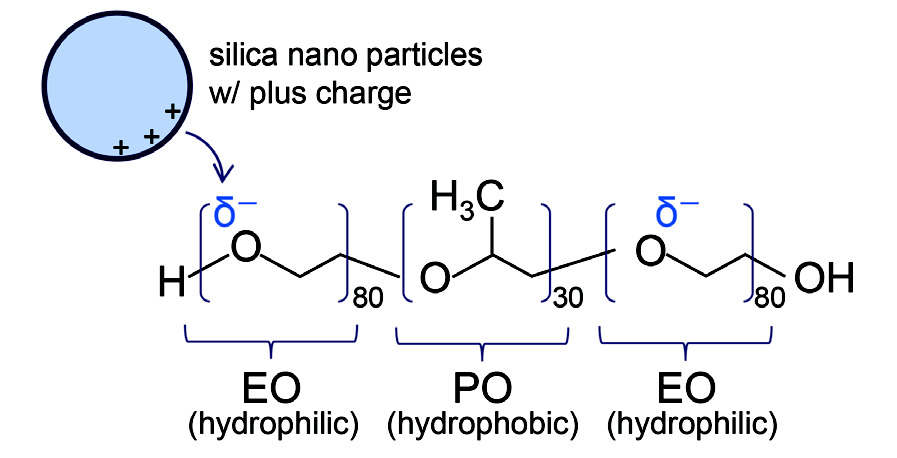
シリカナノ微粒子はF68と複合体を形成後、その状態でF68の疎水性であるPO鎖部が油滴表面に吸着して安定化する必要がある。加えて、油滴周囲に存在する複合体中のシリカナノ粒子同士が凝集することでシリカ殻が形成できる。一般的にコロイダルシリカはpHが4から7にかけてゲル化速度が速く凝集し易くなることが知られており(26)、pH6で保持することで油滴周囲のシリカ微粒子同士が結合を形成し易くなったと考えられる。
pHinitとpHpostに対する中空粒子率の変化をプロットしたものをFig. 21に示す。図中のプロット円の大きさは中空粒子率に対応している。pHinit=1における中空粒子率が相対的に低く、pHinit=2付近で制御することが中空粒子率を高くする必要条件であることがわかった。この結果は前述のゼータ電位の挙動と整合しないが、その原因として、シリカ粒子の表面が修飾された場合や溶液中に塩が存在する場合に、等電点や準安定状態のpH域が変化することによる影響があげられる。実際、ゼータ電位がプラスとなるpH域が2から3の間と狭い報告例(28)がある。また、pHinit=1の条件では、pHを下げるために溶液中に多量のHClを加えていることによる影響も考慮すべきと思われる。
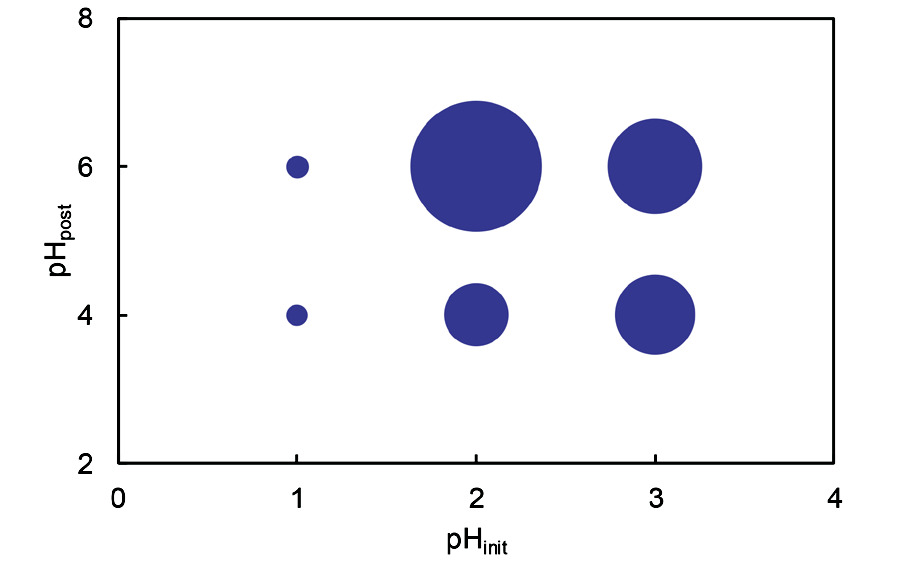
pHpostに着目すると、同一のpHinitであればpHpost=6の中空粒子率の方が高いことがわかる。この結果は上述の仮説を支持したものとなっている。この結果から、pHinit=2、pHpost=6の条件が、微粉もなく中空粒子の生成比率が最も高くなる条件であることがわかる。
4.3. 2段目殻形成工程におけるS/Oおよび煆焼~焼成条件がシリカ殻中の細孔構造に与える影響
本研究で開発した中空シリカナノ粒子は、S/O ≧1.2かつ800 ℃焼成をすることで、実用上十分な機械的強度を有するとともに、水中で保持しても長期間中空性を維持できるという従来に無い特徴を実現した。本節ではこれらの実験結果をもとに、作製した中空シリカ殻のメソポーラス構造について考察する。
Fig. 3に示したように1段目シリカ殻形成終了段階でのオイルコア-シリカシェル粒子は、シリカ殻厚が高々5 nm程度であるため、乾燥させると真球形状を維持できずホオズキ形に変形してしまう。そのため2段目シリカ殻形成工程では希釈珪酸ソーダ水溶液を追加することでシリカ殻の厚さを厚くしている。Fig.22に2段目シリカ殻形成の模式図を示す。2段目工程では、液のpHを9付近で制御することで、液滴界面でシリカ殻を構成しているシリカナノ微粒子の粒成長を促進させ、新たなシリカナノ微粒子が液中に形成することを抑制している。このため、2段目でS/Oの値を0.4~2.2の間で変化させてもFig. 11に示したように微粒子発生量はほとんど変化せず、シリカ殻厚のみを変化させることができた。
3.6節にて述べたように、S/Oと一次粒子径、凝集径、見かけ密度および中空粒子率の間には相関が見られない。一次粒子径はドデカン核の大きさにより決定されるからであるが、凝集径とS/Oの間に相関が見られないのは、加えたSiO2量がシリカ殻の成長に用いられるため、シリカ殻の外で一次粒子間を結合させるような余計なシリカ微粒子が生成しなかったことによると考えられる。また、見かけ密度とS/O間に相関が見られない点は、シリカ殻を構成する微粒子の成長によるメソポーラスな貫通孔の径変化よりも不完全中空粒子における開口部の影響の方が見かけ密度への影響が大きいためと考えられる。さらにTGより算出した中空粒子率とS/O間で相関が見られない点は、S/Oを大きくしても、1段目シリカ形成時に被覆しきれなかった開口部を塞ぐことは困難であることを示唆している。一方で、Fig. 17に示した水中へ長時間浸漬した際の見かけ密度変化の傾きは、シリカ殻のメソポーラスな貫通孔を通じた中空粒子内部への水の侵入しやすさを表わしていると考えられる。Fig. 17からわかるようにS/Oが大きくなるに従い傾きが小さくなることから、S/Oが大きいほど緻密な殻構造を実現できていることが確認できた。
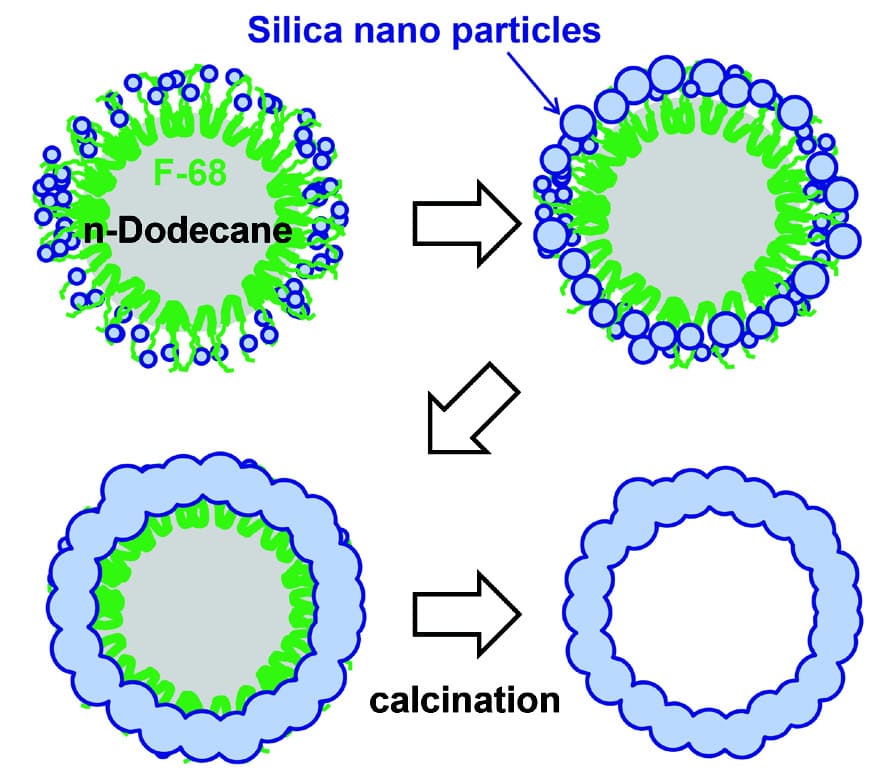
続いて、煆焼~焼成工程におけるシリカ殻の変化について考察する。本手法では中空部を形成するドデカン核および界面活性剤であるF68の除去のために、400 ℃での煆焼処理をおこなっている。400 ℃のシリカ殻はまだ緻密化していないため、ドデカンおよびF68の熱分解・燃焼によって発生するガス成分を粒子外へ脱離させることが可能となっている。なお400 ℃での煆焼処理を省略し、直接650 ℃以上まで昇温した場合、中空内部に有機成分が残留してしまい粒子が茶色に着色することを確認している。
煆焼後の焼成工程において、焼成温度を変化させると、700 ℃以上の焼成では前述した4 nmの細孔ピークの消失に加え、乾式密度測定結果から示唆されるように貫通孔の径変化が生じていると考えられる。この貫通孔の径変化を各分子の大きさをもとに推定する。
Table 3に、ヘリウムガス、酸素ガス、アルゴンガスおよび水分子のファンデルワールス半径および動的分子径を示す(29–33)。ここでは気体分離膜等の検討と同様に動的分子径に着目する。ヘリウムガスは焼成温度によらず通過しているのに対し、酸素ガスとアルゴンガスは700 ℃以上では通過できない。このことから700 ℃以上で焼成した後のシリカ殻に存在する貫通孔は0.26 nmより大きく0.34 nmより小さいと推定される。また、650 ℃以下において酸素ガスプローブにおける測定値がアモルファスシリカの真密度を上まわっている一方で、ほぼ同じ動的分子径であるアルゴンガスプローブでの測定ではこのような現象は見られない。これらのことから、650 ℃以下における貫通孔の径は酸素ガスの動的分子径に近く、クヌーセン拡散というよりも表面拡散に近い状態になっていると推定される。酸素ガスはシリカ殻に対して吸着性を有するために孔内壁へ分子が吸着することで透過速度が低下したと考えられ、密度測定時に測定室内の圧力が平衡になるまでの時間が長くなったり真値からずれたりした結果、見かけ密度値の上昇や測定エラーの発生が生じたものと考えられる。なお、水中に浸漬した場合に容易に水が中空粒子内に侵入しないのは、内部の気体が外部へ移動することが律速になっているためと考えられる。また、シリカに対する水の吸着力が強いことも影響していると考えられる。
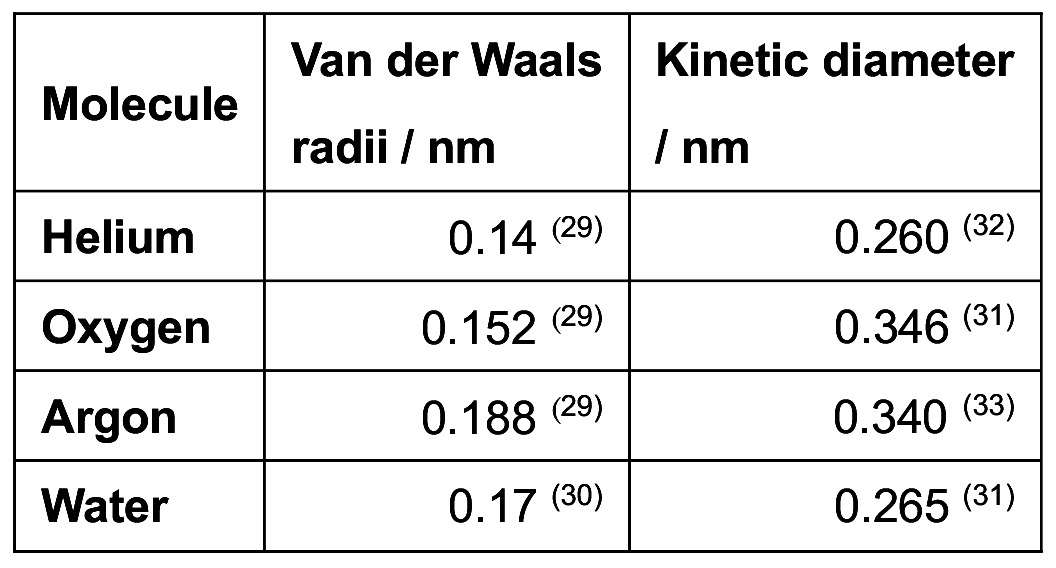
4.4. 中空粒子率の低減・制御に向けた影響因子の同定
中空シリカナノ粒子における不完全中空粒子の存在は、中空性を低下させるという観点からは欠陥であるが、意図的に存在させることにより吸油率や比重を制御、開口部の大きさによっては界面張力差を利用した徐放性の実現といった応用も考えることができる。そこで単純な低減だけでなく、積極的な制御の可能性も念頭に影響因子について考察した。
不完全中空粒子の生成メカニズムには大きく以下の4つが考えられる。
- 1段目シリカ殻形成段階におけるドデカン核の不完全な被覆
- 煆焼~焼成工程にて脱離する有機成分の膨張にともなう破裂
- 解砕工程における機械的強度の低さによる破壊
- 結合して殻形成していた粒子が解砕工程で分離することによる開口部生成
ここで、C) については殻厚が今回検討した範囲内であれば、解砕や超音波照射の条件を適切に選択することで回避できることを確認した。D) についてはSEM観察結果から本研究における作製条件下ではそれほど確認できなかった。もっとも多く見られる不完全粒子の形状は、粒子の一部が割けたように見えるものである。当初この発生要因としてB) を懸念していたが、熱処理工程前後でのSEM観察において不完全粒子が増えているようには見えないこと、密度の低下も見られないことから主要因ではないと判断した。一方でA) は、液中試料のTEM観察結果(Fig. 5)からもわかるように、1段目シリカ殻形成において存在していることが確認できた。また、4.3節で述べたように、1段目で中空粒子率が低い条件では、2段目シリカ殻形成で条件を振っても中空粒子率の改善につながらない。以上より、不完全中空粒子を低減、制御するには、1段目シリカ殻形成反応のpH制御が重要であると考えられる。現状では、pH変動に対する粒子形状の変化が大きく、制御性に課題がある。積極的な活用にはpHに対する形状変化の感度を低減させる添加物の検討等が必要であると考えられる。
4.5. 水中で長期保管した際の中空内への水侵入挙動の推定
本研究で開発した中空シリカナノ粒子は800 ℃で焼成することで緻密な殻構造を実現することができるため、例えば、800 ℃焼成後中空シリカナノ粒子(比重約1.0) では、1ヶ月間水中に保持しても中空粒子内へ水が侵入しないため比重と光散乱性が変化せず、均一分散して白濁した状態を維持することを確認している。
中空粒子内へ水が侵入すると、もともと中空内部に存在していた空気と水が一部置換されて、Fig. 23に示すような空気層、水層、シリカ殻層の3層からなる構造となると仮定できる。この時、中空部全体に対する粒子内へ侵入した水の体積比をxとおくと、中空シリカナノ粒子の見かけ密度d(x)は以下のように表すことができる。

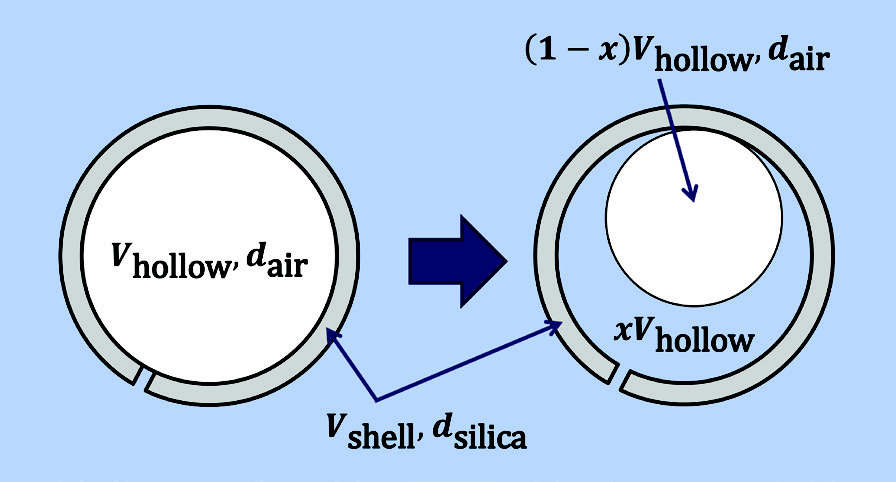
式中Vshell,Vhollow はシリカ殻および中空部の体積、dsilica,dair はそれぞれアモルファスシリカおよび空気の密度である。Fig. 24に、d(0)=0.8の場合のxに対する見かけ密度変化Δdの関係を示す。ここでは、Δd=d(x)- d(0)である。
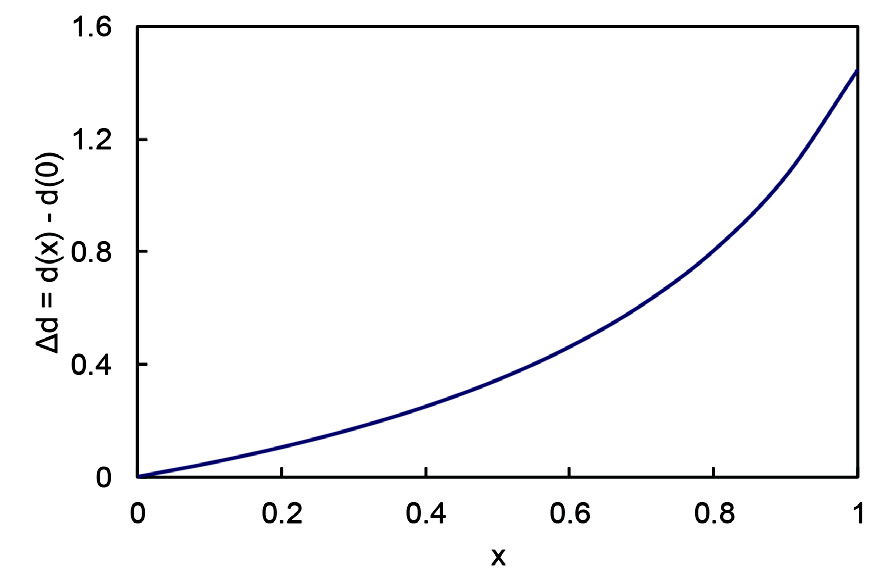
中空部の直径が300 nm、殻厚が20 nmである800 ℃焼成後中空シリカナノ粒子 (S/O=1.2) を室温(25 ℃)下で水中に保持した際に、x=0.3となる、つまり中空部の3割が水に置換されて散乱に寄与する残存気泡の体積が初期の7割まで低下するまでにかかる日数を、本モデルをもとに推算した。Fig. 15から算出した浸漬温度と一日あたりの見かけ密度変化の関係をFig. 25に示す。この図から25 ℃における1日あたりの見かけ密度変化は110 ℃の場合と比べて約7 %程度と見積ることができる。この結果とFig. 16をもとに、見かけ密度がΔd上昇するのに要する日数をプロットした結果をFig. 26に示す。■は800 ℃焼成後中空シリカナノ粒子 (S/O=1.2) を110 ℃下で保持した際の実測結果であり、破線はその線形回帰直線、赤実線は25 ℃の水中で保持した際の予測線である。また、Δdに対応するの値を第2横軸としてあわせて示した。Fig. 26から、x=0.3に到達するのに要する日数は、110 ℃浸漬では約50日であるのに対し25 ℃浸漬では約730日と予測される。x=0.3に対応する実サンプルの外観も110 ℃で50日間浸漬後もほとんど変化が無いことから、2年間室温の水中で保管してもほとんど外観変化を生じない可能性が高いことが示唆された。
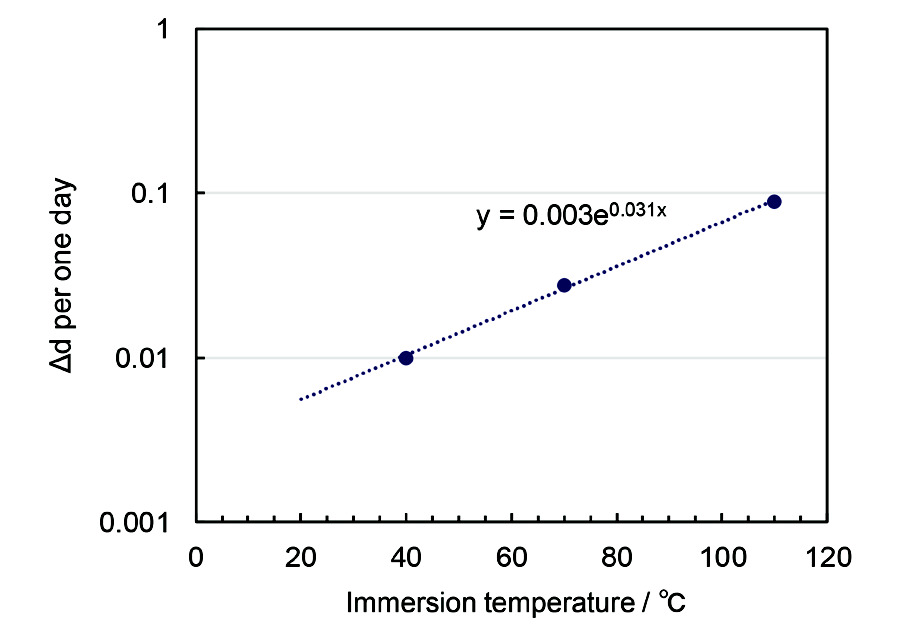
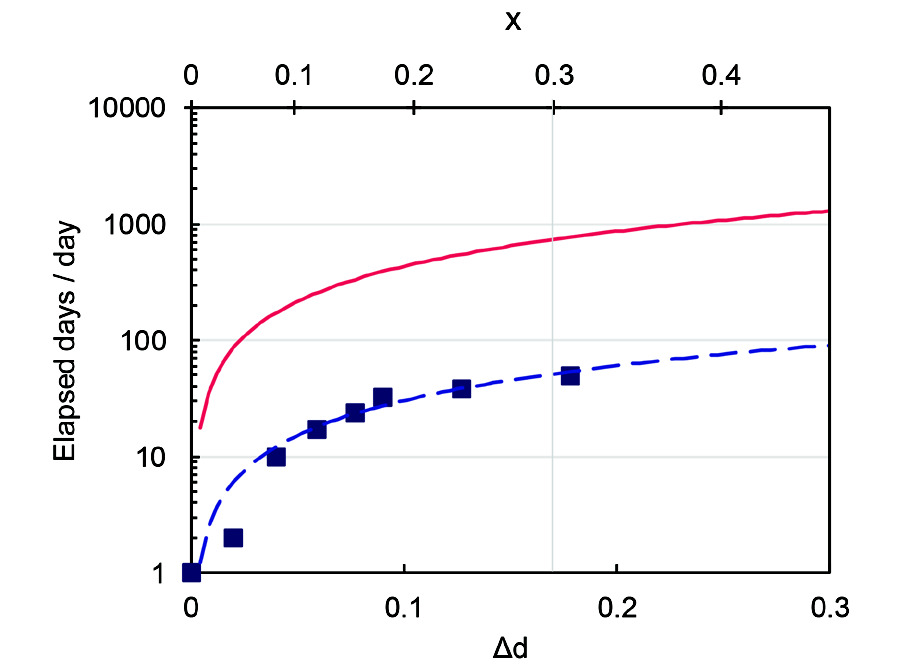
本考察は110 ℃浸漬試験結果をもとに予測したが、シリカの溶出による貫通孔径の変化や水侵入が進行することによる駆動力の変化等は考慮していない。110 ℃におけるアモルファスシリカの水への溶解度は25 ℃にくらべて3倍近く大きい(26)ため、実際の水侵入速度はより低い可能性がある。水侵入に伴い中空内部の気泡径が小さくなることで界面張力差が大きくなる、粒子内外での溶存気体濃度差が小さくなるなどの環境変化により、実際の長期浸漬では水侵入の駆動力が変化することも考えられる。これらの影響を考慮に入れた予測モデルの検討は今後の課題である。また、本考察では一例としてx=0.3 に要する浸漬日数を見積ったが、今後は、中空内への水侵入による光散乱性の変化について、実測結果とシミュレーション結果を比較することで、光散乱性に影響が無い水侵入率の範囲の明確化についても検討を進める予定である。
5. 総括
本研究では、液体核と珪酸ソーダを出発原料とし、2段階のシリカ殻形成工程により前駆体を作製し、これを400 ℃で煆焼、650 ℃~800 ℃で焼成することで、真球形状の中空シリカナノ粒子が得られることを示した。中空シリカナノ粒子の粒径はO/Wエマルションの油滴径で変化させることができ300 nm~700 nmの範囲で制御可能であること、殻厚はS/Oを変化させることで17 nm~32 nmの範囲で制御可能であること、この範囲で実用的な強度を有する中空シリカナノ粒子が得られることが示された。1段目シリカ殻形成時のpH制御によって、油滴をシリカナノ微粒子で完全に被覆することが中空粒子率向上の支配要因であることを見出し、欠陥の少ない中空シリカナノ粒子を得るためには、希釈珪酸ソーダ水溶液添加中のpHを2とし添加後pHを6とすることが適当であることを、シリカ殻形成機構の仮説とあわせて示した。また、2段目シリカ殻形成時のS/Oを高くすることおよび700 ℃以上で焼成をすることでシリカ殻が水やアルゴンガスを透過しない程度まで緻密化することを示した。特に800 ℃焼成後の中空シリカナノ粒子は水中で長期間保持しても中空内への水侵入が抑制されるため、中空粒子内への水侵入モデルを基に、室温下であれば2年程度光散乱性および水中での分散性を維持できる可能性があることを示した。
本研究において確立した新規中空シリカナノ粒子形成手法によれば、比較的安価な原料とプロセスによって、従来品では実現困難な粒径100 nm~1µmの範囲で、粒径、殻厚、比重を制御可能で、実用上十分な機械的強度を持ち、水中でも長期間中空構造を維持可能であるという優れた特長を有する中空シリカナノ粒子を製造できることを示した。本成果は、近年注目を集めつつある化粧品用樹脂粒子代替、電子デバイス用の低誘電、断熱用フィラー材料、反射防止塗膜、ドラッグデリバリー等のバイオ・医薬等分野への展開が期待される。これら各種の応用展開に向けた機能性付与について現在鋭意検討中である。
参考文献
- Wang, J., Yu, J., Zhu, X. & Kong, X. Z. Preparation of hollow TiO2 nanoparticles through TiO2 deposition on polystyrene latex particles and characterizations of their structure and photocatalytic activity. Nanoscale Res. Lett. 7, 646 (2012).
- Nomura, T., Tanii, S., Ishikawa, M., Tokumoto, H. & Konishi, Y. Synthesis of hollow zirconia particles using wet bacterial templates. Adv. Powder Technol. 24, 1013–1016 (2013).
- Gyger, F., Hübner, M., Feldmann, C., Barsan, N. & Weimar, U. Nanoscale SnO2 hollow spheres and their application as a gas-sensing material. Chem. Mater. 22, 4821–4827 (2010).
- Chen, S., Chen, Z., Luo, Y., Xia, M. & Cao, C. Silicon hollow sphere anode with enhanced cycling stability by a template-free method. Nanotechnology 28, 165404 (2017).
- Li, S., Pasc, A., Fierro, V. & Celzard, A. Hollow carbon spheres, synthesis and applications-a review. Journal of Materials Chemistry A vol. 4 12686–12713 (2016).
- Bommel, K. J. C. van, Hwa Jung, J. & Shinkai, S. Poly(L-lysine) Aggregates as Templates for the Formation of Hollow Silica Spheres. Adv. Mater. 13, 1472–1476 (2001).
- Lin, H., Cheng, Y. & Mou, C. Hierarchical Order in Hollow Spheres of Mesoporous Silicates. Chem. Mater. 10, 3772–3776 (1998).
- Li, W., Sha, X., Dong, W. & Wang, Z. Synthesis of stable hollow silica microspheres with mesoporous shell in nonionic W/O emulsion. Chem. Commun. 2, 2434–2435 (2002).
- Du, Y., Luna, L. E., Tan, W. S., Rubner, M. F. & Cohen, R. E. Hollow silica nanoparticles in UV - Visible anti reflection coatings for poly(methyl methacrylate) substrates. ACS Nano 4, 4308–4316 (2010).
- Schacht, S., Huo, Q., Voigt-Martin, I. G., Stucky, G. D. & Schüth, F. Oil-Water Interface Templating of Mesoporous Macroscale Structures. Science. 273, 768–771 (1996).
- Xu, L. & He, J. Fabrication of highly transparent superhy drophobic coatings from hollow silica nanoparticles. Langmuir 28, 7512–7518 (2012).
- 河合洋平 & 米田貴重. 中空状を含有する分散液、塗料組成物及び反射防止塗膜付き基材, 日本国特許 P2006-335881A (2006).
- Yanagisawa, T., Shimizu, T., Kuroda, K. & Kato, C. Trimethylsilyl Derivatives of Alkyltrimethylammonium–Kanemite Complexes and Their Conversion to Microporous SiO2 Materials . Bull. Chem. Soc. Jpn. 63, 1535–1537 (1990).
- Kresge, C. T., Leonowicz, M. E., Roth, W. J., Vartuli, J. C. & Beck, J. S. Ordered mesoporous molecular sieves synthesized by a liquid-crystal template mechanism. Nature 359, 710–712 (1992).
- Attard, G. S., Glyde, J. C. & Göltner, C. G. Liquid-crystalline phases as templates for the synthesis of mesoporous silica. Nature 378, 366–368 (1995).
- Rana, R. K., Mastai, Y. & Gedanken, A. Acoustic Cavitation Leading to the Morphosynthesis of Mesoporous Silica Vesicles. Adv. Mater. 14, 1414–1418(2002).
- Fowler, C. E., Khushalani, D. & Mann, S. Interfacial synthesis of hollow microspheres of mesostructured silica. Chem. Commun. 1, 2028–2029(2001).
- Hubert, D. H. W. et al . Vesicle-Directed Growth of Silica. Adv. Mater. 12, 1286–1290(2000).
- Jafelicci, M., Davolos, M. R., Dos Santos, F. J. & De Andrade, S. J. Hollow silica particles from microemulsion. J. Non. Cryst. Solids 247, 98–102(1999).
- Sun, Q. et al. The Formation of Well-Defined Hollow Silica Spheres with Multilamellar Shell Structure. Adv. Mater. 15, 1097–1100(2003).
- Zhang, L. et al. Hollow silica spheres: Synthesis and mechanical properties. Langmuir 25, 2711–2717(2009).
- Nandiyanto, A. B. D., Akane, Y., Ogi, T. & Okuyama, K. Mesopore-free hollow silica particles with controllable diameter and shell thickness via additive-free synthesis. Langmuir 28, 8616–8624(2012).
- Sharma, J. et al . Hybrid hollow silica particles: Synthesis and comparison of properties with pristine particles. RSC Adv. 10, 22331–22334(2020).
- Jo, S. M., Jiang, S., Graf, R., Wurm, F. R. & Landfester, K. Aqueous core and hollow silica nanocapsules for confined enzyme modules. Nanoscale 12, 24266–24272(2020).
- 3MTM グラスバブルズ|3M. https://www.3mcompany.jp/3M/ja_JP/company-jp/all-3m-products/~/All-3MProducts/高機能材料/グラスバブルズ.
- Iler, R. K. The Chemistry of Silica: Solubility, Polymerization, Colloid and Surface Properties and Biochemistry of Silica.(Wiley-Interscience, 1979).
- Sehlleier, Y. H., Abdali, A., Schnurre, S. M., Wiggers, H. & Schulz, C. Surface functionalization of microwave plasmasynthesized silica nanoparticles for enhancing the stability of dispersions. J. Nanoparticle Res. 16,(2014).
- Xu, P., Wang, H., Tong, R., Du, Q. & Zhong, W. Preparation and morphology of SiO2/PMMA nanohybrids by microemulsion polymerization. Colloid Polym. Sci. 284, 755–762(2006).
- Bondi, A. Van der waals volumes and radii. J. Phys. Chem. 68, 441–451(1964).
- Li, A.-J. & Nussinov, R. A set of van der Waals and coulombic radii of protein atoms for molecular and solventaccessible surface calculation, packing evaluation, and docking. Proteins Struct. Funct. Genet. 32, 111–127.(1998).
- Ismail, A. F., Khulbe, K. & Matsuura, T. Gas Separation Membranes: Polymeric and Inorganic.(Springer, 2015).
- Matteucci, S., Yampolskii, Y., Freeman, B. D. & Pinnau, I. Transport of gases and vapors in glassy and rubbery polymers. in Materials Science of Membranes for Gas and Vapor Separation 1–47( John Wiley & Sons, Ltd, 2006).
- Breck, D. W. Zeolite Molecular Sieves: Structure, Chemistry, and Use.(Wiley, 1974).