AGC Research Report 74(2024)
熱可塑性複合材料の樹脂部非弾性変形を考慮した疲労寿命予測
Predicting the Fatigue Life of Thermoplastic Resin Composites Considering the Non-Elastic Deformation of the Resin Component
秋田幸仁*・吉川暢宏**
Yukihito Akita, and Nobuhiro Yoshikawa
*AGC株式会社 先端基盤研究所(yukihito.akita@agc.com)
**東京大学 生産技術研究所(nobyoshi@iis.u-tokyo.ac.jp)
第5世代移動通信システム(5G)のプリント基板において、低誘電損失に期待してPTFEなどの熱可塑性樹脂を母材とする複合材料の活用が試みられている。熱可塑性複合材料の強度部材への適用には、長期の信頼性を保証する疲労強度設計が不可欠である。しかし、熱可塑性複合材料の母材として用いられる熱可塑性樹脂は著しい塑性変形を示すため、疲労寿命を予測することが困難である。本研究では、熱可塑性樹脂であるポリアミド6(PA6)を母材とした一方向熱可塑性炭素繊維強化プラスチック(CFRTP)試験片に関して、Interfacial Plastic Strain Energy(IPSE)を基準とした疲労寿命予測の有効性を検証した。CFRTP内部のPA6は高い静水圧を受けるため、Drucker-Prager降伏条件を適用した。そしてツースケール解析により、CFRTP試験片のマクロ応力を正確に予測し、ミクロスケールにおける局所的な力学場からIPSEを算出する手法を提案した。一軸引張試験と一軸圧縮試験から得られた内部摩擦角を適用して、CFRTP内部のPA6の塑性ひずみエネルギーを算出した。そして、疲労試験により得られた応力-破断サイクル数線図を塑性ひずみエネルギーΔWp-破断サイクル数線図に変換し、PA6単体とCFRTP内部のPA6の疲労線図を比較した。その結果、疲労線図はよく一致しており、PA6単体の疲労試験結果からIPSE評価手法を適用することで、CFRTPの疲労寿命が高精度に予測できることが示された。
To develop printed circuit boards for fifth-generation mobile communication systems, composite materials using thermoplastic resins, such as polytetrafluoroethylene, are being investigated because of their low dielectric loss. To apply these composites as structural components, high fatigue strength is essential to guarantee long-term reliability. However, the thermoplastic resins used as the matrix in these composites exhibit significant plastic deformation, complicating the prediction of their fatigue life. Therefore, in this study, we investigated the applicability of interfacial plastic strain energy (IPSE) for predicting the fatigue life of unidirectional carbon fiber reinforced thermoplastic (CFRTP) specimens employing polyamide 6 (PA6) as its matrix. We applied the Drucker–Prager yield criterion for the estimation under high hydrostatic pressure. We proposed a method for precisely estimating the macro stress of the CFRTP specimens using a two-scale analysis and the IPSE from localized mechanical fields at the microscale. We used the internal friction angle obtained from uniaxial tension and compression tests to calculate the IPSE of the PA6 in the CFRTP. Furthermore, we converted the stress-number of cycles to failure curve obtained from fatigue tests into the plastic strain energy-number of cycles to failure curves and compared the fatigue diagrams of pure PA6 and the PA6 in the CFRTP. The results showed excellent agreement between the fatigue diagrams, confirming that the IPSE evaluation method based on the fatigue test of pure PA6 is sufficiently accurate for estimating the fatigue life of the CFRTP.
1. 緒言
第5世代移動通信システム(5G)のプリント基板において、低誘電損失に期待してPTFEなどの熱可塑性樹脂を母材とする複合材料の活用が試みられている。熱可塑性複合材料の強度部材への適用のためには、長期の信頼性を保証する疲労強度設計が不可欠である[1-2]。熱可塑性複合材料の母材として多用されている6ナイロン(Polyamide 6:PA6)[3-4]やポリエーテルエーテルケトン樹脂(Poly Ether Ether Ketone:PEEK)[5-6]については、樹脂単体の疲労寿命に関する研究が行われているが、それらを母材とした熱可塑性複合材料の疲労寿命に関する研究は希少であり[7-8]、疲労メカニズムに関して不明な点が多い。
熱可塑性複合材料試験片を用いた疲労試験結果を公称応力や公称ひずみに注目して、金属材料類似の応力-ひずみ(S-S)曲線を描こうとすると、樹脂含有率や強化材の配向さらには積層構成が異なれば全く異なるS-N関係を呈する。試験片の諸元ごとに網羅的に疲労試験を実施することは現実的ではない。この状況を打開するため、樹脂と強化材の強度モデルを明確に区分して、ミクロスケールでの考察から一般性の高い疲労寿命予測を行う試みもなされている。Plumtreeら[9]はSmith Watson Topperの疲労損傷パラメータを開発し適用した。Petermannら[10]はひずみエネルギー密度を適用した。Varvani-Farahaniら[11]はエネルギーに基づく疲労損傷パラメータを開発した。これらの手法は連続体モデルを設定し、疲労寿命予測パラメータから予測される疲労試験結果が実験結果を適切に予測できるものとなっていることで、経験則的に適切さを示している。本研究でも同様の方法論をとり、強化材と樹脂を区分し、強化材が規則的に配置された確定的なミクロモデルを用いて解析された疲労寿命予測パラメータと疲労寿命との相関を明らかにし、疲労寿命予測が適切に行えることをもって、疲労寿命予測パラメータとしての妥当性の根拠とする。
著者の一人は、熱硬化性CFRP(Carbon Fiber Reinforced Plastic)試験片を対象として、ミクロスケール解析により得られる Interfacial Normal Stress:INSにより疲労寿命を予測する汎用的な手法を提案している[12-14]。INSはHojoら[15-16]により提案されたパラメータであり、炭素繊維間の樹脂部に作用する2本の炭素繊維を引き離す垂直応力であり、in-situ SEM観察から測定されたトランスバースクラック強度を支配することが示されている。INSに基づく疲労寿命予測法は応力規準であるため、ミクロスケールでの樹脂挙動が弾性体に近い熱硬化性CFRPの高サイクル疲労領域で有効であり、低荷重であってもミクロスケールで視れば樹脂に相当の塑性変形が生じる熱可塑性複合材料試験片[17]に対しては適用が難しいと思われる。
そこで本研究では、熱可塑性樹脂であるPA6を母材とした一方向CFRTP(Carbon Fiber Reinforced Thermoplastic)試験片に関して、INSに代わる塑性ひずみエネルギー規準をInterfacial Plastic Strain Energy:IPSEにより設定した。IPSEを隣接する炭素繊維を最短距離で結ぶ線分の中点における、線分に垂直な面に関する垂直塑性ひずみエネルギーとせん断塑性ひずみエネルギーの和と定義する。CFRTP内部のPA6は成型時に繊維方向に球晶構造が扁平するため疲労強度の異方性が現れると思われる。そのため、金属材料のように相当塑性ひずみエネルギーを適用せずに、方向を指定して塑性ひずみエネルギーを求めることが妥当と考えた。
CFRTP試験片内部のPA6のミクロスケール力学場は炭素繊維の強い拘束を受けるため、高い平均垂直応力(静水圧)を受ける。高分子材料は静水圧により弾塑性構成則が変化することが知られている[18-20]ため、Drucker-Prager降伏条件を適用した。Drucker-Pragerパラメータの内部摩擦角は、一軸引張試験と一軸圧縮試験から降伏応力を求めることで算出した。そして得られた内部摩擦角を適用して、提案するIPSE評価手法により、CFRTPの疲労寿命を予測することの有効性を示すことを目的とする。傾斜繊維配向CFRTP試験片に一軸荷重を与えると、面内カップリング効果により複雑な応力分布を示す。そこで本研究では、ミクロスケールモデルとマクロスケールモデルを連成させたツースケール解析を適用することにより、試験片に作用する応力を正確に予測した。
2. Off-axis荷重におけるCFRTPの疲労試験
2.1. 疲労試験方法
CFRTPの平板試験片の形状をFig. 1に示す。試験片はASTM D3039に準拠しており、疲労試験機との掴み部で破断しないようにアルミニウム製のタブを接着させた。繊維配向が荷重方向に対して90°、60°および30°となるように3種類の一方向強化試験片とした。一方向強化プリプレグを14層積層し、圧力11.5MPa、温度250℃で10分間保持するホットプレスにより成形した。炭素繊維は東レ製のT700SCとした。炭素繊維の体積含有率はJIS K 7075に準拠した硫酸分解法により63.7 %と測定された。試験機はMTS製370.10油圧サーボ疲労試験機である。荷重負荷波形を正弦波とし、応力比は0、繰り返し周波数は10 Hzとした。

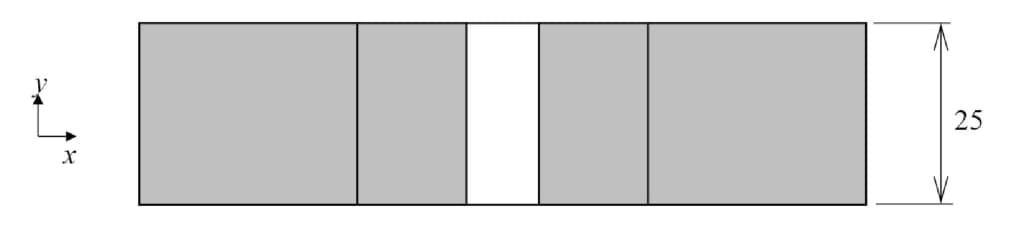
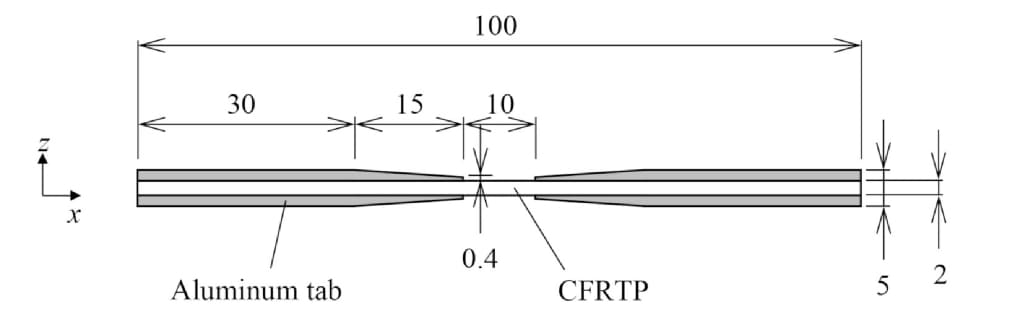
2.2. 疲労試験結果
疲労試験により得られたS-N 線図をFig. 2に示す。先行研究[21]により得られたPA6単体の疲労線図も併せて示す。CFRTPの疲労強度は30°、90°、60°の順に高くなった。一般的な熱硬化性CFRPは繊維配向が0°に近いほど疲労強度は高くなる[9-12]が、そのような序列にはならなかった。これは、傾斜繊維配向CFRTPは面内カップリング効果により、荷重に垂直な断面で応力が均一にならなかったためと考えられる。また、傾斜繊維配向CFRPはミクロスケールにおける樹脂部でせん断応力が発生する。球晶構造を有するPA6はせん断応力に対して弱いため、疲労強度が低下したと考えられる。
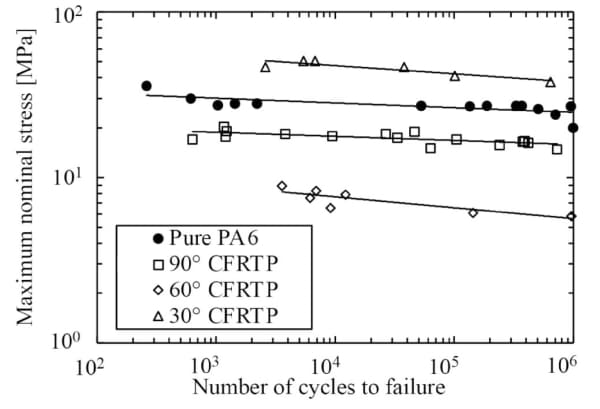
傾斜繊維配向CFRTPの疲労試験後の代表的な破断写真をFig. 3に示す。全ての疲労試験片は試験片中央付近で破断した。繊維破断はほとんど起きておらず、繊維配向に沿うように破壊する形態を示した。
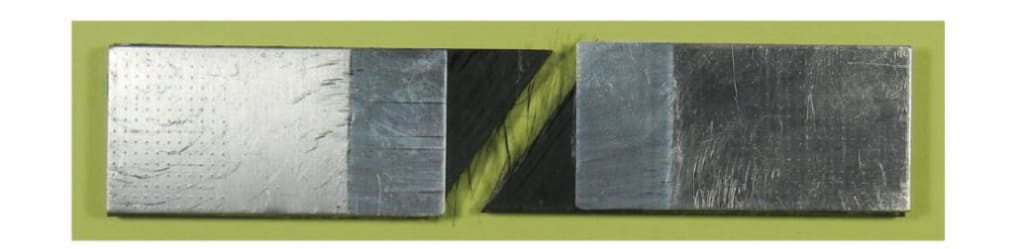
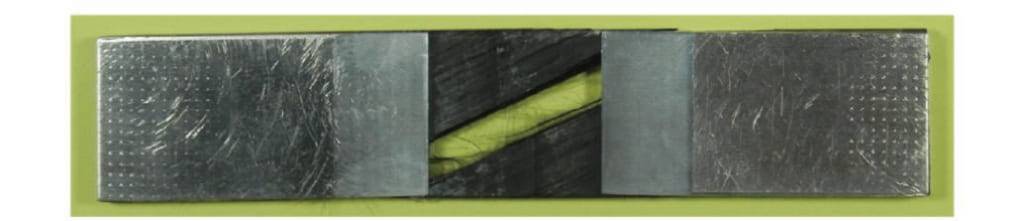
3. 塑性ひずみエネルギーによるCFRTPの疲労寿命予測
3.1. 塑性ひずみエネルギーの同定方法
PA6の疲労試験は荷重制御であり、ひずみは測定していない。そこで、PA6単体の静的引張試験により得られたS-S 曲線から塑性ひずみエネルギーを予測する手法を提案する。また、CFRTP内部のPA6に発生する塑性ひずみエネルギーの同定方法も提案する。
PA6単体の塑性ひずみエネルギーΔWpの予測手法の概要図をFig. 4に示す。弾塑性曲線は次式により示される。
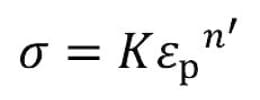
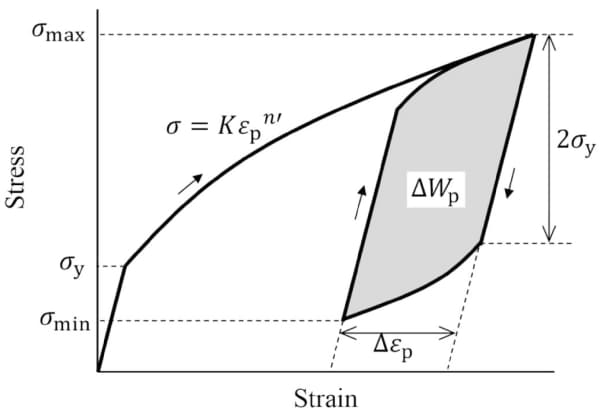
ここで、Kは加工硬化係数、n'は加工硬化指数である。静的引張試験によりK=132[MPa]、n'=0.337と測定された。なお、疲労試験の最大応力はσmax、最小応力はσminとし、PA6の降伏応力をσyとする。PA6に引張荷重を与えると、はじめに降伏応力σyまで弾性変形する。その後塑性変形し、最大応力σmaxに達してから除荷となる。本研究では移動硬化則に基づき、除荷開始から次の降伏応力までの応力範囲は2σyとした。除荷時の塑性変形においても、最初の引張負荷時と同じS-S曲線を描くものとした。そして最小応力σminに達してから再び引張負荷となる。このように引張負荷と除荷を繰り返すことによるヒステリシスループのひずみの幅が塑性ひずみ範囲Δεpである。またヒステリシスループを囲む面積が塑性ひずみエネルギーΔWpである。塑性ひずみエネルギーは次式により求められる[22]。
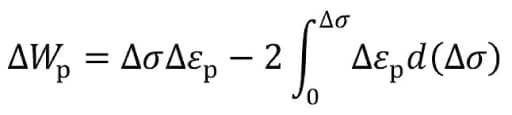
ここで、Δσは応力範囲であり、次式により求まる。
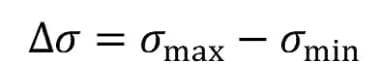
Radhakrishnan[23]がこの数式により求められた塑性ひずみエネルギーとヒステリシスループの面積がよく一致していることを確認している。式(1)を用いると、式(2)から次式を得る。
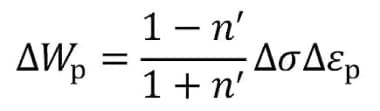
式(4)を適用することで、PA6単体の疲労試験結果から塑性ひずみエネルギーを算出することができる。 一方、CFRTP内部のPA6における塑性ひずみ範囲については、Fig. 5に示すIPSE評価点において、炭素繊維軸間を結ぶ方向に働く垂直応力-垂直ひずみ曲線を弾塑性解析より出力した。そしてFig. 4に示すヒステリシスループを仮定して垂直塑性ひずみ範囲を算出した。そして、垂直塑性ひずみエネルギーは次式により求められる。
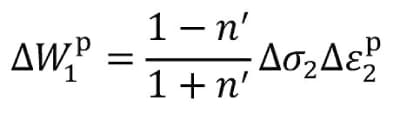
ここで、Δσ2は2本の炭素繊維を引き離す方向の垂直応力範囲である。同様に、せん断寄与による塑性ひずみエネルギーは次式により求められる。
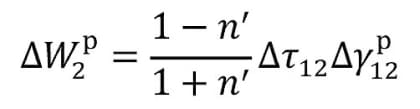
Δτ12は炭素繊維軸間を最短で結ぶ線分に垂直な面に働くせん断応力範囲であり、は同平面上におけるせん断塑性ひずみ範囲である。垂直寄与とせん断寄与の塑性ひずみエネルギーの和を取ることで、次式のIPSEを得る。
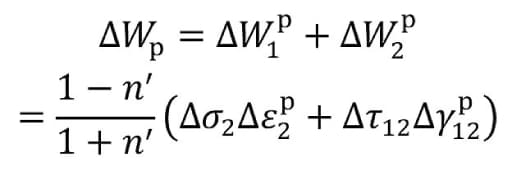
PA6単体試験片は式(4)から塑性ひずみエネルギーを求め、CFRTP内部のPA6は式(7)からIPSEを求める。そして塑性ひずみエネルギーを疲労寿命予測パラメータとしてΔWp-N 線図を比較し、同一直線状に乗ることを確認して疲労寿命予測手法の妥当性を評価する。
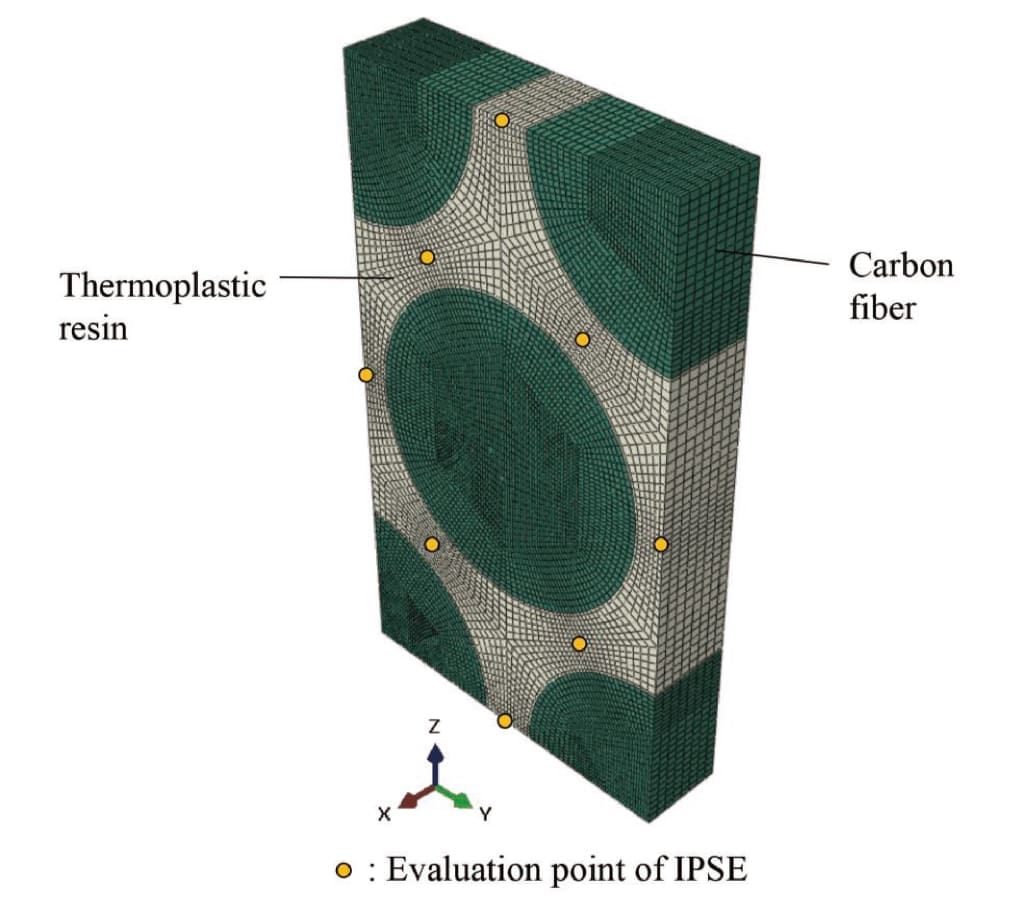
3.2. CFRTP試験片のツースケール解析
傾斜繊維配向CFRTP試験片は面内カップリング効果により、複雑な応力分布を示す。そこで、試験片に発生する応力を正確に評価するため、ツースケール解析を実施した。ミクロモデルは炭素繊維を最密充填構造としたユニットセルモデルとし、マクロモデルは試験片スケールのモデルとした。
はじめに、ユニットセルモデルを用いて、CFRTPの等価な異方性物性値を求めた。ユニットセルモデルはMoritaら[12]の方法に倣い、Fig. 5に示すモデルを適用した。節点数73631、要素数64064の8節点6面体1次要素を適用し、6表面に周期境界条件を設定した。解析はAbaqus ver. 2017を使用した。炭素繊維の体積含有率は疲労試験に用いた試験片から実測して63.7%とした。炭素繊維はT700SCであり、直交異方性線形弾性体としてMounierら[24]の研究を参考にEL = 235 GPa、ET = 18.08 GPa、GLT = 15.0 GPa、GTT = 10.0 GPa、νLT = 0.26、νTT = 0.26とした。ここで、Lは繊維方向成分、Tは繊維と垂直方向成分を表す。母材のPA6はヤング率E = 1.46 GPa、ポアソン比 ν = 0.44とした。そして、外力として3方向の垂直応力と3方向のせん断応力をそれぞれ付与して求めたCFRTPの等価な直交異方性物性値は、EL = 150 GPa、ET = 6.17 GPa、GLT = 2.01 GPa、GTT = 2.12 GPa、νLT = 0.32、νTT = 0.58である。
次にFig. 6に示す試験片モデルの弾性解析により、CFRTP試験片に作用するマクロ応力成分を算出した。CFRTPの引張試験により、S-S 曲線は大きな非線形性を示さない結果を得ており、弾性解析で十分に応力を評価できると考えた。90° CFRTPモデルは節点数20943、要素数4144、傾斜繊維配向CFRTPモデルは節点数48003、要素数10064の20節点6面体2次要素を適用した。解析はAbaqus ver. 2017を使用した。対称性を利用して1/2モデルとし、対称面はz 方向変位拘束とした。片側のチャック部はx 方向とy 方向の変位を拘束した。もう一方のチャック部はy 方向変位を拘束し、x 方向変位は全ての節点で同じ変位量となるように多点拘束条件とした。CFRTPはユニットセルモデルで同定した直交異方性物性値とし、アルミニウムはヤング率72.0 GPa、ポアソン比0.33の線形弾性体とした。そして、応力の評価点を決めるためにCFRTPの応力分布を評価した。CFRTPの最大応力位置は、アルミニウムタブの端部との接着部であり、特異応力場となる。このような局所応力が発生する箇所は、CFRTPの非弾性変形により応力が緩和することが想定される。そこで、荷重負荷時にポアソン効果により断面積の減少が最も起こると思われる、試験片の長手方向に対して中央断面を評価点とした。また疲労試験により得られた破断位置はFig. 3に示す通り試験片の中心であったため、マクロ応力の評価位置も試験片の中心とした。また参考として、マクロ応力成分σL 、σT 、τLTの理論値を次式により求めた。
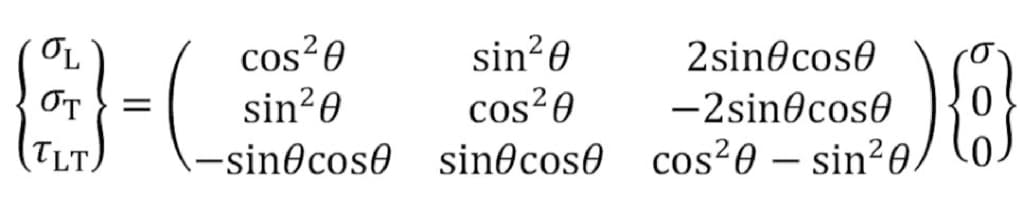

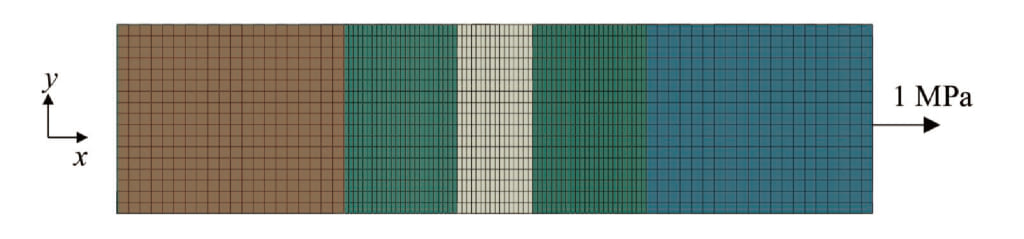

ここで、σは試験応力であり、ここでは1 MPaとした。またθは繊維配向角度である。理論値と試験片モデルの弾性解析により求められたマクロ応力成分を比較してTable 1に示す。90° CFRTP試験片は理論値通りの応力成分を示した。一方、面内カップリング効果が働く傾斜繊維配向CFRTPについては、理論値と大きく異なる解析結果が得られた。樹脂部破壊に強く影響すると思われるσTとτLTをみると、 30° CFRTP試験片は理論値と大きく乖離した。繊維配向が0°に近いほど炭素繊維の両端が拘束されている本数の割合が多く、樹脂部破壊の原因となる応力成分が発生しづらかったためではないかと考えられる。

次に、得られたマクロ応力成分を荷重条件として、Fig. 5に示すユニットセルモデルの弾塑性解析を実施した。PA6はDrucker-Prager降伏条件による弾塑性体としてモデル化した。静水圧依存型の降伏条件であるDrucker-Prager降伏条件は次式で示される[25]。

ここで、σ_eqは単軸試験などから得られる流動応力、p=-σii/3は静水圧である。本研究では、全方向から圧縮が作用する場合に、静水圧が正の値となるように定義した。σ0は静水圧がない状態での降伏応力を表す。βは内部摩擦角であり、相当応力と静水圧の関係をグラフで示した時の傾きを示す。内部摩擦角は一軸引張試験と一軸圧縮試験により得られる降伏応力から求めることができ、本研究で対象とするPA6は23.8°と測定された。高分子材料では高静水圧下での塑性変形後の体積変化は著しく小さいという報告[26]から、塑性変形による体積変化が含まれないように非関連流れ則を定義した。したがって塑性ひずみ速度は次式で示される。
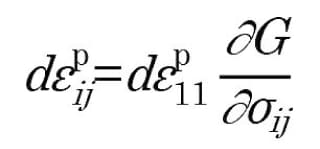
ここで、は応力および負荷履歴に依存する正値のスカラー関数である。G は塑性ポテンシャルであり、偏差応力の第2不変量J2を用いて次式で表される。
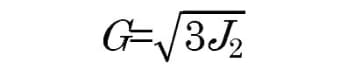
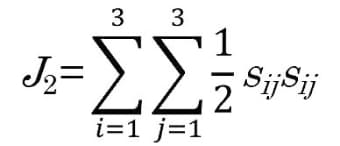
式(10)の塑性構成則を用いて、ユニットセルモデルの弾塑性解析により得られたIPSE評価点での応力と塑性ひずみ成分から、式(7)によりI PSEを算出した。
3.3. CFRTPの疲労寿命予測結果
PA6単体は式(4)により疲労試験結果からΔWp-N 線図を算出した。一方、CFRTP試験片はツースケール解析を行い、式(7)からCFRTP内部のPA6のΔWp-N 線図を算出した。PA6単体とCFRTP内部のPA6のΔWp-N 線図を比較してFig. 7に示す。PA6単体の疲労線図と比べて、各繊維配向のCFRTPの疲労線図はよく一致しており、高精度にCFRTPの疲労寿命が予測できることが示された。参考として、IPSE評価点におけるvon Mises応力と相当塑性ひずみを用いて、式(4)からΔWp-N線図を算出した結果をFig. 8に示す。Fig. 7のIPSEによる予測結果と比べて、P6単体と90° CFRTPの疲労線図の差異が大きくなった。次いで60° CFRTPの差異が大きく、30° CFRTPはほとんど変わらない結果となった。これはCFRTP内部の静水圧が影響しているものと思われる。静水圧は90°、60°、30°の順に小さくなる。90° CFRTPのように高い静水圧が作用する場合、IPSE評価点における垂直応力と相当応力は大きく異なる。そのため、繊維配向が90°に近いほど予測精度が低下したものと思われる。CFRTP内部のPA6は球晶が扁平し、疲労強度の異方性を有すると考えられるため、相当応力や相当塑性ひずみを適用するのではなく、繊維配向により決定される座標系を基にIPSEを算出することの意義が示された。
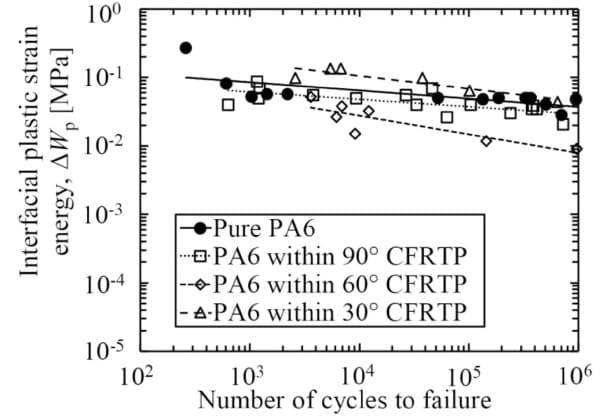
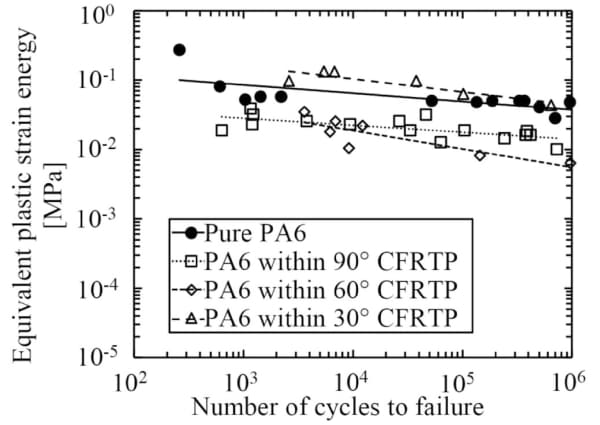
また参考に、Moritaら[12]が熱硬化性CFRPを対象に提案したINS評価手法による疲労線図をFig. 9に示す。PA6単体の疲労線図に比べて30° CFRTPは大きく乖離した。INS評価手法は弾性応力解析により得られる垂直応力を適用するものである。PA6は熱硬化性樹脂に比べて非弾性変形が顕著であり、正確な応力が求められなかったことが誤差の要因と思われる。また、30° CFRTPと60° CFRTP内部のPA6ではせん断応力が作用するが、INS評価手法ではせん断寄与による疲労損傷を考慮していないことも要因として考えられる。
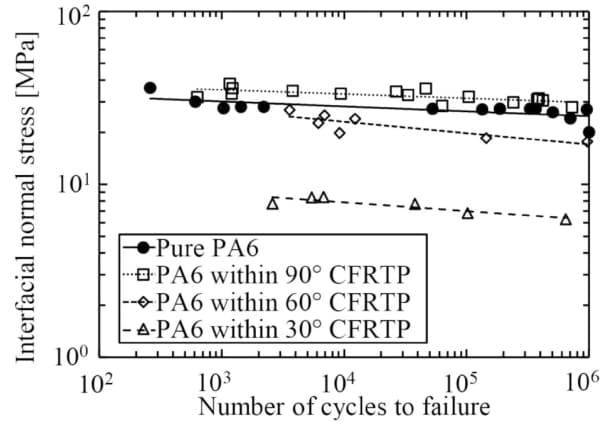
また、本研究で提案したIPSEと、相当塑性ひずみエネルギーを適用したEPSE(Equivalent Plastic Strain Energy)及び先行研究により提案されたINSを疲労寿命予測パラメータとした評価手法の予測精度を定量的に比較する試みを行った。Coffin-Manson則[27]により、樹脂単体の疲労線図はlogF を縦軸、logNを横軸とし、Aを傾き、Bを切片として、次式の一次関数で近似できる。
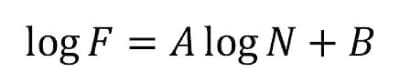
ここで、Fは疲労寿命予測パラメータであり、INS、EPSE、IPSEのいずれかを示す。Nは疲労破断サイクル数である。PA6単体の疲労線図に対する、各繊維配向のCFRTP内部のPA6の疲労線図の誤差は、次式の二乗平均平方根で求められる。

ここで、nは各繊維配向のCFRTPの疲労試験本数である。試験番号iの疲労寿命予測パラメータをFi、疲労破断サイクル数をNiとする。RMSの単位はlogFの単位と同じであるため、INS、EPSEおよびIPSEでオーダーが大きく異なり、3条件のRMSを直接比較することは不適切である。そこで、疲労線図の傾きに対する予測誤差を比較するという考えのもと、RMS/Aとして無次元化した値を評価指標とした。INS、EPSEおよびIPSEの予測誤差をRMS/Aにより定量化して比較した結果をFig. 10に示す。このように予測誤差を定量的に見ても、IPSE評価手法は他の手法と比べて予測誤差が小さいことが確認できた。
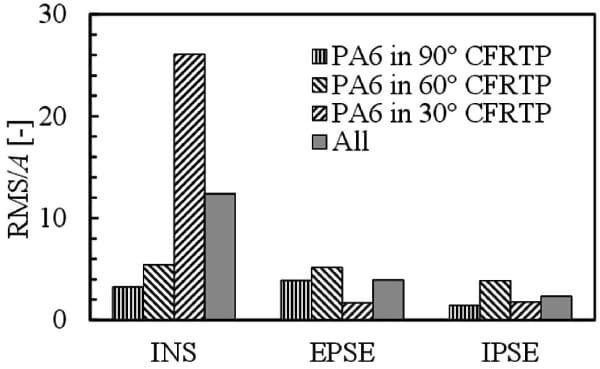
4. 総括
本研究では熱可塑性樹脂であるPA6を母材とした一方向CFRTP試験片に関して、Interfacial Normal Stress(INS)に代わる塑性ひずみエネルギー規準としてInterfacial Plastic Strain Energy(IPSE)を設定し、その疲労寿命予測に対する有効性を検証した。CFRTP内部のPA6は高い静水圧を受けるため、Drucker-Prager降伏条件を適用した。そしてツースケール解析により、CFRTP試験片のマクロ応力を正確に予測し、ミクロスケールにおける局所的な力学場からIPSEを算出する手法を提案した。
一軸引張試験と一軸圧縮試験から得られた内部摩擦角を適用して、CFRTP内部のPA6の塑性ひずみエネルギーを算出した。そして、疲労試験により得られたS-N線図をΔWp-N線図に変換し、PA6単体とCFRTP内部のPA6の疲労線図を比較した。その結果、これらの疲労線図はよく一致しており、PA6単体の疲労試験結果からIPSE評価手法を適用することで、CFRTPの疲労寿命が高精度に予測できることが示された。
参考文献
- T. Ishikawa: Overview of Carbon Fiber Reinforced Composites (CFRP) Applications to Automotive Structural Parts, -Focussed on Thermoplastic CFRP-, Journal of the Japan Society for Precision Engineering, 81, 6(2015), 489-493.
- M. Yamane, I. Ohsawa, K. Uzawa, T. Matsuo and J. Takahashi: Possibility of Repeated Recycling of CFRTP for Mass Production Automotive Application, 15th European Conference on Composite Materials, Venice, Italy(2012)24-28.
- M. Shokrieh, M. Esmkhani, F. Taheri-Behrooz: A Novel Model to Predict the Fatigue Life of Thermoplastic Nanocomposites, Journal of Thermoplastic Composite Materials, 28, 11(2013)1496-1506.
- J. Yang, G. Kang, Y. Liu, K. Chen, Q. Kan: Life prediction for rate-dependent low-cycle fatigue of PA6 polymer considering ratchetting: Semi-empirical model and neural network based approach, International Journal of Fatigue, 136(2020)105619.
- R. Shrestha, J. Simsiriwong, N. Shamsaei, R. D. Moser: Cyclic deformation and fatigue behavior of polyether ether ketone(PEEK), International Journal of Fatigue, 82, 3(2016)411-427.
- G. Hartwig, S. Knaak : Fatigue behaviour of polymers, Cryogenics, 31, 4(1991)231-233.
- Y. Ma, Y. Zhang, Toshihide Sugahara, Shanshan Jin, Yuqiu Yang, Hiroyuki Hamada: Off-axis tensile fatigue assessment based on residual strength for the unidirectional 45° carbon fiber-reinforced composite at room temperature, Composites: Part A, 90(2016)711–723.
- S. Kobayashi, K. Terada, N. Takeda: Evaluation of long-term durability in high temperature resistant CFRP laminates under thermal fatigue loading, Composites: Part B, 34(2003)753–759.
- A. Plumtree & G. X. Cheng: Fatigue damage parameter for off-axis unidirectional fibre-reinforced composites, International Journal of Fatigue, 21, 8(1999), 849-856.
- J. Petermann, A. Plumtree: A unified fatigue failure criterion for unidirectional laminates, Composites Part A: Applied Science and Manufacturing, 32, 1(2001), 107-118.
- A. Varvani-Farahani, H. Haftchenari, M. Panbechi: An energy-based fatigue damage parameter for off-axis unidirectional FRP composites, Composite Structures, 79(2007)381–389.
- N. Morita, Y. Mino, N. Yoshikawa, M. Hojo: Versatile fatigue strength evaluation of unidirectional CFRP specimen based on micro-stress analysis of resin, Composite Structures, 276(2021)114539.
- Y. Mino, N. Morita, N. Yoshikawa, M. Hojo: A versatile methodology for the fatigue life prediction of unidirectional carbon fiber-reinforced plastic specimens by the micro-stress analysis of resins, Journal of the Japan Society for Composite Materials, 47, 2(2021)73-79.
- M. Abe, N. Morita, N. Yoshikawa, M. Hojo: Fatigue life prediction of laminated CFRP based on micro stress analysis of resin, Journal of the Japan Society for Composite Materials, 48, 5(2022)183-190.
- M. Hojo, M. Mizuno, T. Hobbiebrunken, T. Adachi, M. Tanaka, S. K. Ha: Effect of fiber array irregularities on microscopic interfacial normal stress states of transversely loaded UD-CFRP from viewpoint of failure initiation, Composites Science and Technology, 69(2009)1726–1734.
- T. Hobbiebrunken, M. Hojo, T. Adachi, C. D. Jong & B. Fiedler: Evaluation of interfacial strength in CF/epoxies using FEM and in-situ experiments, Composites Part A: Applied Science and Manufacturing, 37, 12(2006)2248-2256.
- Y. Sato, S. Masumizu, K. Sakaue, J. Koyanagi, A. Ohtani and T. Sakai: Evaluation of viscoelastic non-isochoric plastic behavior of PBT and PA6, Mechanics of Time-Dependent Materials, 27(2022)829-841.
- J. Schijve: Fatigue of structures and materials in the 20th century and the state of the art, International Journal of Fatigue, 25(2003)679–702.
- J. P. Manaia, F. A. Pires, A. M. P. de Jesus, S. Wu: Mechanical response of three semi crystalline polymers under different stress states: Experimental investigation and modelling, Polymer Testing, 81(2020)106156.
- L. Xu, C. Cheng, C. Du, Z. Jiang, Z. Du, G. Gao: Semi-Crystalline Polymers Applied to Taylor Impact Test: Constitutive, Experimental and FEM Analysis, Polymers, 2020, 12, 1615.
- Y. Akita, N. Yoshikawa: Fatigue life prediction of unidirectional carbon fiber-reinforced thermoplastic specimens using the plastic strain range of resin, Journal of the Japan Society for Composite Materials, 49, 3(2023)82-90.
- S. Klee: Das zyklische Spannungs-Dehnungs und Bruchverhalten verschiedener Stätile, Veröffentlichungen des Instituts für Statik und Stahlbau der T. H. Darmstadt, Heft 22, in Germany(1973).
- V. M. Radhakrishnan: An Analysis of Low Cycle Fatigue based on Hysteresis Energy, Fatigue of Engineering Materials and Structures, 3(1980)75-84.
- D. Mounier, C. Poilâne, C. Bûcher, P. Picart: Evaluation of transverse elastic properties of fibers used in composite materials by laser resonant ultrasound spectroscopy, Acoustics(2012),1247-1250.
- D. C. Drucker, W. Prager: Soil mechanics and plastic analysis or limit design, Quarterly of Applied Mathematics, Vol. 10, No. 2(July 1952), pp. 157-165.
- W. A. Spitzig, O. Richmond: Effect of hydrostatic pressure on the deformation behavior of polyethylene and polycarbonate in tension and in compression, Polymer Engineering and Science, Volume19, Issue16, December 1979, Pages 1129-1139.
- S.S. Manson: Interfaces between fatigue, creep, and fracture, International Journal of Fracture Mechanics, 2(1966)327-363.