Based on more the 40 years of experience in contract development and manufacturning of intermediates and APIs, AGC continues robust supply of the product with quality control in compleance with cGMP.
AGC has extensive experience in general chemical reactions, halogenation reactions including fluorination, cryogenic reactions.
Service overview
AGC offers quality-controlled stable CDMO services for pharmaceuticals and intermediates levaraging our systematic management system.
AGC has a prolific track record in halogenation, including fluorination, and ultra low temperature reactions, and respond appropriately to the diverse needs of customers globally.
For contract development and manufacturing of pharmaceuticals, we have the plants in Chiba and Wakasa, Japan and the plant in Malgrat de Mar, Barcelona, Spain and we also handle risk dispersal using the multiple bases.
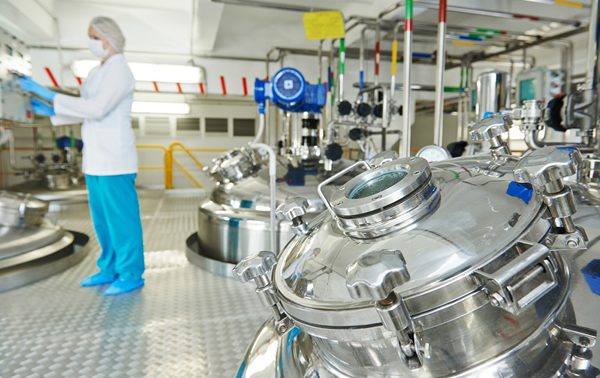
Features
- Fluorinated synthetic technologies -
AGC handles fluorinated synthetic technologies as follows:
- Various types of fluorinating agents (HF, F2 gas, nucleophilic / electrophilic fluorination agents)
- Innovative fluorination technology - PERFECT method* (* The method that converts arbitrary hydrocarbon compounds into perfluoro compounds)
- Use of plentiful fluorine-containing building blocks
- One-stop solution from development to manufacturing -
AGC is equipped with contract manufacturing capabilities able to handle various needs based on cooperation with group plants.
Wide ranging and flexible manufacturing is possible from lab schale to commercial manufacturing scale.
We are able to conduct contract manufacturing of high quality active pharmaceutical ingredients and intermediates based on efficient process development through the provision of a one stop solution from process development (non-clinical) to commercial manufacturing.
- cGMP compliance / FDA inspection experiences -
AGC offers high quality, stable production based on systematic management systems.
In response to requests, we also comply with cGMP plant manufacturing and FDA inspections.
- Global support system -
AGC has operating bases in Japan, U.S. (PA) and Spain.
We also can adequately support global contract manufacturing.
Manufacturing bases / equipment
<AGC Chiba Plant> (Ichihara City, Chiba Prefecture) *cGMP compliant
Equipment | Material | Volume | Number |
---|---|---|---|
Reactors | Glass Lining (GL) | 1,000 ~ 15,000L | 10 |
Hastelloy C | ~ 5,000L | 2 | |
SUS | 2,000 ~ 10,000L | 4 | |
Filter / Dryers | Glass Lining (GL),Hastelloy C,SUS | - | 8 |
Distillation Towers | SUS | 2,500 ~ 5,000L | 2 |
Micronizer | Jet mill (~8㎏/h),Pin mill (15~20㎏/h) | - | 2 |
Environment management level: The plant has manufacturing rooms with 100,000 particles / ft3
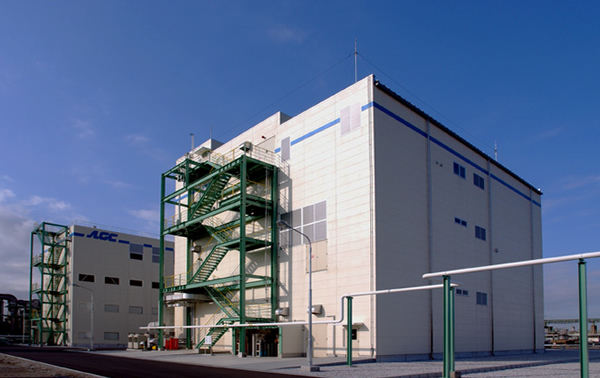
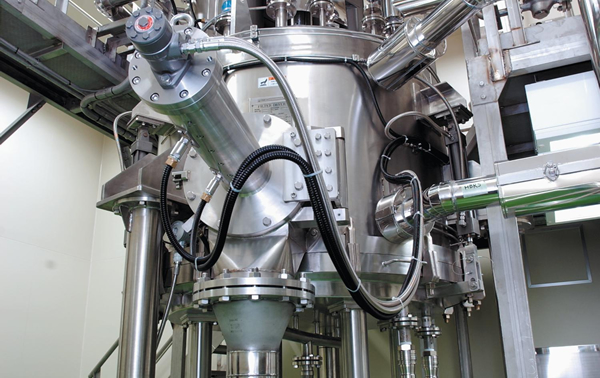
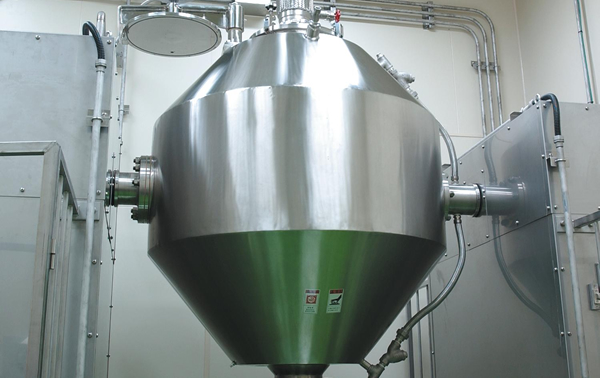
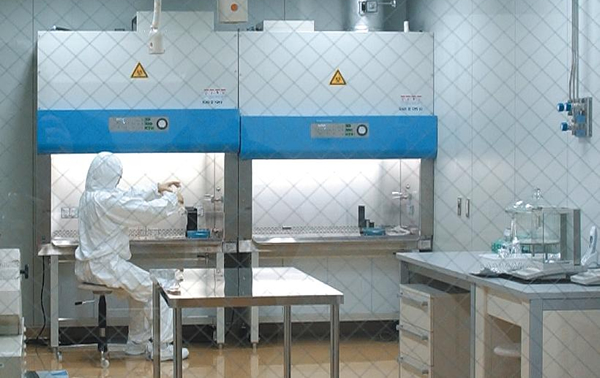
<AGC Wakasa Chemicals: Obama Plant / pharmaceuticals Plant>(Obama City, Fukui Prefecture)
AGC Wakasa Chemicals- cGMP compliant
- Starting materials and raw materials
Equipment | Material | Volume (L) | Numbers | Design Temp. (°C) |
---|---|---|---|---|
Reactors | SUS, Glass Lining,Hastelloy C, Resin | 100 to 5,000 | 45 | -50 to 210 |
Distillation Towers | SUS, Glass Lining | up to 2,000 | 2 | - |
Centrifugal separators | SUS, Resin | up to 48inch | 8 | - |
Mixed dryer | SUS, Glass Lining | 300 to 2,000 | 4 | - |
Filter dryer | SUS | 300 to 1,700 | 4 | - |
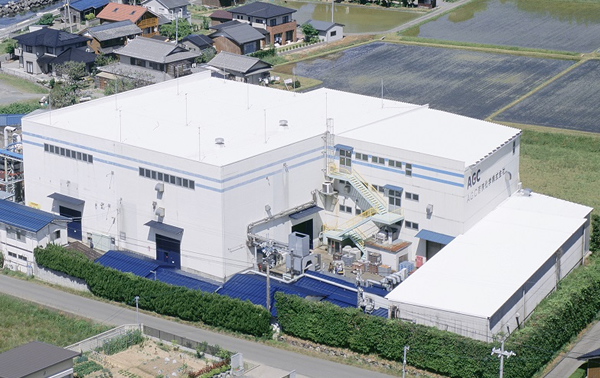
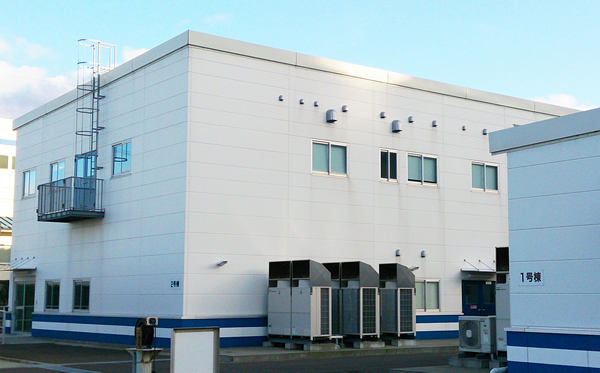
<AGC Wakasa Chemicals: Kaminaka Plant>(Wakasa-cho, Mikata Kaminaka-gun, Fukui Prefecture)
AGC Wakasa Chemicals- Intermediates and active ingredients
- Agrochemical CDMO
Equipment | Material | Volume (L) | Numbers | Design Temp. (°C) |
---|---|---|---|---|
Reactors | SUS, Glass Lining,Hastelloy C, Alloy | 200 to 14,000 | 49 | -45 to 250 |
Distillation Towers | SUS, Glass Lining | up to 8,000 | 7 | - |
Centrifugal separator | SUS, Resin | up to 48inch | 8 | - |
Mixed dryer | SUS, Glass Lining | up to 4,000 | 7 | - |
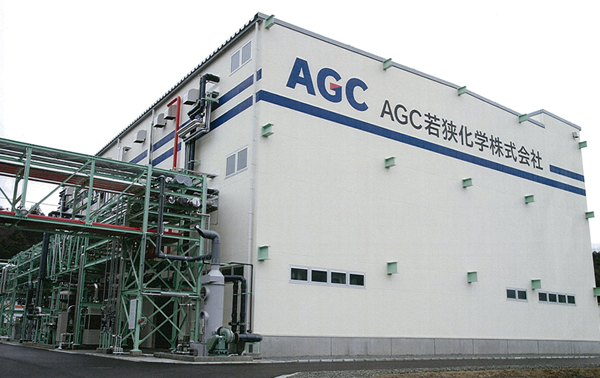
<AGC Pharma Chemicals Europe>(Malgrat de Mar, Barcelona, Spain)
AGC Pharma Chemicals Europe- cGMP compliant
- Designed to handle small molecule APIs from development phase to commercial scale
- Solid track record in Authority Inspections with no critical observations since 2007:
- ISO 14001:2015 and ISO 45001:2018 Certified
-6 times by FDA, latest 2023
-3 times by EMA, latest 2018
-8 times by PMDA, latest 2023
Equipment | Material | Volume (L) | Numbers |
---|---|---|---|
Reactor | Glass lined, Stainless,Hastelloy | up to 6,000 | 42 |
Distillation tower | Glass lined, Stainless | up to 6,000 | 5 |
Centrifuge | Stainless, Hastelloy,Halar coated | Φ 1 - 1.4m | 12 |
Paddle dryer | Stainless, Hastelloy | up to 3,500 | 6 |
Tumble dryer | Glass lined, Stainless,Hastelloy | 2,000 | 5 |
Filter dryer | Stainless, Hastelloy | up to 2,500 | 4 |
Thin layer dryer | Stainless | 4m2 | 1 |
Micronization unit | Stainless | OEB4 (1 to 10 μg/m3) | 1 |
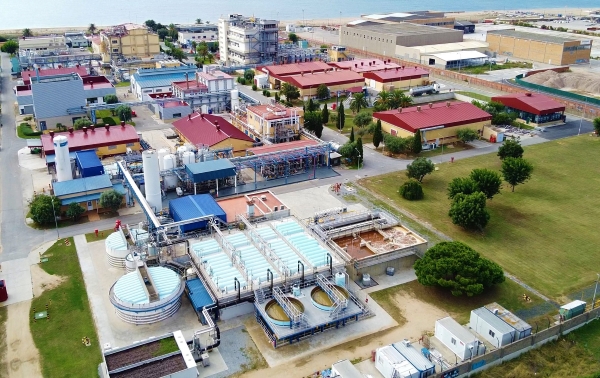
Special technology
AGC is a fluorine chemical manufacturer with vast experience in fluorine chemistry and is equipped with world leading technological and production capabilities able to handle the 4 main halogens. We have a prolific track record in halogenation, including fluorination, and ultra low temperature reactions, and respond to the diverse needs of customers.
Fluorination Technology
Diazo-fluorination, Electrophilic fluorination etc.
Building blocks with “F” Components
ClCHF2, Tetrafluoroethylene derivatives, Fluorine containing gas components
Hazardous Reactions
Cyanide chemistry, Diazotization
General Organic Reactions
Grignard reaction, Lithiation, Cross-coupling, Amidation, Friedel-crafts
Oxidation/Reduction
TEMPO, NaOCl oxidation, LAH, Vitride, Silane reduction
- Hydrogenation Reactions
- Ultra-low Temperature Reactions (<-100℃)
- High Potent API (OEL:1-10μg/m3)
- Distillation(GMP)
- Pulverization(Jet/Mechanical mill)
Environment measures
AGC has activated sludge waste water treatment equipment, HF-containing waste gas treatment equipment and organic fluorine compound incineration equipment.
cGMP
AGC offers contract manufacturing of cGMP-compliant high order intermediates and active pharmaceutical ingredients.
We are also able to handle ultra low temperature (-100°C) reactions and reactions at high pressure (0.99 MPa) under GMP, and are able to pack out products in manufacturing clean rooms with an environment management level of 100,000 particles / ft3.
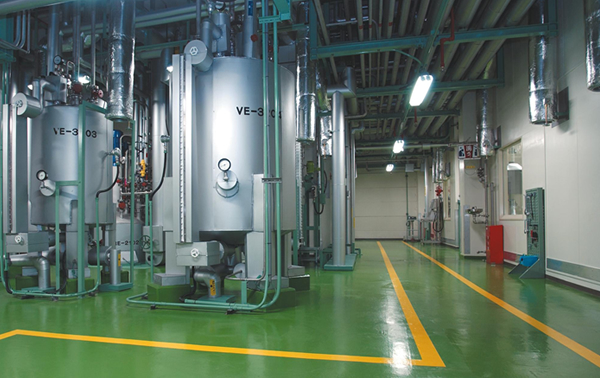
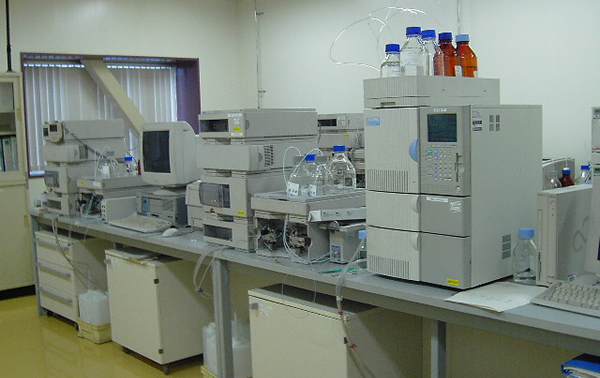
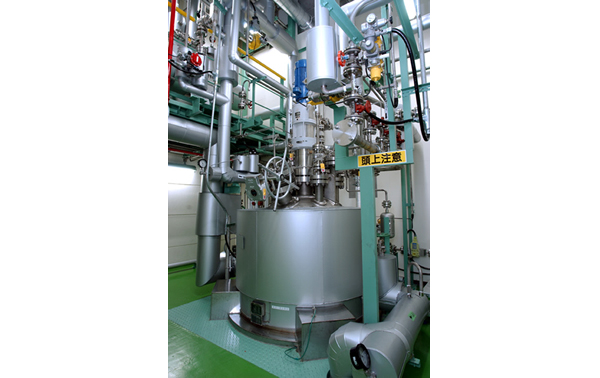