The ion-assisted deposition (IAD) method achieves denser and harder coatings than those by vacuum evaporation and ion plating. By forming dense Y2O3 coatings and Y5O4F7 coatings, this product helps extend the lifespan of equipment components and improve product yield.
Applications
- Top plate and side walls of chambers of etching equipment
- Top plate and side walls of chambers of deposition equipment
- Stage and heater components
- Viewing window
Features
- Achieves dense, high hard coating quality by the ion-assisted deposition (IAD) method. Helps improve product yield by extending the lifespan of components and reducing particle generation.
- Capable of forming coatings on large-area insulating and conductive substrates (up to a diameter of 750 mm), which is difficult to achieve by vacuum evaporation and ion plating.
- Achieves approximately 100* times higher plasma resistance properties than thermal spraying, extending the lifespan of components. (*According to our research)
Increases durability and reduces particle generation in severe plasma environments
When used for coating various components of chambers of etching equipment and various deposition equipment, high durability and particle reduction can be expected, especially in environments where plasma is generated.
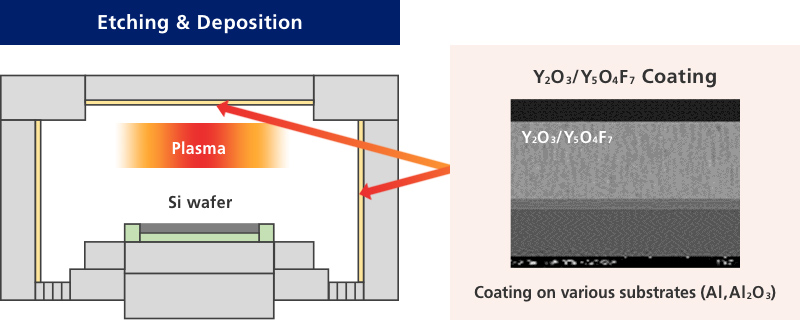
What is the ion-assisted deposition (IAD) method?
In comparison to conventional thermal spraying, vapor-phase synthesis can deposit films with high hardness and density. Among various vapor-phase synthesis, the IAD method makes it possible to form dense coatings on large-area insulating or conductive substrates, which is difficult to achieve by vacuum evaporation or ion plating. It forms coatings on large substrates with a maximum diameter of 750 mm.
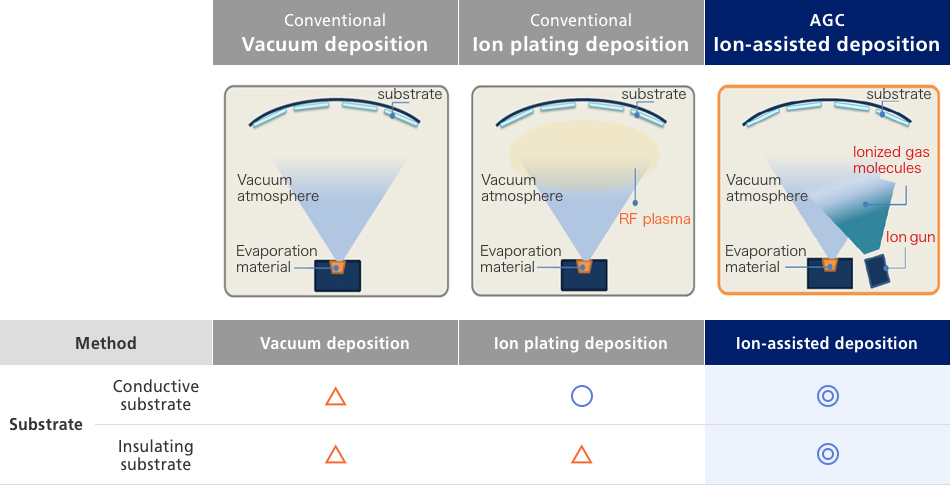
Helps extend the lifespan of equipment components and improve product yield
Unlike thermal spraying, it forms coatings at the atomic level, resulting in dense, high hard coatings. The coatings have high corrosion resistance in environments requiring plasma resistance, extending the lifespan of equipment components and reducing maintenance costs. Additionally, the capability to form dense coatings reduces particle generation, improving yields in manufacturing processes.
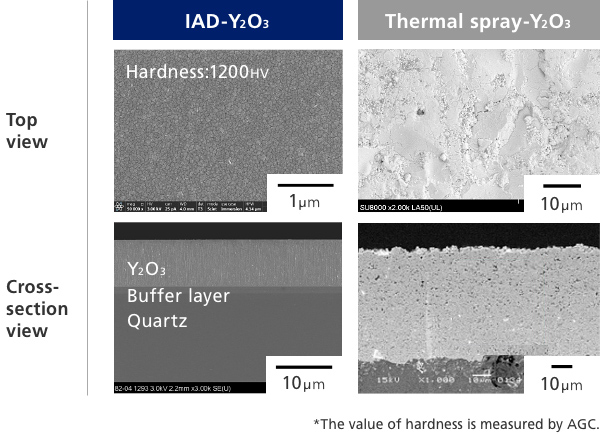
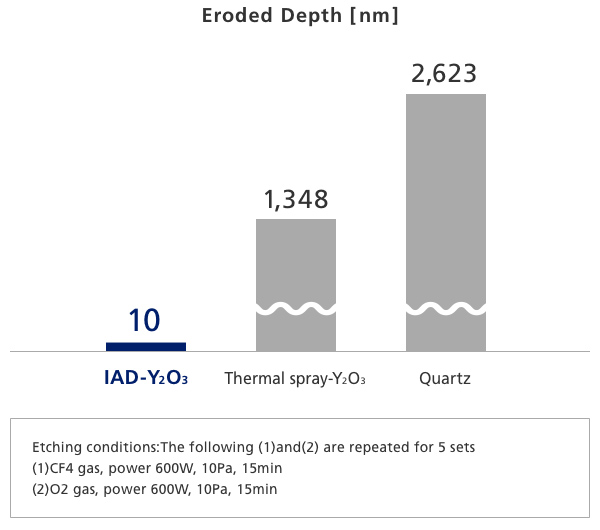