Structure and principle of LiDAR
A light detection and ranging (LiDAR) system is a kind of range-finding sensor that emits laser beams to an object and detects the beams reflected back. The mainly used system is the time of flight (ToF) system, in which the time between emitting a laser beam and its return is measured. Making use of the fact that light travels at about 300,000 km per second, this method calculates distances by measuring how long it takes for the beams to return after hitting the object. Other than that, a triangular range finding system that simply measures the distance to the object is also used. LiDAR is widely used for 3D surveying in the field of construction and vacuum-cleaning robots. Recently, however, there has been a growing need for 3D mapping and measurement of surroundings in the areas of ADAS/autonomous driving, AR/MR glasses and smartphones, and LiDAR has been attracting a great deal of attention.
LiDAR serves as the eye of a machine or device, but it generally uses near-infrared rays, which are invisible to the human eye. As the light source, it uses a laser, which allows collimated light beams to fly straight without diverging. Sunlight and light in the room can become noise, but since the beams that are used in LiDAR have a higher monochromaticity and peak light intensity, the system can increase the detection sensitivity by filtering out unnecessary light. In addition, by modulating the beams used for detection, the system can identify the beams that are reflected back. Thus, LiDAR devices take advantage of the fundamental properties of laser beams, such as directivity, monochromaticity, coherence, controllability, and high energy density.
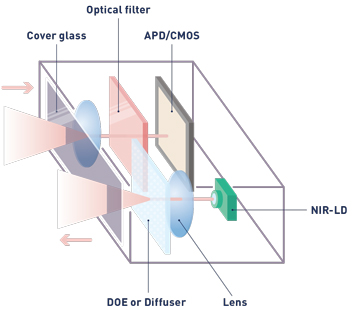
The beam irradiation methods used in LiDAR systems are categorized as shown in the figure. To create a 3D map, LiDAR irradiates laser beams repeatedly and detects the reflected beams to spatially scan the surroundings. That means, laser beams need to be irradiated over a wide angular range.
LiDAR systems are roughly categorized into a scanning system and non-scanning system; in the former, scanning is performed with collimated straight beams, whereas in the latter one, beams are irradiated over a wide area in a flash. The scanning type system has a driving part in it, and the device is rotated together with its housing in some systems, whereas in other systems, a polygon mirror rotates in them. In micro electro mechanical systems (MEMS), a micro mirror produced with micro-processing technology is driven by an electromagnetic force, and the traveling direction of incident beams is controlled by the mirror to scan the object. The optical phased array system, which controls the traveling direction by modulating the phase of beams, has also been proposed. On the other hand, the flash method is a non-scanning system. Here, laser beams emitted from the source are diffused by an optical element to irradiate over a wide angle in a flash. Of course, LiDAR systems are not classified exactly as shown in the figure, and combinations of multiple methods and new methods have also been proposed.
As regards the scanning angle, the system in which the housing also rotates together can scan the surroundings up to 360 degrees. In other systems such as polygon mirrors, MEMS, optical phased array, and flash, the angle range to which beams are irradiated is smaller than 180 degrees, although it depends on the optical system. Thus, we need to select an appropriate system according to the purpose of the LiDAR. The scanning distance varies from several centimeters to several hundred meters depending on the object. In any LiDAR system, it is important to reduce moving parts as much as possible and to project laser beams over a wide range in an effective manner.
Light is a form of electromagnetic wave, and each type covers a range of wavelengths (the length of a period of electromagnetic waves). Human eyes can generally sense only light in the wavelength range called visible light rays, but optical glass and its processed products handle a wide range of light rays, including X-rays and microwaves, depending on the application.
Applications of LiDAR
LiDAR has been receiving attention in the field of consumer electronics such as ADAS/autonomous driving, AR/MR glasses, and smartphones. This section introduces AGC’s products for LiDAR in each field. Details about DOE/diffusers and package substrates for semiconductor lasers (GCHP™) are described later.
ADAS/Autonomous driving
LiDAR creates a 3D map of measured data (point group) to provide a high-resolution picture of the surrounding environment. In ADAS, it is used to measure the distance from the car ahead and to detect obstacles.
Autonomous cars are driving on roads, which are actually in the 3D map developed from the measured data. To get an accurate picture of where the car is in the 3D map, a 360-degree LiDAR is used. The car combines existing 360-degree 3D information, including roads and surrounding buildings, with information it captures to estimate its exact location on the road in the 3D map.
Although there are challenges that must be overcome, such as interference with sunlight and other sensors and the influence of rain, fog, etc., new systems are being developed. In many cases, a number of sensors are installed by combining radar, cameras and other sensors to cope with various situations. AGC has a broad lineup of LiDAR components and products used in ADAS.
Consumer electronics
Another notable application of LiDAR is AR/MR glasses. AR and MR stand for augmented reality and mixed reality, respectively, and they superimpose digital images on the real world. Photos and videos shot with ordinary cameras contain only two-dimensional information, but to superimpose digital information on a three-dimensional image, it is necessary to obtain 3D data about the surroundings. Smart glasses, smartphones, and tablet PCs use range-finding devices to provide users with a natural AR/MR experience, which can be achieved by instantaneously collecting 3D data around them.
As the range-finding devices, stereo cameras, structured light, ToF and LiDAR systems are used. Stereo cameras are used in a set of two and measure the distance from the parallax of two images. A structured light projects a pre-designed pattern onto an object from a light source and another camera shoots the image. The projected pattern distorts along the shape of the object, and this enables the structured light to calculate the 3D shape of the object. ToF is a range-finding system that measures how long it takes for a beam to reach the object and to return back, and is sometimes not distinguished from LiDAR systems. However, while a ToF sensor sometimes refers to a proximity sensor used for close distances, a LiDAR system often refers to a sensor that measures a longer distance over a wider area, so there is a slight difference in nuance between the two systems. Each range-finding system has its own merits, so an appropriate method is chosen according to the application.
If LiDAR and ToF systems are used in consumer electronics with camera functions, besides for the purposes of enhancing AR/MR experience, to understand the distance from the subject, autofocus, and correct images, such as making the depth of field shallow, their applications will expand further.
AGC's products used in LiDAR
A LiDAR system is composed of an emitter that emits signal beams from a laser source, a receiver that detects the reflected beams with a sensor, housing, and internal components such as a control system and a drive mechanism. Here, we will introduce our products to be used in each of the emitter, receiver and housing.
Emitter: DOE/diffuser, aspherical mold lens, glass ceramic substrate (GCHP™),
Receiver: optical filter, aspherical mold lens
Housing: cover glass
DOE/Diffusers
They are optical components that are used to diffuse the near-infrared semiconductor laser beams (NIR-LD) emitted from the emitter over the intended scanning area and to obtain the intended beam intensity distribution. Our proprietary design and manufacturing processes realize characteristics such as a high diffusion angle and high efficiency. These optical components are used not only in LiDAR systems but also in other 3D sensing systems such as the structured light and ToF systems described above.
A diffractive optical element (DOE) uses the diffraction of laser beams to convert laser beams into an arbitrary pattern. A diffuser uses the refraction of beams to diffuse laser beams into the target area. With AGC’s technology of manufacturing optical elements using only inorganic materials, it can provide products that are highly resistant to lasers. LiDAR systems must be able to detect over long distances in daylight conditions. AGC’s products ensure a highly reliable performance even when handling laser beams with high peak intensity.
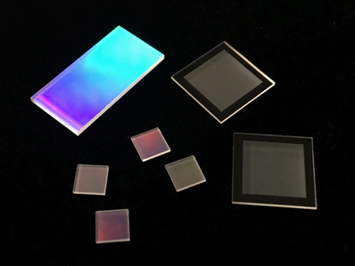
Glass ceramic substrates for semiconductor laser packages (GCHP™)
They are used as package substrates for semiconductor lasers which serve as light sources of emitters. Glass ceramics hybrid package (GCHP™) is a new glass-ceramic hybrid package substrate that has been developed by combining low-temperature co-fired ceramics (LTCC) technology and AGC's glass material technology. LiDAR systems require high output to measure long distances with high sensitivity. Our proprietary heat sink structure can efficiently release heat generated from the element. GCHP™ enables designs that effectively dissipate heat even when applied to high-power semiconductor lasers such as edge emitting lasers (EELs), surface emitting lasers (SELs) and vertical cavity surface emitting lasers (VCSELs).
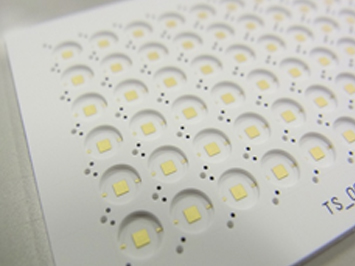
Aspherical glass mold lenses
They are used in both the emitter and the receiver. Lenses play various roles: producing collimated laser beams that can travel a long distance, diffusing beams toward a wide scan area, and collecting reflected laser beams to a sensor. AGC uses the press molding method to produce lenses. The lenses produced by this method are called glass mold lenses because in this method, glass material is placed in a precision-processed metal mold, heated until it softens and then pressed. This method is suited for volume production and reduces cost during the mass production. Depending on the type of metal mold, glass material, and molding process selected, the shapes that we can form vary, so please contact us for details.
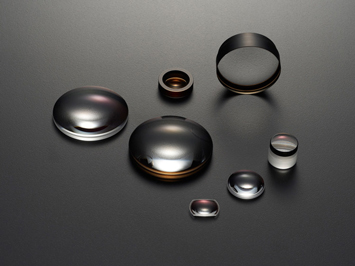
Optical filters
They are used in receivers. In LiDAR systems, light other than reflected beams (sunlight, illumination light, etc.) are sources of noise and must be screened out with optical filters. The detection sensitivity can be enhanced by transmitting only near-infrared rays emitted from a semiconductor laser.
Optical filters consist of multilayer dielectric films, each of which has a refractive index different from one another. Such filters can selectively transmit beams with specific wavelengths by making use of the interference phenomenon of reflected beams generated at the interfaces of the thin films. In this way, they can narrow the transmission band and achieve a clear contrast. They can be applied to wider wavelengths, transmittance, and, stopbands, etc.
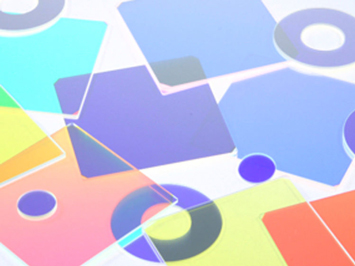
Cover glass
Cover glass is used for housing to protect the emitter and receiver from the external environment. Details are provided below.
Required properties
If a LiDAR for automotive applications is installed on the exterior of the vehicle, the cover glass should have the following properties.
- High infrared transmittance
- Impact resistance
- Heat resistance
High infrared transmittance
The laser used in LiDAR is near-infrared, Therefore, high infrared transmittance is required for the cover glass. AGC's cover glass has an advantage in terms of infrared transmittance compared to resin covers.
Impact resistance
If a LiDAR for automotive applications is installed on the exterior of the vehicle, the cover glass is required to be tough enough to withstand harsh environments such as sudden temperature changes, rain and wind, as well as flying stones. AGC's cover glass is more scratch-resistant than resin covers. In particular, AGC glass (EG-A1) for cover glass is more resistant to cracking than general glass, and is also ISO and SAE compliant. Therefore, it can be used for a longer time.
Heat resistance
In cold environments, snow and frost can pile up on the cover glass and block the laser, resulting in areas that are not detectable by LiDAR. AGC's cover glass can be equipped with a heater to have anti-fogging, defrosting and snow-melting functions.
Customizable
AGC's cover glass has the above properties required for automotive LiDAR. And it has already been adopted by a LiDAR manufacturer. If you have any requests for cover glass for LiDAR systems or cameras, please feel free to contact us.
Glass materials
AGC develops and manufactures glass materials according to customer requests and specifications. AGC conducts in-house everything from materials development to processing, molding, coating, installation of heater, and evaluation. AGC has realized the high infrared transmittance and impact resistance of the cover glass for LiDAR systems and cameras by accumulating and utilizing our huge amount of data. AGC offers not only cover glass, but also glass materials that meet the customer's usage and needs, so please feel free to contact us.
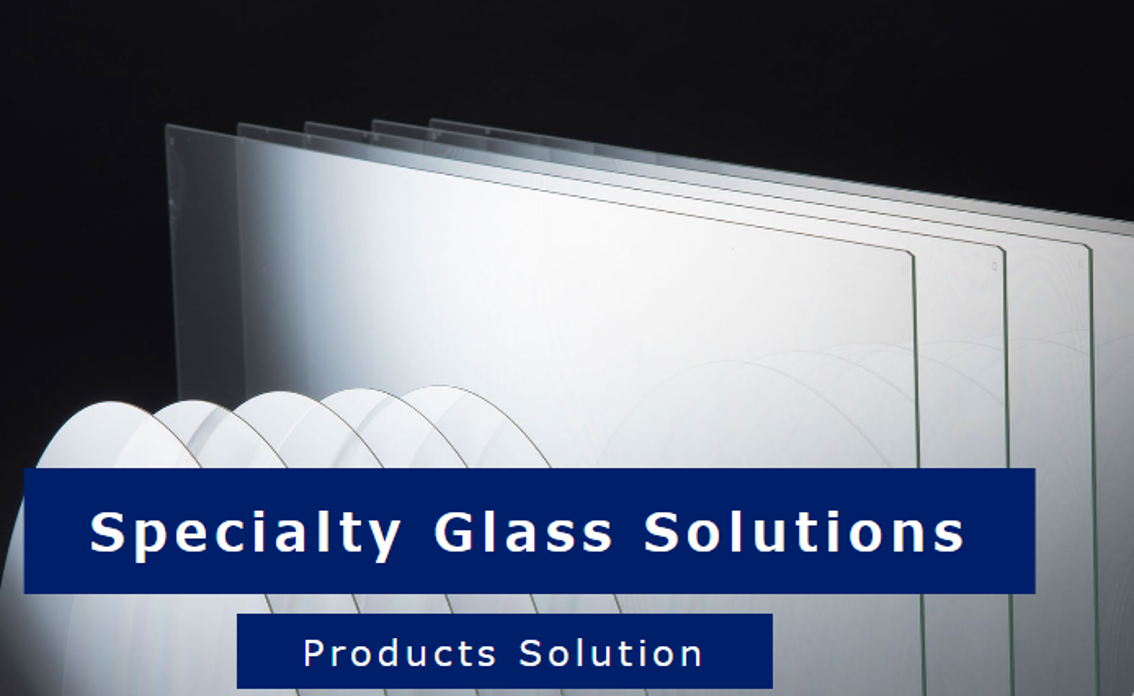
Black type
When LiDAR systems are not used in combination with a window, they do not have to allow visible light through them, and the color of the cover glass can be black. In addition to glass strength evaluation and various processing, AGC has know-how in coating on glass, heater design, and technologies to incorporate a heater into glass. Please feel free to contact us.
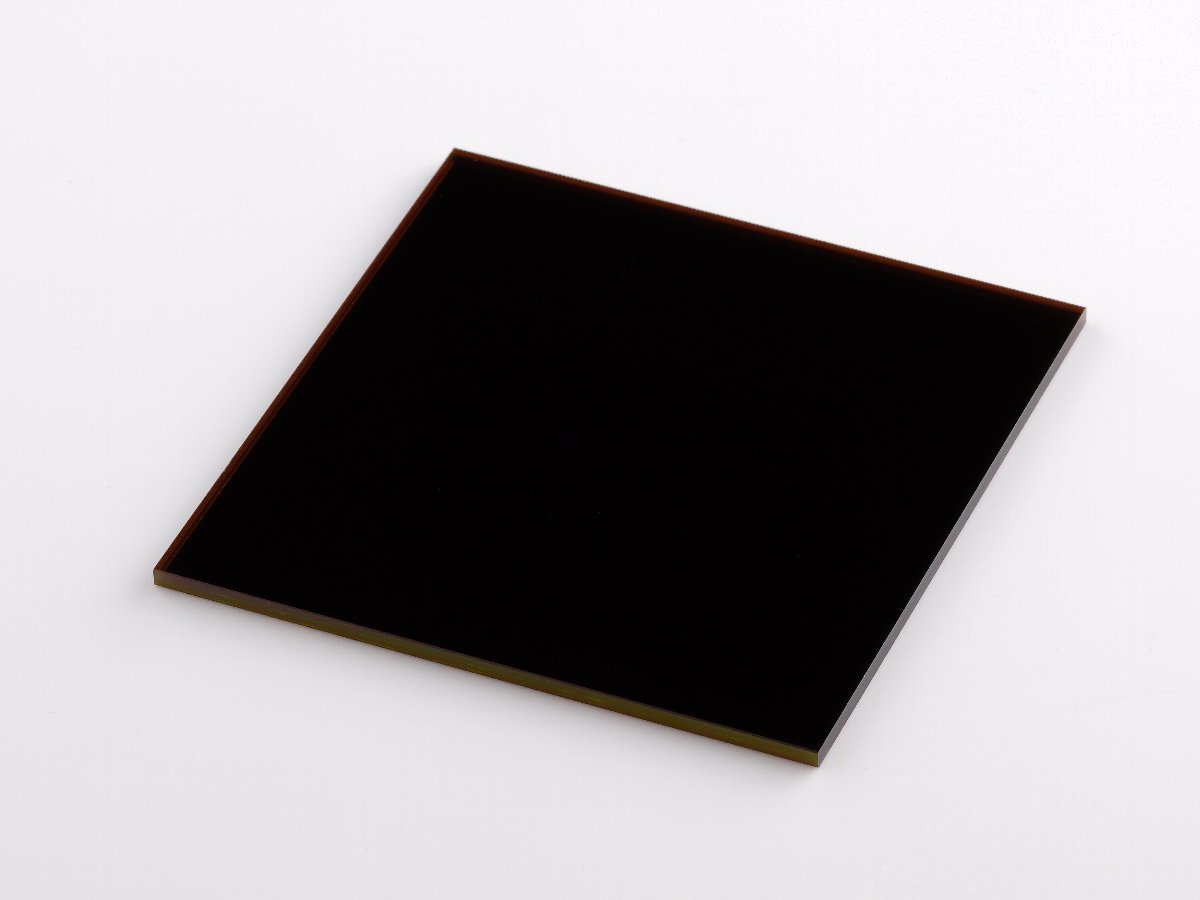
High strength type
It has high resistance to stone impact and supports various (stone impact) standards. It has excellent optical properties and environmental resistance, so it can be used not only for in-vehicle LiDAR, but also for in-vehicle cameras and various sensing devices. You can design high performance, robust sensing devices. Please feel free to contact us.
Wideye Project
When installing LiDAR inside of a car, sensing is performed through a window such as windshield. In our Wideye Project, AGC uses high infrared transmission glass in the windshields.
Application 1: DOE, diffuser
Applicable Products
A LiDAR system is required to scan the beams emitted from the emitter accurately and over a wide area. The figure shows differences among the scanning methods of LiDAR systems. In the scanning system, collimated beams are projected over a long distance, while in the flash system, laser beams are diffused spatially to measure and collect information over a wider range in a flash. Optical elements such as DOE and diffusers are used in combination with lenses and other optical systems to obtain arbitrary patterns and intensity distributions of light. Since the projection pattern of light beams also affects the scanning time and sensitivity, various patterns have been studied: patterns with a smaller or larger range of projection angles, and patterns with various numbers or distributions of dots.
■ Scanning LiDAR
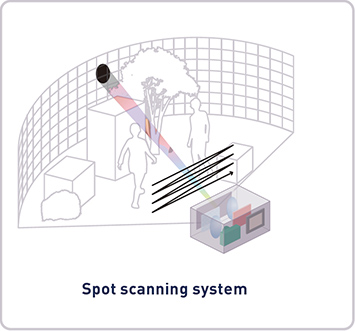
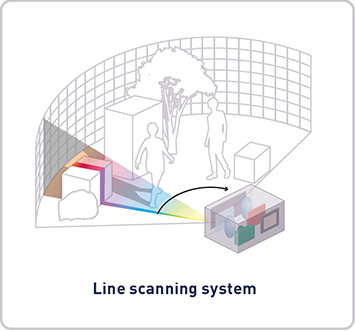
■ Flash LiDAR
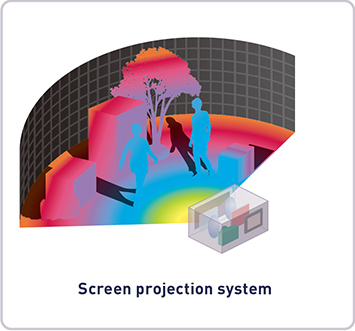
LiDAR systems scanning their surroundings using laser beams. In the scanning system, collimated beams are projected to scan the area and obtain three-dimensional dot group data of the area. In the line scanning shown in the middle, laser beams are vertically or horizontally diffused by an optical system or a dot group is formed in advance, and the laser moves laterally to scan the target. In the flash system, laser beams are emitted toward all of the directions of the area in a flash to obtain data at a time.
AGC combines its optical design technology and glass micro-processing technology to produce diffractive optical elements (DOE) and glass diffusers. DOE and diffusers are suitable optical elements for controlling laser beams. When they are used in long-distance LiDAR systems, in which resistance to lasers and reliability even under a harsh environment are required, such as those used in cars, inorganic materials like glass are suitable.
Application 2: Ceramic package substrates for semiconductor lasers
Applicable Products
LiDAR systems must be able to project laser beams over a long distance in sunlight during the daytime and in the presence of external light such as illumination light in rooms. To ensure sufficient signal light intensity, high power is sometimes used. Therefore, package substrates need to be able to dissipate heat. AGC has developed GCHP™, a new substrate, by combining AGC’s glass technologies and ceramics technologies. The substrates were originally used as package substrates for high-power and high-brightness LEDs and LED headlamps that are used in automotive applications, and they needed to pass stringent environmental tests. However, having a high heat releasing performance, durability, and airtightness, they are highly evaluated also as package substrates for semiconductor lasers which are used as the light sources of LiDAR systems, since they are also required to have high reliability.
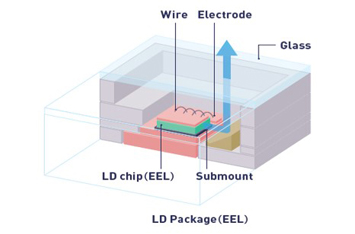
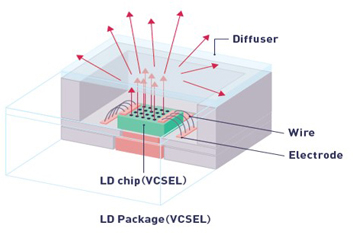
AGC has a consistent system to manufacture glass ceramic substrates (GCHP™), from glass materials to the final substrates. The vertical cavity surface emitting laser (VCSEL), which has been spotlighted by its use in 3D sensing in autonomous driving systems, etc., is required to have high heat releasing performance and reliability, and is one of the suitable applications of GCHP™. The high heat releasing performance of the material, its highly reliable characteristics, and the LTCC technology enable internal wiring. These points will be explained.